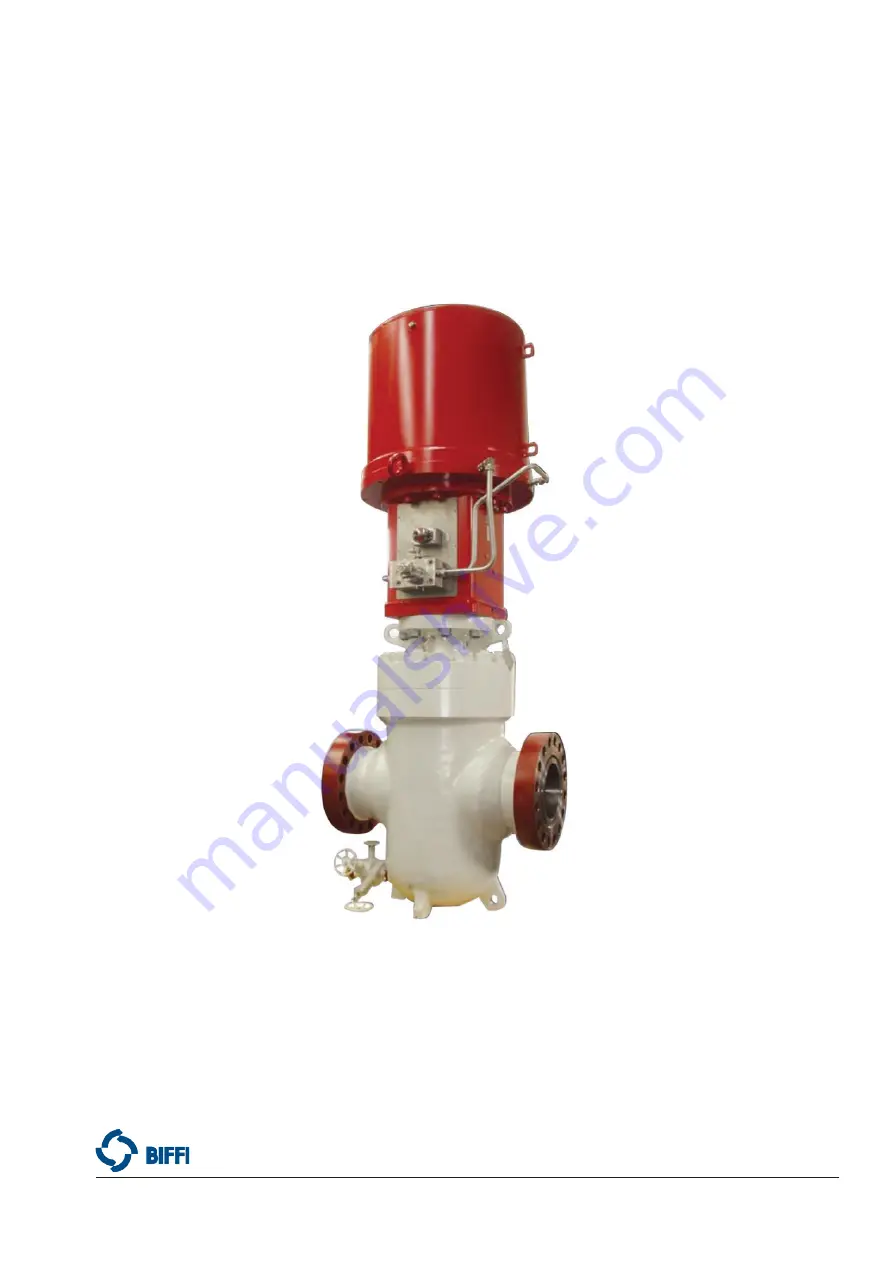
Installation, Operation and Maintenance Manual
MAN 707 Rev. 3
March 2022
Biffi HLAS-C Compact Series
High Pressure Spring-Return Hydraulic Linear Actuator
Copyright © Biffi. The information in this document is subject to change without notice. Updated data sheets can be obtained from our website www.biffi.it or from your nearest Biffi Center:
Biffi Italia s.r.l. - Strada Biffi 165, 29017 Fiorenzuola d'Arda (PC) –
Italy PH:
+39 0523 944 411 – [email protected]