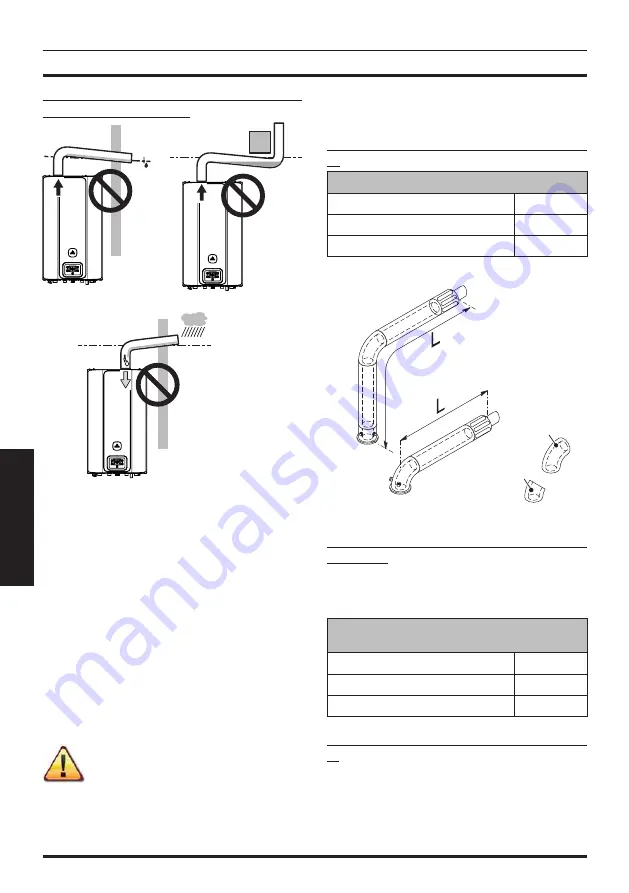
- 40 -
INST
ALL
ATION
INSTALLATION
INCORRECT implementation of twin flue gas
outlet/air suction systems
Figure 5.10
S
A
S
A
= air suction
S
= flue gas outlet
5.9 Flue gas outlet dimensions and
lengths
The flue gas outlet/air suction can be set up in
the following ways:
C
13
C
33
C
43
C
53
C
63
C
83
C
93
B
23P
Consult the sheet provided with the selected kit
which is packaged separately.
The horizontal sections of the flue gas pipes must
have a slope of approx. 1.5 degrees (25 mm per
metre).
The terminal must be higher than
the boiler side opening.
Only the coaxial pipe with the terminal must
be horizontal as the discharge pipe has already
been implemented with the correct slope.
The following kits are available for connection to
the boiler:
Wall-mounted flue gas outlet kit (Figure 5.11
A)
Coaxial duct Ø 60/100 mm (A)
Nominal length
0.915 m
Minimum length
0.5 m
Maximum length
10 m
Figure 5.11
B
A
C
45°
90°
C13
Vertical flue gas outlet kit with 90° elbow (Fig-
ure 5.11 B)
This kit is used to raise the outlet axis of the boiler
by 635 mm.
The terminal must always discharge horizontally.
Coaxial duct Ø 60/100 with
90° elbow (B)
Nominal length
1.55 m
Minimum length
0.5 m
Maximum length
10 m
Supplementary 45° or 90° elbows (Figure 5.11
C)
Coaxial elbows Ø 60/100 mm.
When these elbows are used in the duct, they re-
duce the maximum length of the flue gas duct
by: