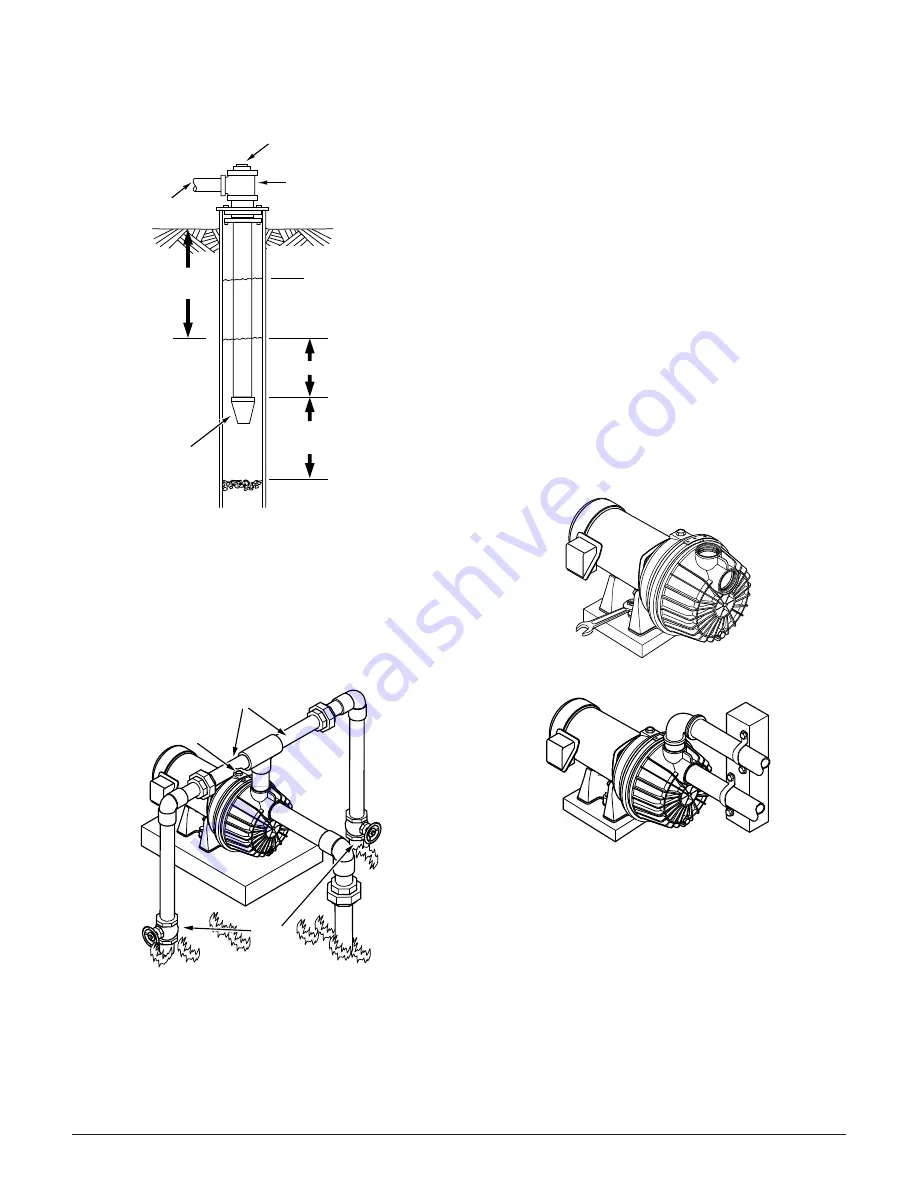
4.
When proper depth is reached, install sanitary well seal
over pipe and in well casing. Tighten bolts to seal casing.
5.
When using foot valve, a priming tee and plug are rec-
ommended (See Figure 1).
Driven Point Installation
1.
Connect suction pipe to drive point (See Figure 2). Keep
horizontal pipe run as short as possible. Use Teflon tape
on male pipe threads. Multiple well points may be neces-
sary to provide sufficient water to pump.
2.
Install check valve in horizontal pipe. Flow arrow on
check valve must point toward pump.
Horizontal Piping From Well To Pump
1.
Pump performance will be decreased if less than 1-1/2”
pipe is used as suction pipe.
2.
To aid priming on well point installations, install line
check valve. Be sure check valve flow arrow points
toward pump.
Discharge Pipe Sizes
Discharge pipe size should be increased to reduce pressure
losses caused by friction on long pipe runs.
• Up to 100' (30.5 m) run: Same size as pump discharge
port.
• 100' - 300' (30.5 - 91.4 m) run: Increase one pipe size.
• 300' - 600' (91.4 - 182.9 m) run: Increase two pipe sizes.
Lawn Sprinkler Application
This pump is designed for lawn sprinkling. Delivers plenty of
water at full sprinkler pressure. Pumps from pond, cistern, or
well points.
Pump discharge can be divided to supply 4 or more sprinkler
systems.
Do not use in booster pump applications.
Pump/Piping Installation
If turning pump on and off by pressure, a pressure switch
and tank are required. For proper installation and operation
instructions, call Customer Service.
Use rigid pipe. Do not use hose or plastic tubing. See “Well
Pipe Installation” for more information.
NOTE:
Use only Teflon tape or Teflon based joint compounds
for making all threaded connections to the pump itself. Make
sure that all pipe joints in the suction pipe are air tight as well
as water tight.
If the suction pipe can suck air, the pump will
not be able to pull water from the well.
1.
Bolt pump to solid, level foundation (See Figure 3).
2.
Support all piping connected to pump (See Figure 4).
3.
Wrap 11⁄2 to 2 layers of Teflon tape clockwise (as you
face end of pipe) on all male threads being attached to
pump.
4.
Tighten joints hand tight plus 11⁄2 turns.
Do not over-
tighten.
5.
Replacing the priming plug with a pressure gauge (pur-
chased separately) will aid in sizing zones, troubleshoot-
ing, and following the pump performance chart.
NOTE:
Install pump as close to well head as possible. Long
piping runs and many fittings create friction and reduce flow.
NOTE:
For long horizontal pipe runs, install a priming tee
between check valve and well head (See Figure 1). For dri-
ven point installations, install check valve. Be sure that check
valve flow arrow points
toward
pump.
3
Suction
pipe
Foot
Valve
Priming plug
Priming tee
Drawdown water
level (pump on)
10-20' (3-6 m)
20' (6 m)
max.
At least 5 feet
(1.5 m)
Standing water
level (pump off)
Figure 1 – Cased/Dug Well
L17
6-35P
Gate
valve
To
service
Priming
plug
Figure 2 – Driven Point
L17
6-35P
Figure 3 – Bolt Pump to Foundation
L17
6-35P
Figure 4 – Support All Piping Connected to Pump