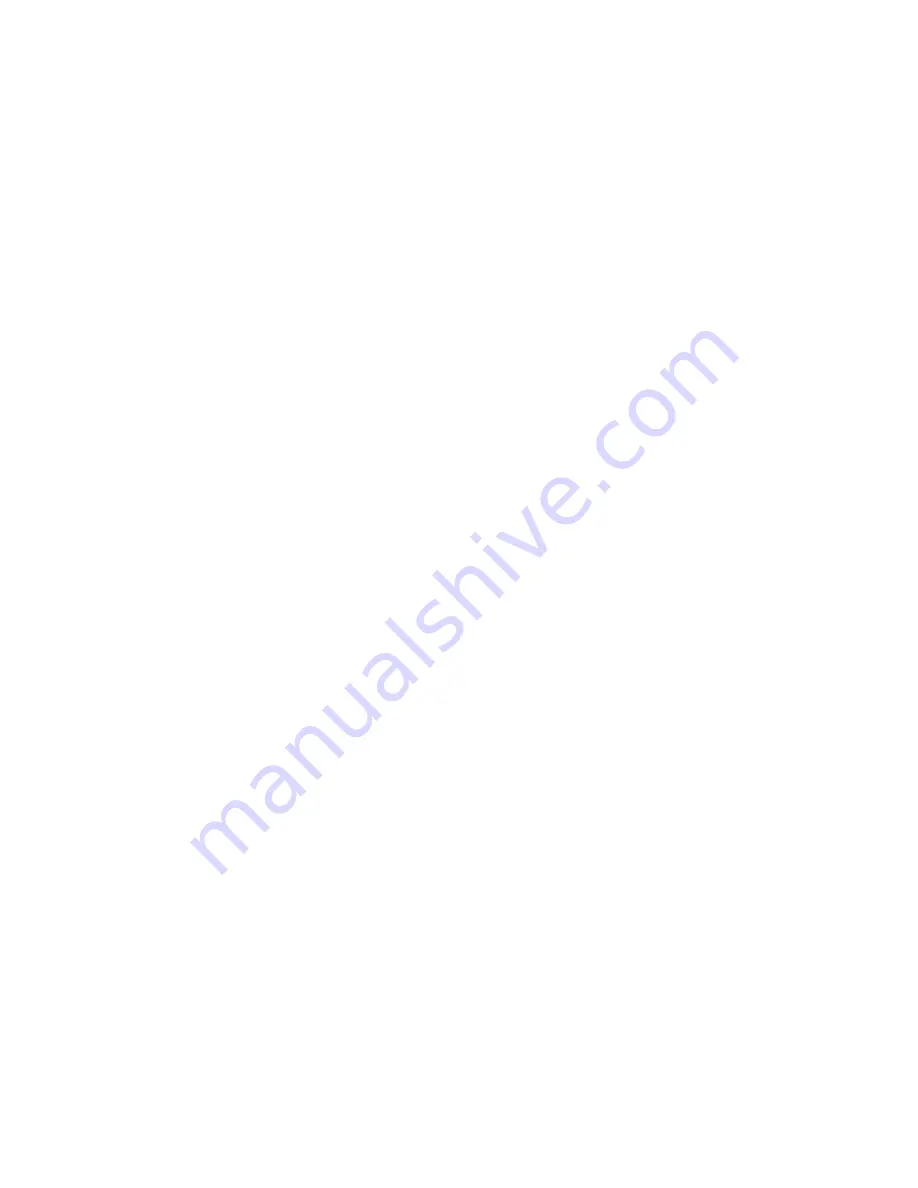
GUH RANGE PROPANE GAS FIRED UNIT HEATERS
Page 13 of 41
2.5 Flue Installation
.
An integral flue spigot is fitted to all GUH Air Heaters thereby allowing the flue to connect directly to
the heater.
The design of the flue must ensure that it can be disconnected to allow for cleaning and servicing.
