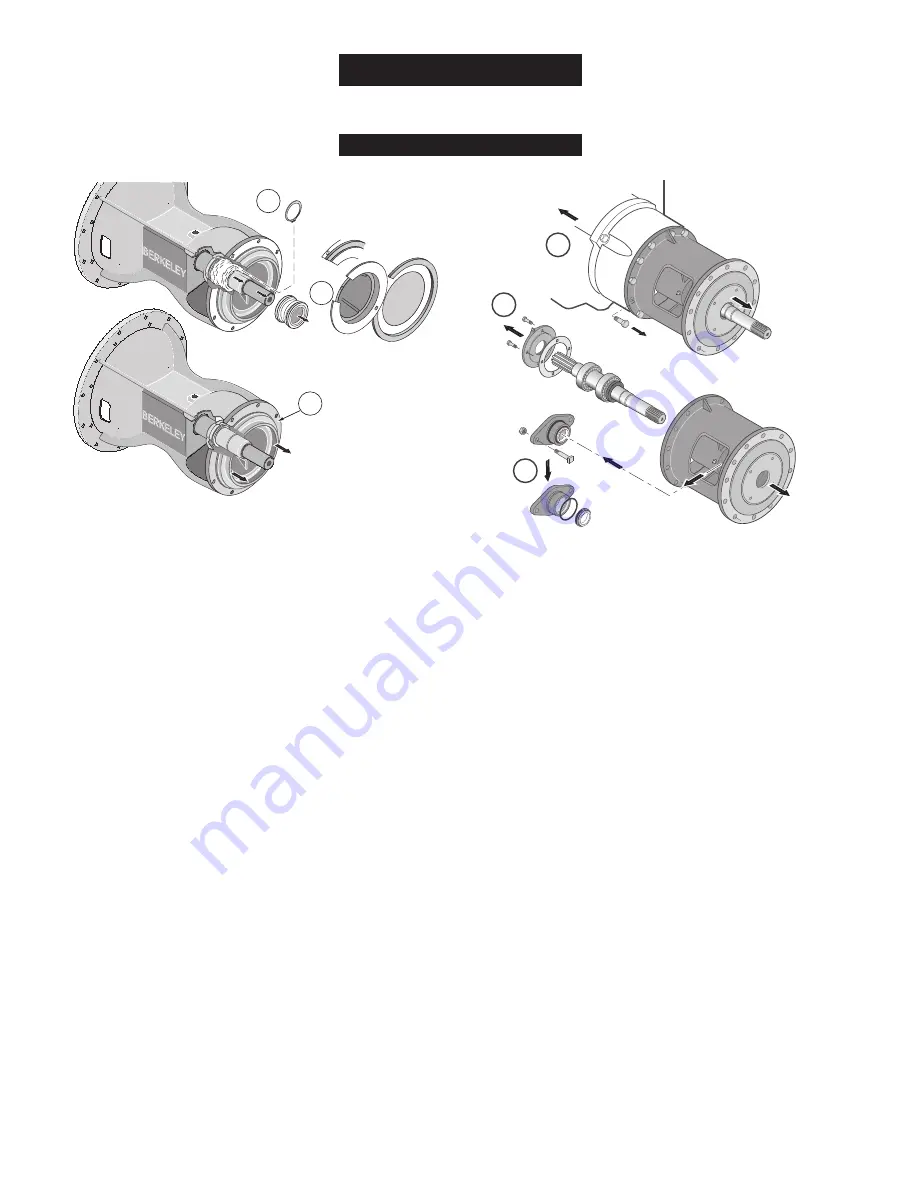
3.
If your pump has a bolted in balance ring, remove it; if it
has a pressed in balance ring, leave it in place unless
there isn’t room to get the seal out past it. If it doesn’t
have a balance ring, go to Step 4.
•
Check the clearance between the balance ring and
the impeller hub. If it is more than .020” on a side,
replace the balance ring.
4.
Remove the seal retaining ring and pull the rotating part
of the seal off the shaft.
Model B4EYQBHS
and similar pumps: See the special
section on this page. Others: go to Step 5.
5.
Z Series:
Pull the seal plate out until it clears the shaft,
bringing the stationary part of the seal out with it. Tap the
seal out of the seal plate and clean the seal cavity.
Other Pumps: Pull the stationary part of the seal out of
the cavity and clean the cavity.
6.
Install the new stationary seal in the seal cavity.
•
Apply a small amount of mineral oil to the O-Ring or
cup seat of the stationary seal.
•
Use the cardboard washer (supplied) and a piece of
pipe as a press; press the stationary seal into place.
•
Do not damage the seal face!
7.
Reinstall the seal plate (if used) now.
•
Cover all shaft threads with tape to protect the seal
during installation.
•
Apply a small amount of mineral oil to the inside
diameter of the rubber ring in the rotating seal and to
the outside of the shaft sleeve.
•
Slide the seal plate over the shaft now, taking care to
avoid damage to the stationary part of the shaft seal
as it goes over the shaft shoulder.
8.
After lubricating the rotating part of the seal, slide it onto
the shaft and sleeve until it seats against the stationary
(ceramic) part.
9.
Compress the seal spring on the shaft sleeve and
reinstall the seal retaining ring (if used).
10. Reinstall the balance ring (if used).
11. Slide or thread the impeller onto the shaft until it seats
solidly against the shaft shoulder, then install a new
impeller screw with its associated hardware.
12. Replace the volute. Use new gasket(s) and O-Ring(s).
B4EYQBHS and similar pumps (See Picture Above):
After STEP 4, you will need to:
A.
Remove the bracket from the engine.
B.
Remove the outer bearing cap and slide the shaft
assembly back out of the bracket.
C.
Remove the seal retainer and tap out the stationary seal.
D.
Clean the seal retainer and shaft (don’t scratch the
shaft!).
E.
Apply a small amount of mineral oil to the O-Ring or cup
seat of the stationary seal, to the inside diameter of the
rubber ring in the rotating seal, and to the outside of the
shaft sleeve.
F.
Use the cardboard washer (supplied) and a piece of pipe
to press the stationary seal into place.
G.
Inspect the oil seal and replace it if necessary.
H.
Repack the bearings and reinstall the shaft in the bracket.
NOTE:
When the end of the shaft comes through the
front bearing bore in the bracket, slip the slinger and seal
retainer over the end of the shaft. BE SURE you don’t
damage the seal face on the shaft shoulder!
J.
Reinstall the outer bearing cap with a new gasket and
proceed to STEP 7 (“Reinstall the shaft sleeve....”)
F00636
Page 19
Seal/Impeller Replacement
Maintenance
1
3
2
Remove seal
plate
6056 0609
A
B
C
B4EY Series
Seal Chan
g
e
Se
q
uence
Summary of Contents for S.A.E.
Page 28: ......