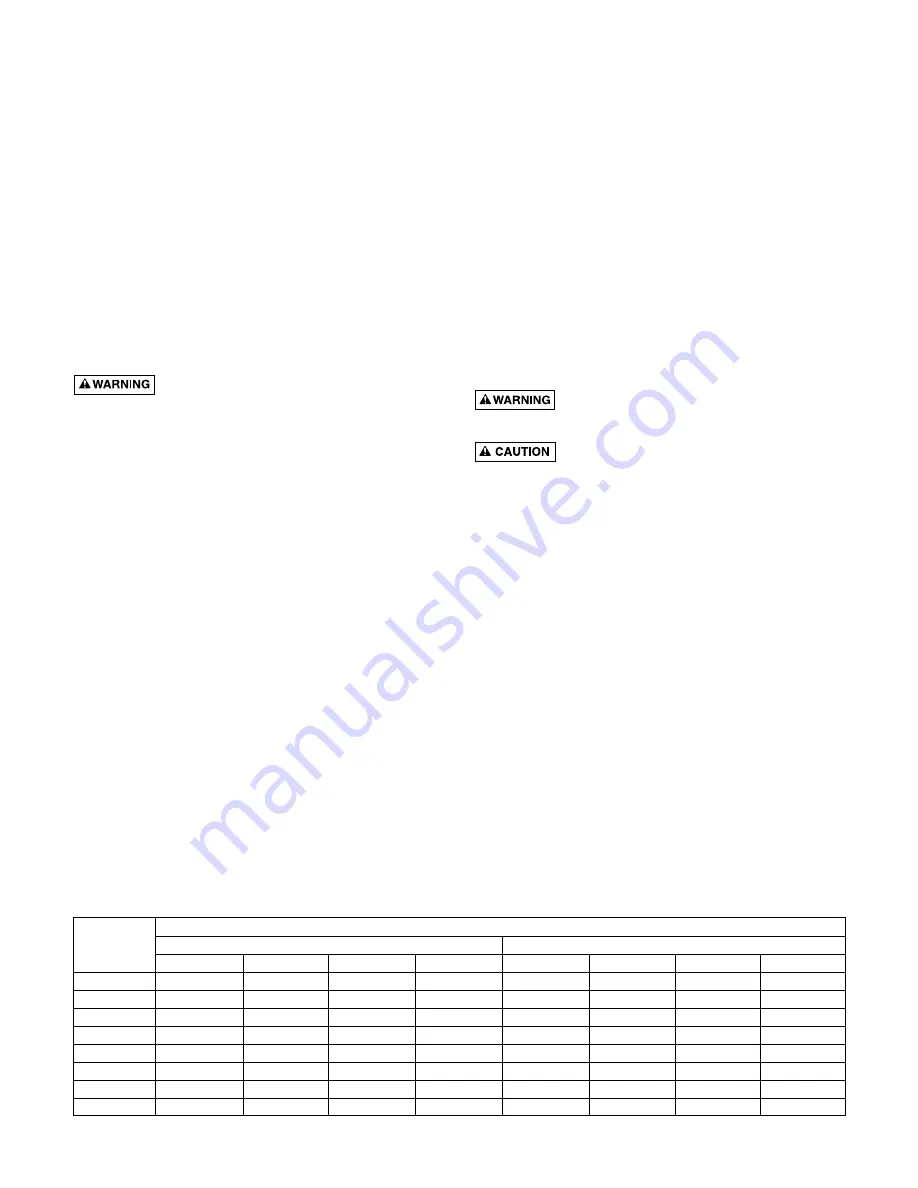
SPECIFICATIONS
Horsepower (10PDH11VT) . . . . . . . . . . . . . . . . . . . . . . . 1
(15PDH11VT) . . . . . . . . . . . . . . . . . . . . 1-1/2
Volts @ 60 Hz. . . . . . . . . . . . . . . . . . . . . . . . . . . . 115/230
Phase . . . . . . . . . . . . . . . . . . . . . . . . . . . . . . . . . . . . . . . 1
Pump Body . . . . . . . . . Fiberglass reinforced thermoplastic
Impeller . . . . . . . . . . . . . . . . . . . . . . . Engineered polymer
Seal . . . . . . . . . . . . . . . . . . . . . . . . . . . . . . . . . . . . Viton*
Diffuser . . . . . . . . . . . . . . . . . . . . . . . . . . . . Polypropylene
Height . . . . . . . . . . . . . . . . . . . . . . . . . . . . . . . . 11-13/16”
Width . . . . . . . . . . . . . . . . . . . . . . . . . . . . . . . . . . .6-9/16”
Length (10PDH11VT) . . . . . . . . . . . . . . . . . . . . . . 18-5/8”
(15PDH11VT) . . . . . . . . . . . . . . . . . . . . . . 19-3/4”
Port Size - Inlet . . . . . . . . . . . . . . . . . . . . . . . . . . . . 1-1/2”
Port Size - Outlet . . . . . . . . . . . . . . . . . . . . . . . . . . . 1-1/2”
* Seal has ceramic seat, carbon head, and stainless steel
spring.
