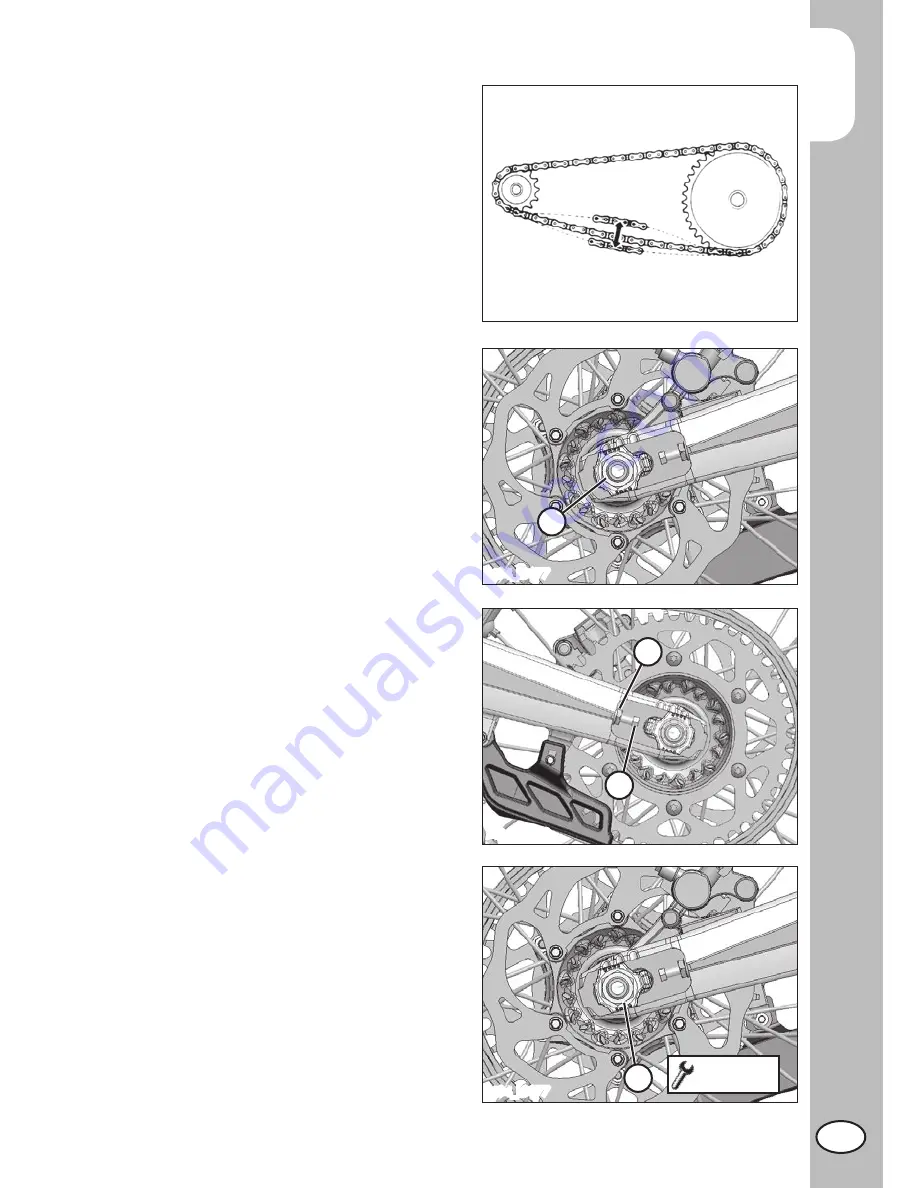
4
C
HEC
KS AND MAINTENAN
CE
61
USA
CHECK AND ADJUST
TIGHTENING CHAIN
Position the drive on a flat base ensuring
stability.
If the chain play exceeds 30÷35 mm ten-
sion the chain.
%
Loosen the pin
1
.
%
Loosen counternuts
A
on either side of
the fork.
%
Turn adjusting screws
B
on either side until
the desired chain tension is obtained.
%
Tighten counternuts
A
on either side of
the fork.
30÷35 mm
1
M04_L0077
A
B
M04_L0078
1
130Nm
M04_L0077
%
Tighten the pin
1
to the torque indicated.
Summary of Contents for RR-S 350 EFI 2020
Page 1: ...4 STROKE 2020 OWNERS MANUAL W W W B E T A U S A C O M...
Page 10: ...1 GENERAL INFORMATION 9 USA...
Page 17: ...16 USA...
Page 29: ...28 USA...
Page 39: ...38 USA...