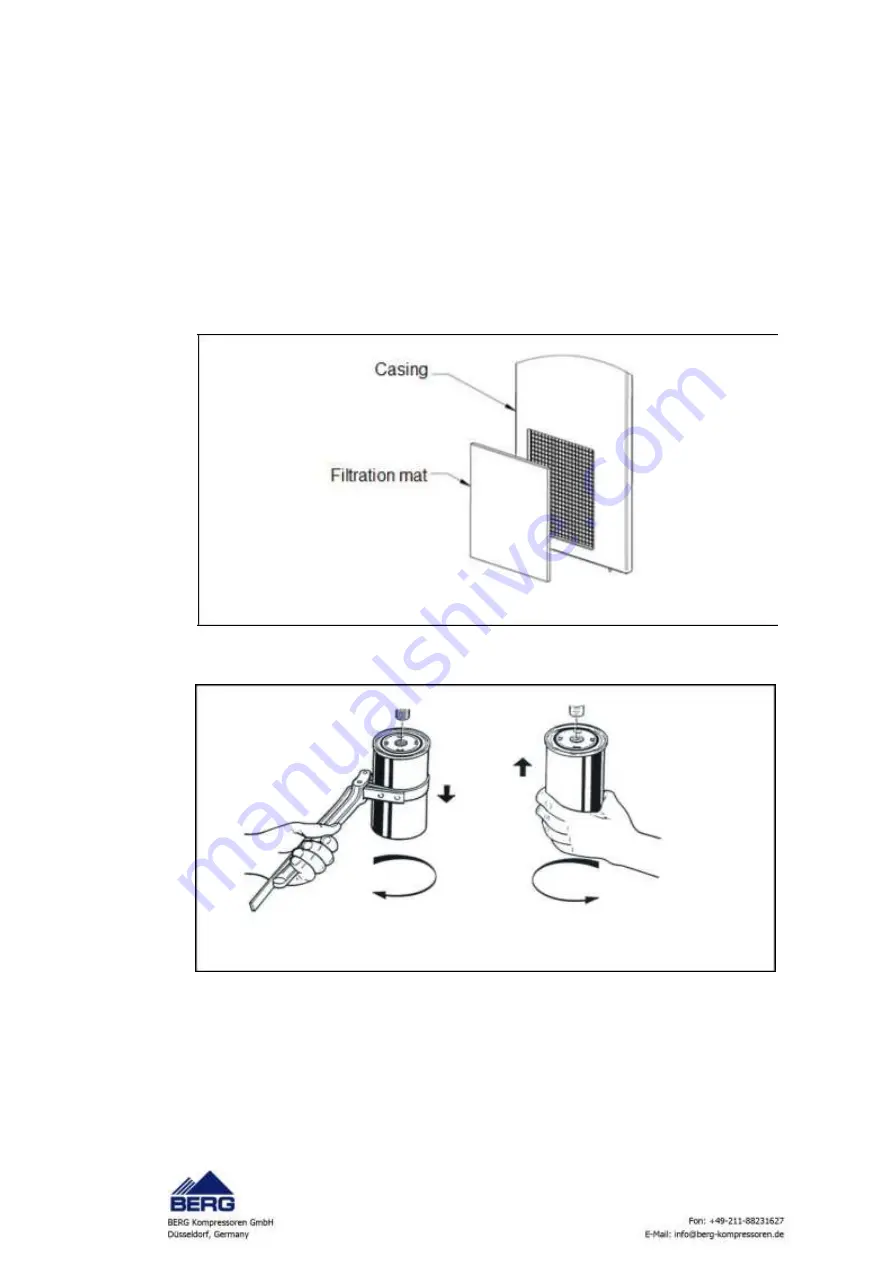
26
7.3.2 Cleaning or replacing the filter mats.
Filter mat is placed at the inlet into the housing. If the filter mat get dirty, cooling of the
compressor may be insufficient.
Maintenance operations:
-
Carefully, without tools, remove the filter mat from the housing.
-
Thoroughly vacuum or flick the mat. In case of heavy dirtiness, the mat can be washed
in water with detergent.
-
If it’s impossi
ble to clean the mat or the mat is damaged, it should be completely
replaced.
-
Carefully placed the filter mat in the housing.
Filtration mat exchange
7.3.3. Oil filter
Change the oil filter every 8000 hours or once a year.
screwing out
screwing in
Oil filter - maintenance
Maintenance procedure:
-
Stop the compressor and close the pressure conduit valve. Reduce the overpressure in the screw
assembly body and oil system to reach the atmospheric pressure (see the oil pressure manometer
/ microprocessor controller).
-
Safeguard the compressor from restarting by an unauthorized person, e.g. by cutting power supply
off.
-
It is advised to use a special spanner to replace the filter. Caution
–
hot oil!