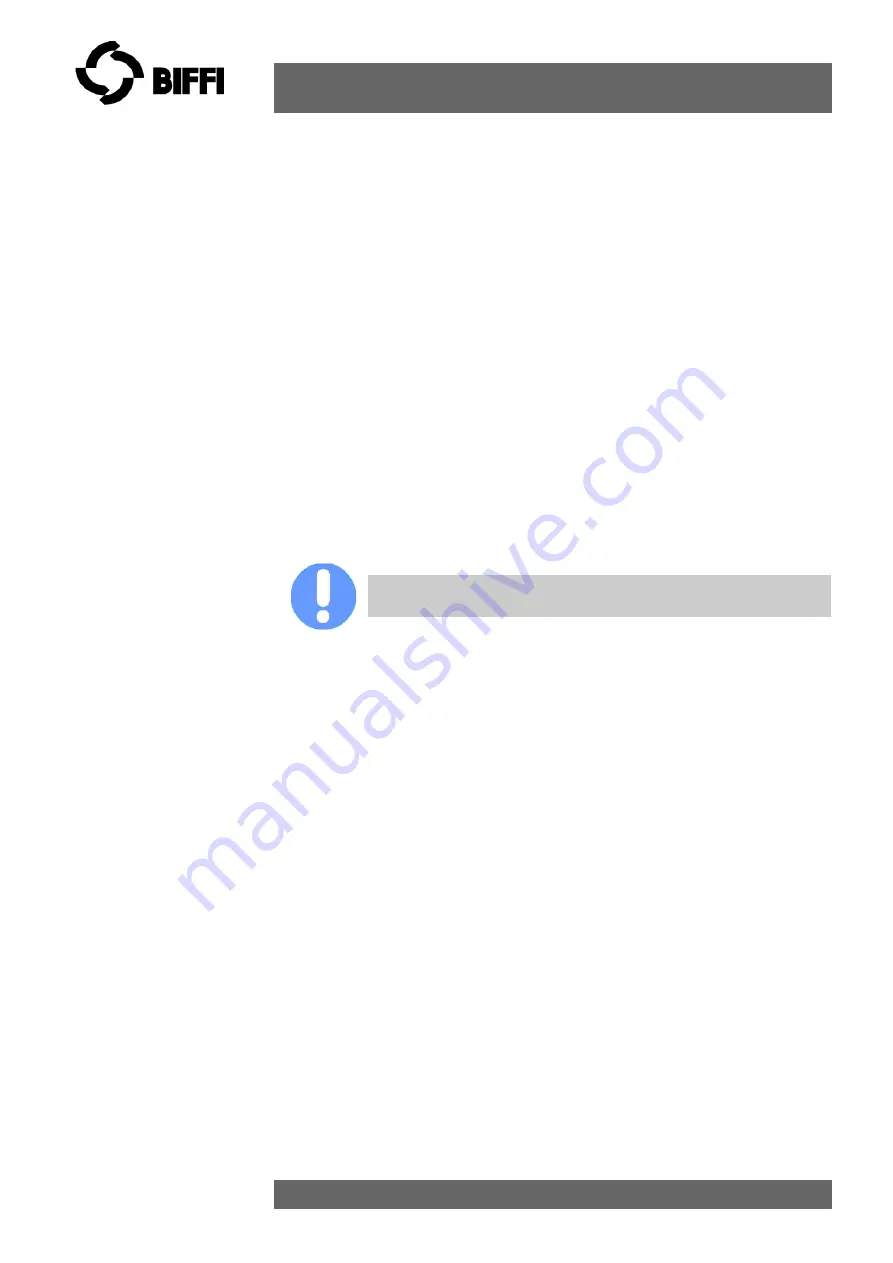
OLGAS-H
– High pressure spring return hydraulic actuator
Use and maintenance manual
© Copyright by BIFFI Italia. All right reserved.
Pag. 39
Contents may change without notice
5) Assemble the end flange by centring it on the inside diameter of
the tube, taking care not to damage the O-ring (50).
6) Assemble the nuts (28) onto the tie rods (19). Tighten the nuts to
the recommended torque, alternating between opposite corners.
7) Restore a generous coating of grease on the contact surfaces of
the yoke (11) and the bushings (41), on the yoke grooves, on the
sliding blocks (39), on guide bar (9).
8) Assemble the new gasket (10) after cleaning the surfaces of the
housing (8) and cover (35)
9) Lubricate with protective oil the O-ring (40).
10) Assemble the cover (35) and the screws (36). Tighten the screws
to the recommended torque.
11) Screw the stop screw (21) by turning it clockwise with an Allen
wrench until it reaches its original position (the same distance with
reference to the end flange surface).
12) Screw the plug (25) into the cylinder end flange.
Carry out a few operations (Sect. 3.3) to check there
are no leakages from the gaskets.