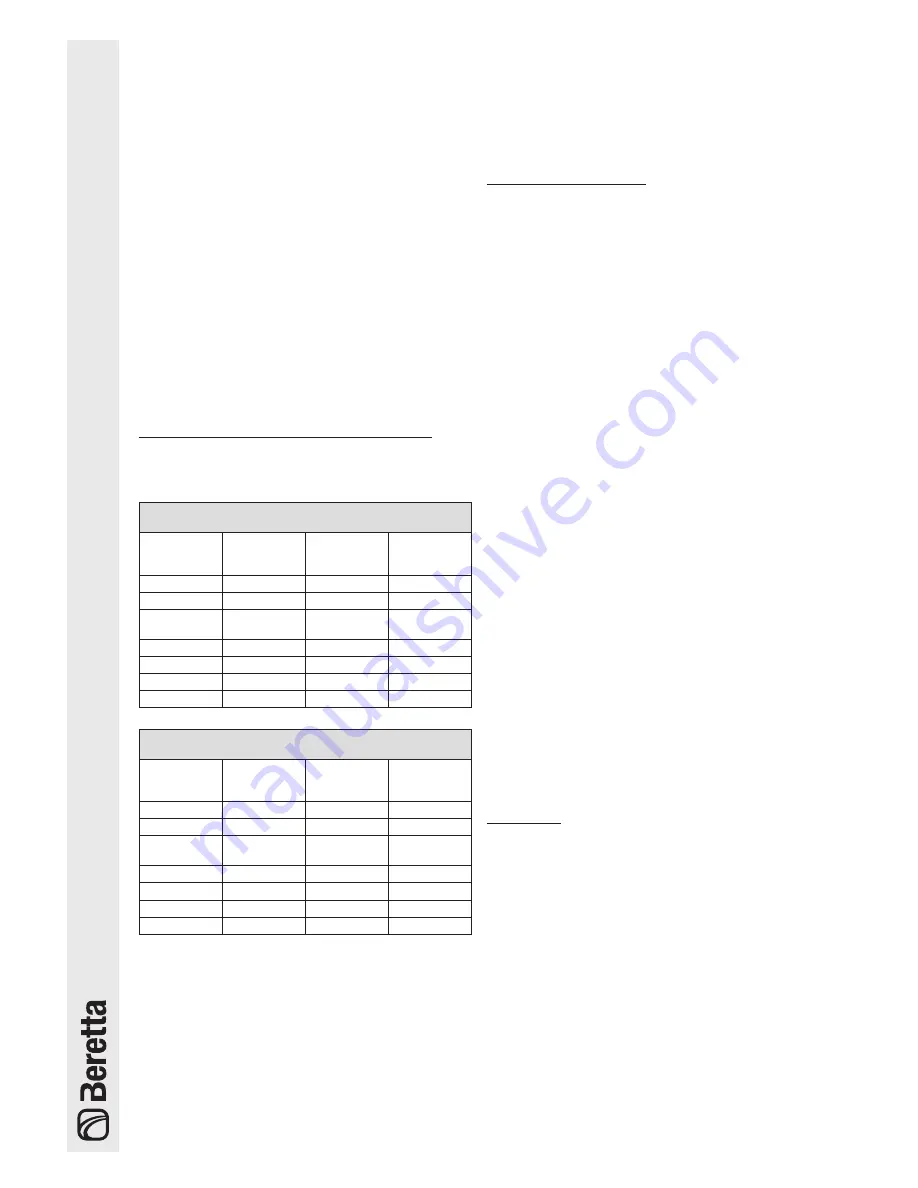
56
4 WATER IN CENTRAL HEATING
SYSTEMS
INTRODUCTION
Water used in central heating systems MUST be suitably
treated to ensure the correct functioning of those systems
and to guarantee an extended working life for boilers and
all other system components. This applies not only to exist-
ing systems but to newly installed systems too.
Sludge, lime-scale and pollutants present in the water can
cause permanent damage to the heating unit, also within
a short time and regardless of the quality standards of the
materials used.
Contact the Technical Assistance Centre for any further in-
formation on type and use of additives.
b
Always conform to the standards and legislation ap-
plicable in the country of installation.
WATER IN CENTRAL HEATING SYSTEMS.
INSTRUCTIONS FOR THE DESIGN, INSTALLATION AND
MANAGEMENT OF CENTRAL HEATING SYSTEMS.
1. Chemical and physical characteristics of water
The chemical and physical characteristics of water used in
central heating systems must conform to the requirements
of EN 14868 standard and to the following tables:
STEEL BOILERS
with furnace power < 150 kW
Initial filling
water
Regular ser-
vice water
(*)
ph
6-8
7,5-9,5
Hardness
°fH
< 10°
< 10°
Electrical
conductivity
μs/cm
< 150
Chlorides
mg/l
< 20
Sulphides
mg/l
< 20
Nitrides
mg/l
< 20
Iron
mg/l
< 0,5
STEEL BOILERS
with furnace power > 150 kW
Initial filling
water
Regular ser-
vice water
(*)
ph
6-8
7,5-9,5
Hardness
°fH
< 5°
< 5°
Electrical
conductivity
μs/cm
< 100
Chlorides
mg/l
< 10
Sulphides
mg/l
< 10
Nitrides
mg/l
< 10
Iron
mg/l
< 0,5
(*) values for water in system after 8 weeks of functioning
General note on water used to top up systems:
- If softened water is used to top up a system, 8 weeks
of functioning after topping up, verify that the water in
the system respects the above limits, in particular for
electrical conductivity
- This check is not necessary if demineralised water is
used to top up the system.
2. Central heating systems
b
Do not use automatic filling devices to add water to
central heating systems. Use a manual device in-
stead and record top-ups in the system service book.
b
If there are more than one boiler, they must all be put
into service either contemporarily or with a very low
rotation time during the initial period of service, so as
to evenly distribute the limited quantity of initial lime-
scale.
b
A flushing cycle must be programmed after the plant
has been installed to flush out any installation debris.
b
Water used to fill a system for the first time and water
used to top it up must always be filtered (using syn-
thetic or metal mesh filters with a filtration rating of no
less than 50 microns) to prevent sludge from forming
and triggering deposit corrosion.
b
The heating system must be flushed out and cleaned
with good workmanship before filling up the existing
systems. The boiler may not be filled until after the
heating system has been flushed out.
2.1 New central heating systems
The system must be filled up slowly the first time; once it is
filled and the air expelled it should never need to be topped
up again.
Systems should also be operated at maximum working
temperature the first time they are started up, in order to
facilitate de-aeration. (Gas is not released from the water at
low temperatures).
2.2 Reconditioning old central heating systems
If a boiler has to be replaced, do not refill the entire cen-
tral heating circuit if the quality of water in it conforms to
requirements. If the quality of water fails to conform to re-
quirements, either recondition the old water or separate the
water circuits (water in the boiler circuit must conform to
requirements).
3. Corrosion
3.1 Deposit corrosion
Under-deposit corrosion is an electrochemical process,
due to the presence of sand, rust, etc., inside the mass
of water. These solid substances generally deposit on the
bottom of the boiler (sludge), on tube and pipe heads or in
the gaps between pipes and tubes.
Micro-corrosion phenomena may be triggered off owing
to the difference in electrochemical potential coming to be
created between the material in contact with the impurity
and the surrounding one.