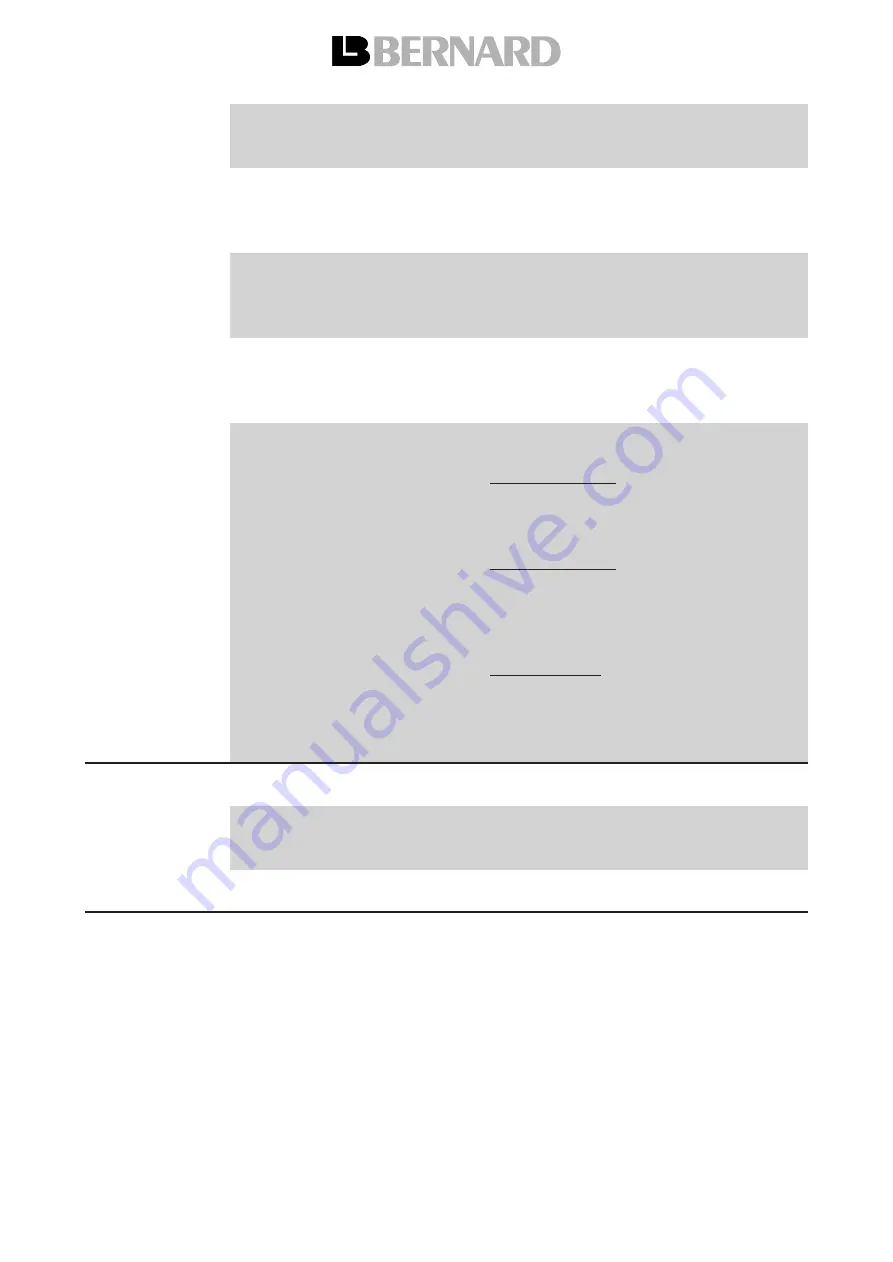
21
CORRECTIVE ACTION
Set the local/remote selector switch to
remote to use the positioner (even when
the positioner is set to manual).
Check that the Actuator receives no
Auto/on-off control command.
Disconnect this remote control (terminal
37) as required for confirmation.
Check the positioner board-Integral board
connection.
Turn the Actuator potentiometer by a
quarter-turn and repeat adjustments in
accordance with commissioning
instructions.
Check input signal configuration on the
positioner board:
4-20 mA signal:
Switch 4 set to A
Switch 9 set to A
Switch 10 set to A
0-20 mA signal:
Switch 4 set to B
Switch 8 set to B
Switch 9 set to A
Switch 10 set to A
0-10 V signal:
Switch 4 set to B
Switch 8 set to B
Switch 9 set to B
Switch 10 set to B
Check setting of Auto - 0% - 100% switch
on the positioner board.
Check the reference signal using a
milliammeter connected in series
(terminal 70).
Check that the plus (+) of the signal is
present at terminal 70
PROBLEM
The actuator
operates in
local
open/close
control mode,
not in
positioner
mode
The Actuator
operates in
positioner
mode in local
mode, not in
remote mode
CAUSE
Local/remote selector
switch set to local or to off
An auto/on-off control order
is present and inhibits the
positioner.
The connector connecting
the positioner board to the
"I" board is
disconnected.
The actuator repeater
potentiometer is incorrectly
set
Input signal incorrect
The Auto - 0% - 100%
switch is not set to Auto
Signal defective
Signal polarity