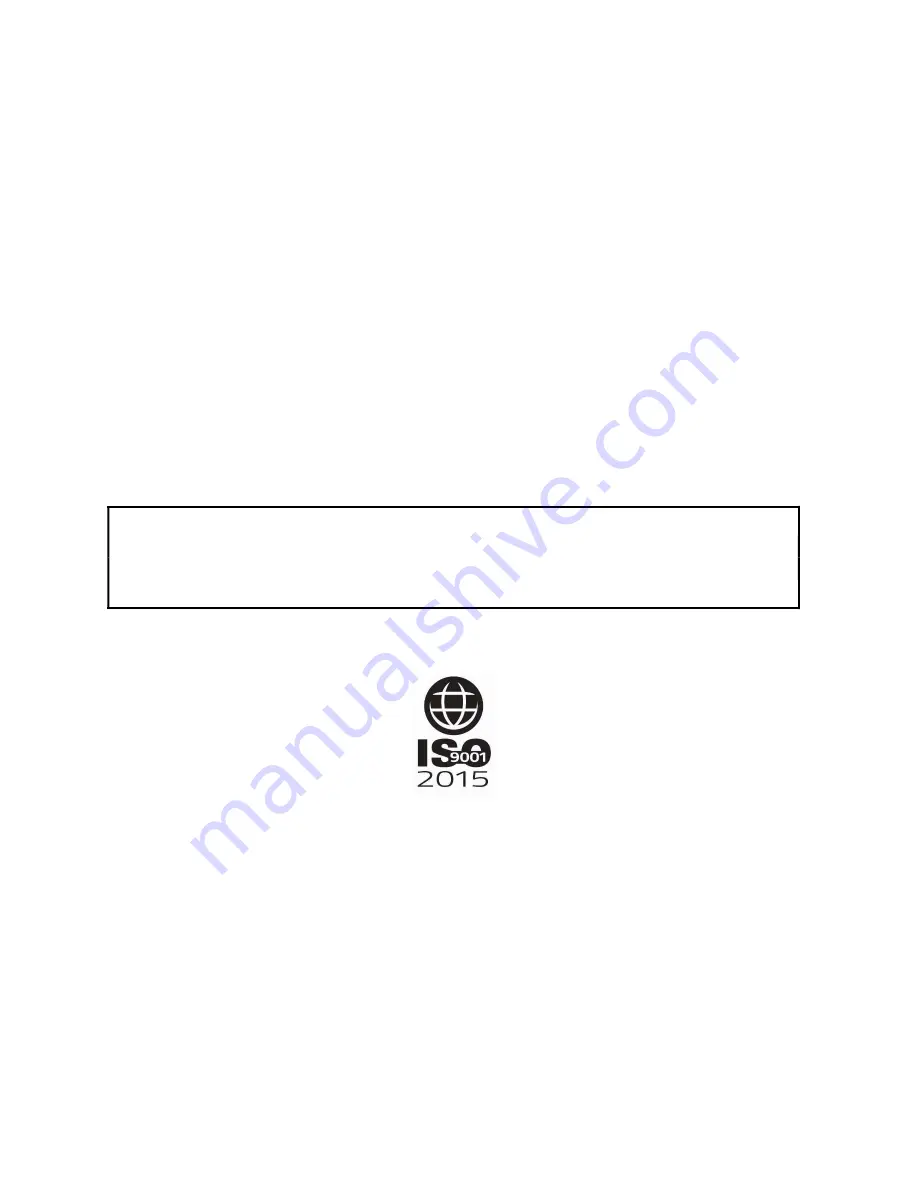
Information in this document is subject to change without notice.
No part of this document may be reproduced or transmitted in any form or any means, electronic or
mechanical, for any purpose, without the express written permission of Bettcher Industries Inc.
Written permission to reproduce in whole or part is herewith granted to the legal owners of the
Bettcher
®
AutoEdge with which these Operating Instructions have been supplied.
Operating Instructions in other languages are available on request. Additional copies of Operating
Instructions are available by calling or writing the local Representative or by contacting:
BETTCHER INDUSTRIES, INC.
P.O. Box 336
Vermilion, Ohio 44089-0336
U.S.A.
Telephone : 440/965-4422
(In The U.S.A.) : 800/321-8763
Fax : 440/328-4535
The Information Provided In These Operating Instructions Is Important To Your
Health, Comfort And Safety.
For Safe And Proper Operation, Read This Entire Manual Before Using This
Equipment.
Copyright
2018 by Bettcher Industries, Inc.
All Rights Reserved
Original Instructions
Page i
COMPANY
CONFIDENTIAL