Further more all of the flue section joints must face upwards and the seal between the sections achieved
through the use of approved caulking string and / or grout.
Warning
It is essential that the products of combustion are flued to the outside of the building.
Each heater must have its own separate flue, with a flue diameter of not less than is detailed in section 7.2
within this manual.
The flue assembly must comply with all the relevant regulations regarding height and materials, and must
terminate with an approved flue terminal.
All GUH Air Heaters are equipped with a built in down draught diverter which prevents the recirculation
of combustion products, consequently an external draught diverter, barometric damper, or anti spillage
system must not be installed. Such devices are unnecessary on the GUH range of heaters.
Alterations to the built in down draught diverter must not be carried out, and it is necessary to provide a
minimum unobstructed clearance in front of the heater of 2Metres to ensure that the down draught
diverter will function correctly and also provide access for servicing.
In order to provide adequate natural draught, the minimum vertical length of flue must not be less than
2Metres.
The flue should rise vertically, and the number of bends should be kept to a minimum.
The temperature of the combustion products can be as high as 260° C and therefore tend to rise naturally
within the flue. Unnecessary bends and restrictions should therefore be avoided.
Provision for the disconnection of the flue for servicing and inspection purposes must also be made, and
where appropriate bends should be fitted with access covers, again to allow for cleaning and inspection.
The position of the flue and its terminal should be such that it does not impair the combustion process. It
should terminate in an exposed position so as to allow the free escape of flue gases without risk of their
re-entering the building through windows, ventilation ports etc.
The following illustrations of different flue configurations are included for guidance purposes (see
figures 2-12 )
If the flue does not have access to an existing chimney then it should be extended through the roof or
wall to a height of at least 1M above that of any object within 3.5M of the terminal.
The materials from which the flue is constructed must be non-combustible, resistant to internal and
external corrosion, and be capable of withstanding the stresses and loadings associated with normal use.
When designing the flue system the prevention of the formation and entrapment of condensation must be
a key consideration.
Twin wall or insulated systems are recommended, as they tend to inhibit the formation of condensates.
Where condensation is unavoidable traps should be included to encourage the condensates to flow freely
to a point from which they may be released, preferably into a gully.
The condensate pipe from the flue to the disposal point must be made from corrosion resistant pipe of not
less than 25mm internal diameter.
If the flue passes through a wall, ceiling, or roof made from combustible material then it has to be sleeved
so as to provide a minimum of a 25mm void between the exterior of the flue and the internal wall of the
sleeve.
The maximum permitted temperature of any adjacent combustible material is 65
o
C.
Summary of Contents for GUH100
Page 12: ...GUH RANGE PROPANE GAS FIRED UNIT HEATERS Page 12 of 41...
Page 15: ...GUH RANGE PROPANE GAS FIRED UNIT HEATERS Page 15 of 41...
Page 16: ...GUH RANGE PROPANE GAS FIRED UNIT HEATERS Page 16 of 41...
Page 17: ...GUH RANGE PROPANE GAS FIRED UNIT HEATERS Page 17 of 41...
Page 21: ...GUH RANGE PROPANE GAS FIRED UNIT HEATERS Page 21 of 41...
Page 22: ...GUH RANGE PROPANE GAS FIRED UNIT HEATERS Page 22 of 41...
Page 31: ...GUH RANGE PROPANE GAS FIRED UNIT HEATERS Page 31 of 41 6 0 Wiring Diagrams...
Page 32: ...GUH RANGE PROPANE GAS FIRED UNIT HEATERS Page 32 of 41...
Page 33: ...GUH RANGE PROPANE GAS FIRED UNIT HEATERS Page 33 of 41...
Page 34: ...GUH RANGE PROPANE GAS FIRED UNIT HEATERS Page 34 of 41...
Page 35: ...GUH RANGE PROPANE GAS FIRED UNIT HEATERS Page 35 of 41...