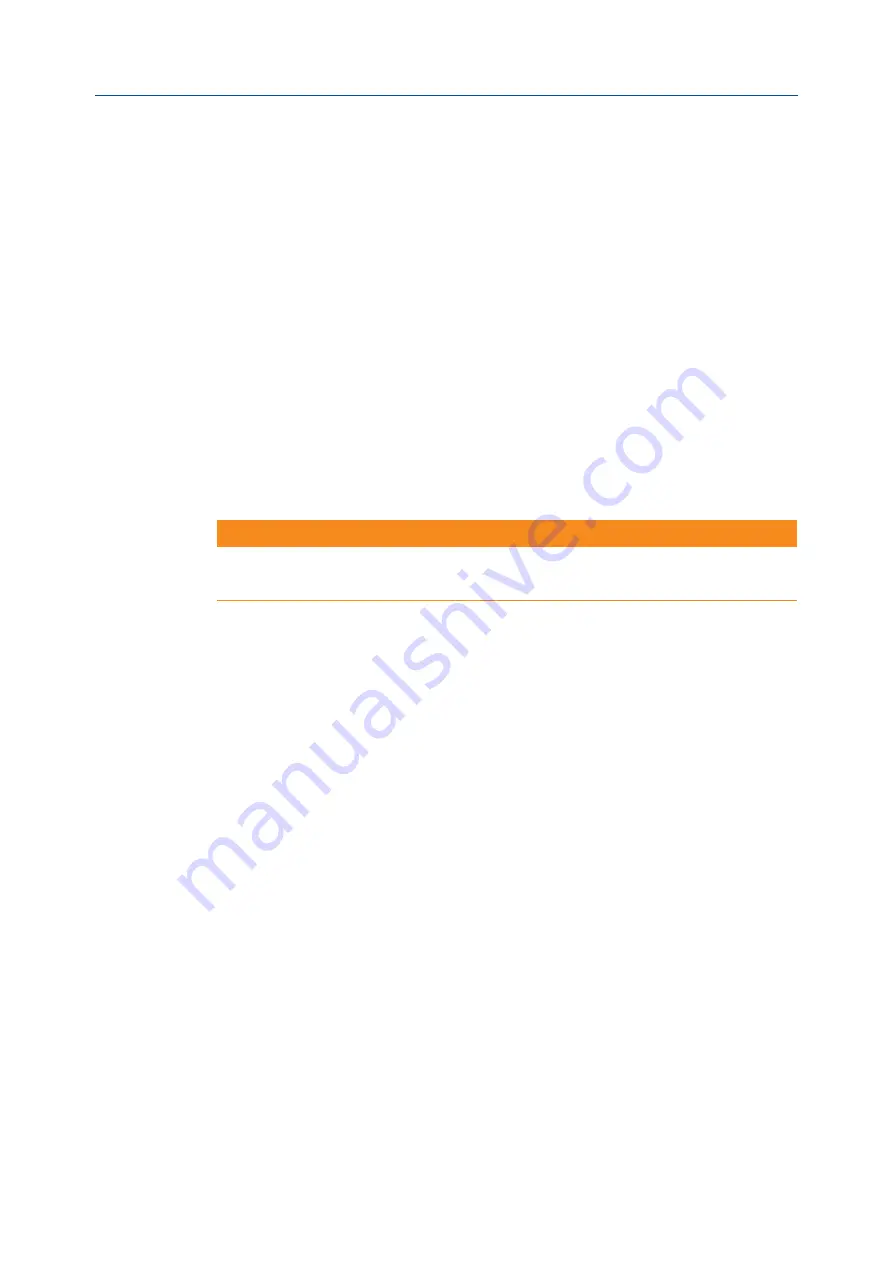
July 2020
Installation, Operation and Maintenance Manual
MAN 573 Rev. 8
2.5
Pneumatic Connections
Connect the actuator to the pneumatic feed line with fittings and pipes in accordance to the plant
specifications. They must be sized correctly in order to guarantee the necessary air flow for the
operation of the actuator, with pressure drops not exceeding the maximum allowable value.
The shape of the connecting piping must not cause excessive stress to the inlets of the actuator.
The piping must be suitably fastened so as not to cause excessive stress or loosening of threaded
connections, if the system undergoes strong vibrations.
Every precaution must be taken to ensure that any solid or liquid contaminants which may be present
in the pneumatic pipe-work to the actuator are removed to avoid possible damages to the unit or loss
of performance. The inside of the pipes used for the connections must be well cleaned before use:
wash them with suitable substances and blow through them with air or nitrogen.
The ends of the tubes must be well deburred and cleaned. Once the connections are completed,
operate the actuator and check that it functions correctly, that the operation times meet the plant
requirements and that there are no leakages in the pneumatic connections.
2.6
Electrical Connections (If any)
!
WARNING
The connections should be made by qualified staff. Before carrying out any operation, cut line power
off. Safety provisions as per CEI 64-8 regulation should be complied with (same as IEC 60364).
Connect the electrical feed, control and signal lines to the actuator, by linking them up with the
terminal blocks of the electrical components. In order to do this, the housing covers must be
removed without damaging the coupling surfaces, the O-rings or the gaskets. Remove the plugs
from the cable entries. For electrical connections use components (cable glands, cables, hoses,
conduits) which meet the requirements and codes applicable to the plant specifications (mechanical
protection and/or explosion-proof protection). Screw the cable glands tightly into the threaded
inlets, so as to guarantee the weatherproof and explosion-proof protection (when applicable).
Insert the connection cables into the electrical enclosures through the cable glands and connect
the cable wires to the terminals according to the applicable wiring diagram. If conduits are used,
it is advisable to carry out the connection to the electrical enclosures by inserting hoses so as not
to cause anomalous stress on the housing cable entries. Replace the plastic plugs of the unused
enclosure entries by metal ones, to guarantee perfect weatherproof tightness and to comply with
the explosion-proof protection codes (where applicable). Once the connections are completed,
check that the controls and signals work properly.
Installation
12
Section 2: Installation