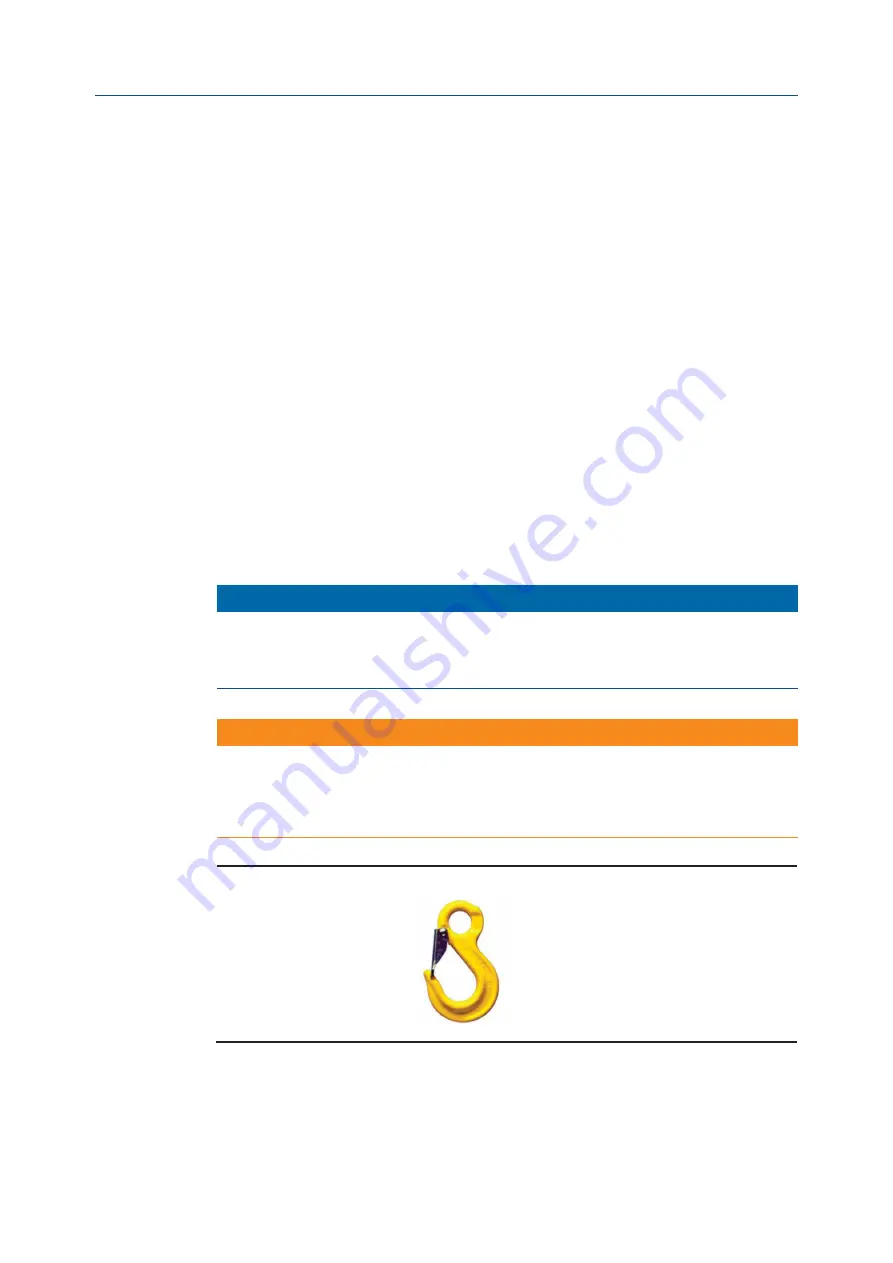
December 2020
Installation, Operation and Maintenance Manual
MAN 606 Rev. 5
Installation
4
Section 2: Installation
Section 2: Installation
2.1
Checks Upon Actuator Receipt
•
Check that the model, the serial number of the actuator and the technical data
reported on the identification plate correspond with those of order confirmation
(Section 1.2).
•
Check that the actuator is equipped with the fittings as provided for by
order confirmation.
•
Check that the actuator was not damaged during transportation: if necessary
renovate the painting according to the specification reported on the
order confirmation.
•
If the actuator is received already assembled with the valve, its settings have
already been made at the factory.
•
If the actuator is delivered separately from the valve, it is necessary to check, and,
if required, to adjust, the settings of the mechanical stops (Section 3.4) and of
micro-switches (if any) (Section 3.5).
2.2
Actuator Handling
NOTICE
The lifting and handling of the actuator must be done by qualified personnel and in
accordance with the laws and regulations in force. Avoid the lifted actuator to be hung
above the personnel.
!
WARNING
The actuator must be lifted by means of a suitable lifting apparatus. The weight of the
actuators is indicated in the technical documentation attached to the equipment itself.
For lifting and moving the actuator, use only hooks fitted with safety latch, like the one,
for example, shown in Figure 3.
Figure 3
Example of Hook with Safety Latch