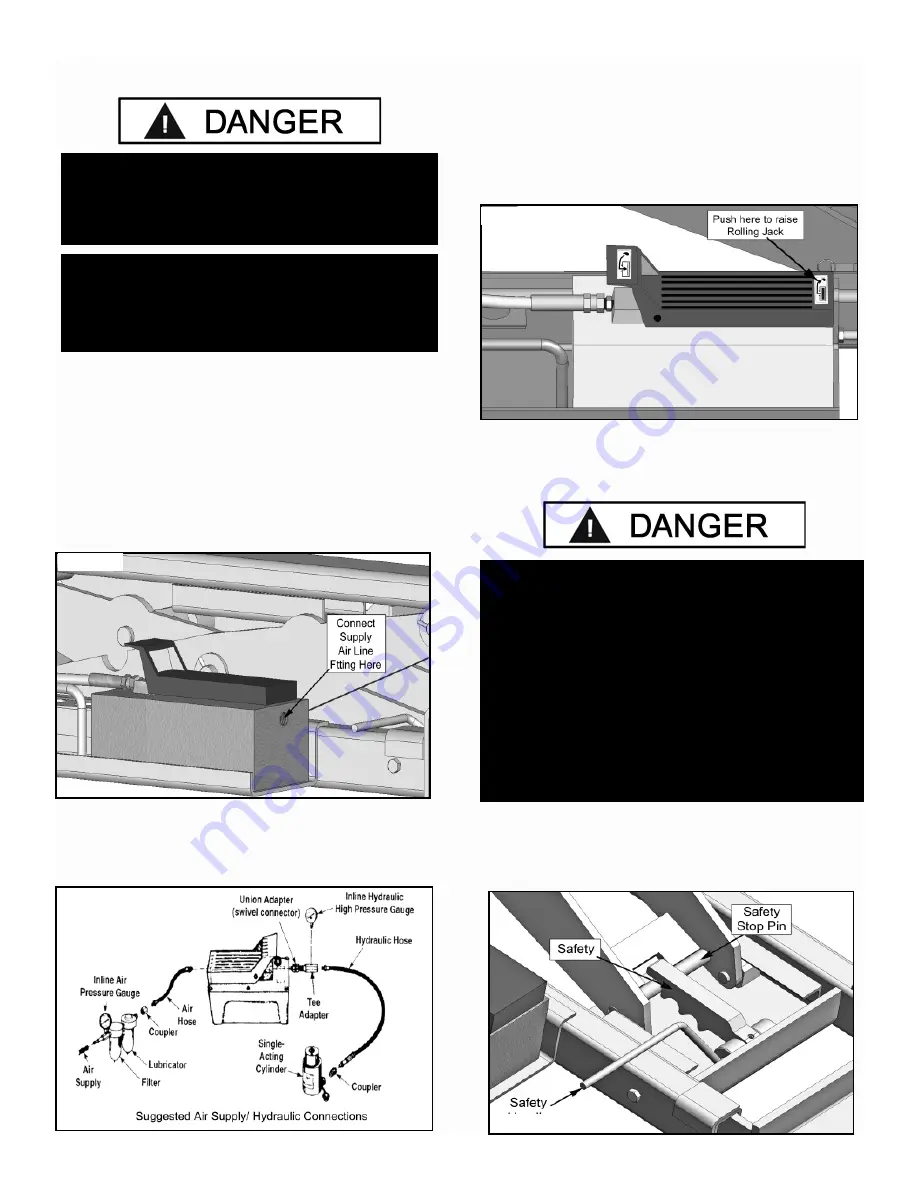
12
STEP 5
(Connecting Air Supply)
Refer to page 18 if installing with the Optional Rolling
Bridge Jack Airline Kit.
1. Remove the thread protector from the air inlet of the
Pump. Select and install the threaded
fi
ttings (not
supplied) which are compatible with your air supply
fi
ttings. The air supply should be 20 CFM / 57 M3/MIN)
and 100 PSI (7 BAR) to obtain the rated hydraulic pressure.
Air Supply should be regulated to a maximum of 125 PSI (8.6
BAR) (See Fig. 5.1)
2. An appropriate air line regulator, water separator and
lubricator should be installed on the Air Supply line. The
absence of these items will void the warranty on pneumatic
components. (See Fig. 5.2)
STEP 6
(Start Up / Final Adjustments)
1. Raise the Jack
WITHOUT
a vehicle to check for proper
operation of the Rolling Bridge Jack.
2. Depress the Pedal on the lifting end to raise the Jack
through the full range of the Jack. (See Fig. 6.1)
Under certain circumstances it may be necessary to prime
the Air Hydraulic Pump Unit. Refer to the manual that came
with the pump for these instructions.
3. Lower the Jack onto the nearest Safety Stop Pin. When
the Jack is loaded with a vehicle make sure the Jack is
resting on the Safety Stop Pin prior to performing any work
on the vehicle. (See Fig. 6.2)
DANGER!
THE AIR SUPPLY SHOULD BE TO
20 CFM (.57 M3/MIN.) AND 100 PSI (7 BAR).
AIR SUPPLY SHOULD BE REGULATED TO A
MAXIMUM OF 125 PSI (8.6 BAR)
DANGER!
DISCONNECT AND / OR RELEASE THE PRESSURE
FROM THE AIR SUPPLY SYSTEM / HOSES BEFORE
PERFORMING ANY INSTALLATION OR MAINTENANCE
OF THE AIR SUPPLY SYSTEM.
DANGER!
VISUALLY CONFIRM THAT ALL PRIMARY
SAFETY LOCKS ARE ENGAGED BEFORE
ENTERING WORK AREA.
Suspension components used on this Jack are
intended to raise and lower the Jack only and are not
meant to be load holding devices. Remain clear of
elevated Jack unless visual confirmation is made that
all primary Safety Locks are fully engaged and
the lift is LOWERED onto the Safety Locks.
Refer to installation /operation manual for proper
Safety Lock procedures and /or further instruction.
Fig. 5.1
Fig. 5.2
Fig. 6.1
Fig. 6.2
Summary of Contents for RJ-12
Page 2: ...2 This page intentionally left blank...
Page 10: ...10 Fig 3 2...
Page 16: ...16...
Page 20: ...20...