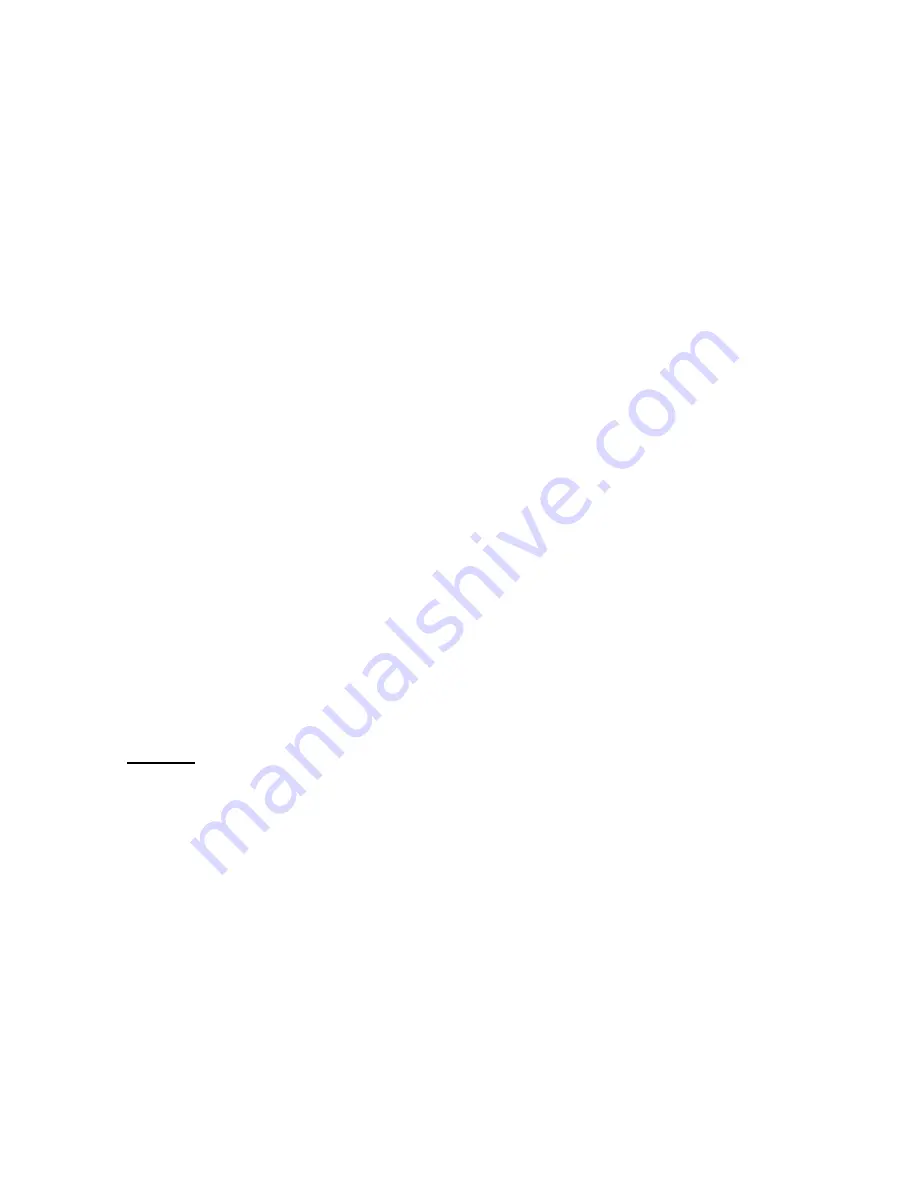
2.6
BALANCED FLUE IN HORIZONTAL CONFIGURATION (CONTINUED)
2.6.2
Mark the position of the centre of the flue on the inner wall. (See Fig.
11 on previous page for position).
2.6.3
Cut hole for outer flue pipe. There are two possible methods to achieve
this, either core drill or via hammer and chisel.
2.6.4
To core drill, proceed as follows :-
2.6.5
Drill a pilot hole through the wall, in position as specified in Fig 11 on
previous page.
2.6.6
Using a 6” core drill, drill the flue hole.
2.6.7
To Hammer and chisel, proceed as follows :-
2.6.8
Mark the position of the centre of the flue pipe as specified in Fig 11.
2.6.9
Mark the position of the hole around this point.
2.6.10
Chisel out the area as marked on the wall.
2.6.11
We then recommend that a cardboard cylinder is placed around the flue
pipe and inserted in the chiselled out hole whilst making good. A wall
plate is provided on the flue duct to seal the terminal around the
flue pipe opening and make good.
Please ensure all joints are taped with suitable high temperature tape when
assembling the flue pipe sections together.
NOTE :- If the appliance is to be installed into a building under
construction, it is recommended that a non-corrosive metal tube of 6”
diameter be inserted into the position of the hole as specified on page 13.
14