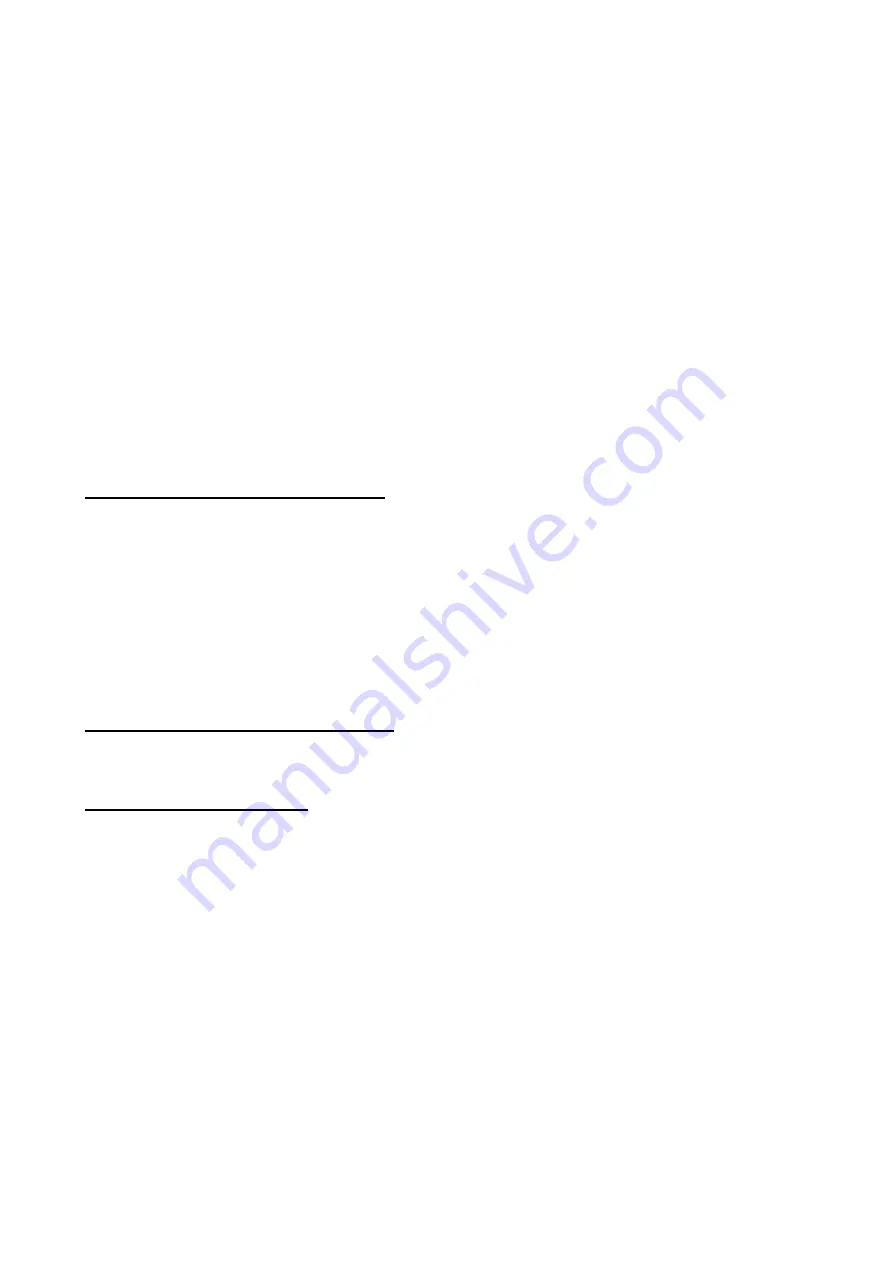
- 22 -
Should it be necessary to add water to the heating system we do so when the boiler is cooled
down to avoid damage to the steel heat exchanger.
b) airtightness of the heating system
c) connection to the chimney
– must be approved by a chimney-sweeping company
d) installation of the ceramic parts in the combustion chamber
e) power supply connection
The sockets are connected so that the protective pin is at the top and the phase wire is connected to the
left side when viewed from the front. The same applies to double sockets.
f) The emission check must be carried out after the first installation in accordance with valid legal
requirements of the country where the boiler is installed.
„Warranty Certificate“ must contain the completion date of the installation as well as information that
a heating test has been carried out.
6.4. Commissioning the boiler
1. Perform the feeder performance test
– see chapter 7.1.
2. Light the boiler up.
3. Bring the boiler to the operating temperature. Recommended operating temperature of the heating water
at the exit point is
65 to 80 ° C.
4. Repeatedly check the airtightness of the boiler.
5. Perform heating test according to the relevant standards (see Warranty Certificate)
6. Inform the user about the operation of the boiler
– see chapter 7.
7. Make entry into the Warranty Certificate.
7. Boiler operation by the user
7.1. Feeder calibration
WARNING!
This is a very important activity. Correct and accurate measurement and setting of ‚Test
fuel quantity‘ in the drive determines the reliability of the boiler operation. Entering an
incorrect value will cause the boiler to malfunction.
The value
Test fuel quantity
defines the amount of fuel that the feeder can deliver to the burner during
continuous operation per unit of time (specifically 6 mins) according to a particular setting and inclination. To
set the value follow the below:
1. Check that the screw feeder is correctly positioned against the tray. The angle between the feeder
and the horizontal floor must be between 0 and
60°, the optimum is 45°.
•
Installation of the feeder at an angle of less than 45
° increases the amount of fuel delivered.
•
Installation of the feeder at an angle of more than 45° reduces the amount of fuel delivered.
2. Fill the tank with the required fuel
– see chapter 3.
Summary of Contents for K14
Page 1: ...BOILER OPERATION AND INSTALLATION GUIDE BENEKOV K14 BENEKOV K20 BENEKOV K25 ...
Page 9: ... 9 Fig 3 BENEKOV K14 boiler basic dimensions ...
Page 10: ... 10 Fig 4 BENEKOV K20 and K25 boiler dimensions ...
Page 17: ... 17 Fig 7 Position of the K14 boiler in a boiler room ...
Page 33: ... 33 Fig 17 Diagram of electrical connection of XS20 burner of the K14 boiler ...
Page 34: ... 34 Fig 18 Diagram of electrical connection of XS26 burner of the K20 and K25 boilers ...