INSTALLATION
Risk of fire and explosion.
Do not use this
pump to pump flammable or explosive fluids such as gaso-
line, fuel oil, kerosene, etc. Do not use in flammable or
explosive atmospheres. Pump should only be used with liq-
uids compatible with pump component materials. Failure to
follow this warning can result in personal injury and/or prop-
erty damage.
Make certain that the power source conforms to the require-
ments of your equipment.
Provide adequate protection and guarding around moving
parts.
Disconnect power before servicing.
Release all pressure within the system before servicing any
component.
Drain all liquids from the system before servicing.
Secure the discharge line before starting the pump. An unse-
cured discharge line will whip, possibly causing personal
injury and/or property damage.
Check hoses for weak or worn condition before each use,
making certain that all connections are secure.
Provide a means of pressure relief for pumps whose dis-
charge line can be shut or obstructed.
Personal Safety
1.
Wear safety glasses at all times when working with
pumps.
2.
Wear a face shield and proper protective apparel when
pumping hazardous chemicals.
Before You Install Your Pump
NOTE:
Well must not be more than 20' (6.1m) depth to
water.
1.
Long runs and many fittings increase friction and reduce
flow. Locate pump as close to well as possible; use as
few elbows and fittings as possible. Be sure suction line
is straight and angles toward pump.
2.
Be sure well and pipe are clear of sand, dirt and scale.
Foreign matter will plug pump and void warranty. Use
new pipe for best results.
3.
Protect pump and all piping from freezing. Freezing will
split pipe, damage pump and void warranty. Check locally
for frost protection requirements (usually pipe must be 12"
(30.5cm) below frost line and pump must be insulated).
4.
Be sure all pipes and foot valve are clean and in good
shape.
5.
Assure there are no air pockets in suction pipe.
6.
Assure there are no leaks in suction pipe. Use Teflon
tape or Plasto-Joint Stik to seal pipe joints.
7.
Unions installed near pump and well will aid in servicing.
Leave enough space to turn wrenches.
Pump body may explode if used as boost-
er pump. DO NOT use in booster application.
Motor normally operates at high temperature
and will be too hot to touch. It is protected from heat damage
during operation by an automatic internal cutoff switch.
Before handling pump or motor, stop motor and allow it to
cool for 20 minutes.
Well Pipe Installation
NOTE:
Use installation method below which matches your
well type.
Cased Well/Dug Well Installation
1.
Inspect foot valve to be sure it works freely. Inspect
strainer to be sure it is clean and secure.
2.
Connect foot valve and strainer to first length of suction
pipe and lower pipe into well. Add sections of pipe as
needed, using Teflon tape on male threads (use 11⁄2”
pipe for suction pipe). Be sure all suction pipe is
leakproof or pump will lose prime and fail to pump. Install
foot valve 10 to 20 ft. (3 to 6 m) below lowest level to
which water will drop while pump is operating (pumping
water level). Your well driller can furnish this information.
3.
To prevent sand and sediment from entering pumping
system, foot valve/strainer should be at least 5 ft. (1.5 m)
above bottom of well.
2
Discharge
Gallons Per Minute at Discharge Pressure (PSI)
Pressure
10PDH11VT
15PDH11VT
PSI
5’
10’
15’
20’
5’
10’
15’
20’
10
55
49
48
45
67
61
56
46
15
51
46
45
44
66
58
55
45
20
45
42
39
37
61
56
54
44
25
38
35
32
29
55
52
51
43
30
31
28
24
20
48
45
44
37
35
23
19
16
11
39
37
34
28
40
17
13
8
–
33
27
20
11
45
–
–
–
–
18
14
8
–
PERFORMANCE