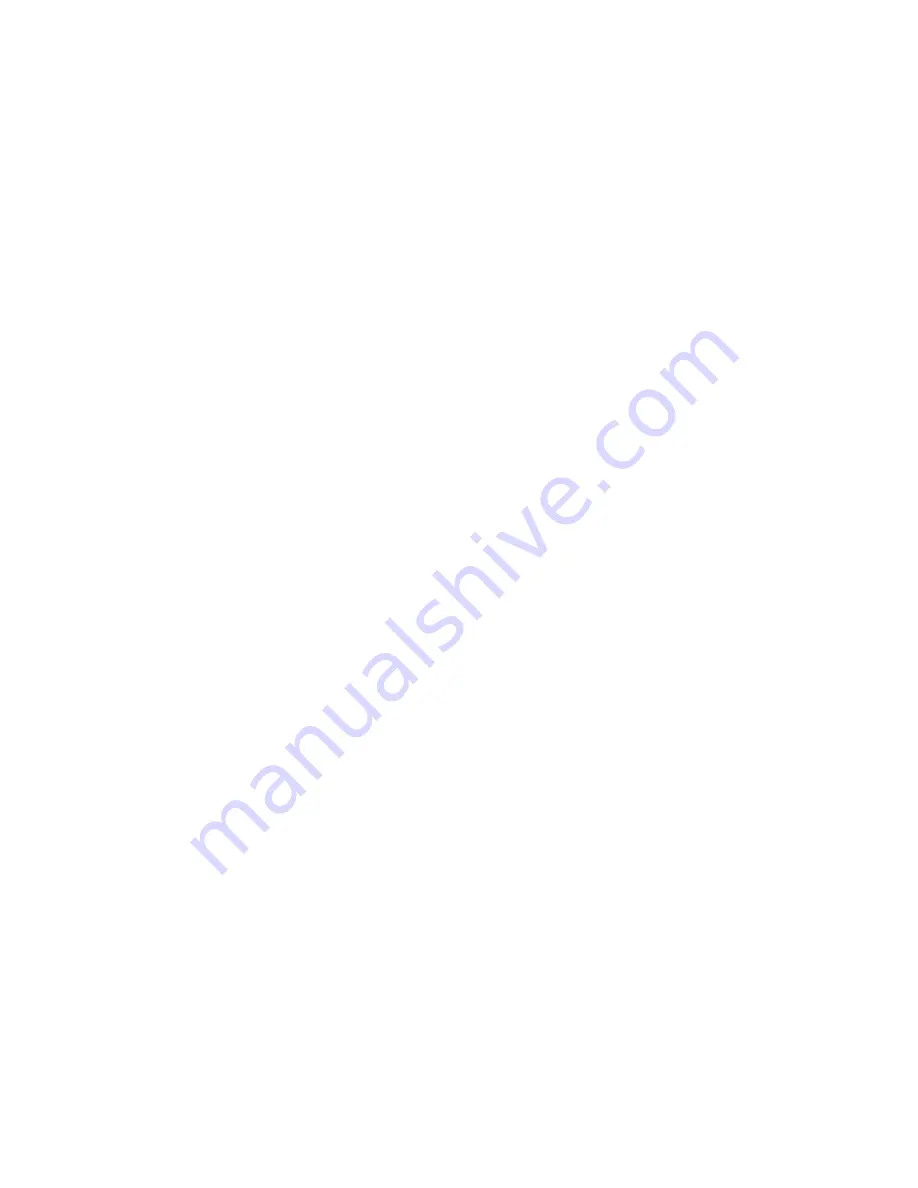
18
Safe Lift Operation
Automotive and truck lifts are critical to the operation and profitability of your business. The safe use of this and other
lifts in your shop is critical in preventing employee injuries and damage to customer’s vehicles. By operating lifts safely
you can insure that your shop is profitable, productive and safe.
Safe operation of automotive lifts requires that only trained employees should be allowed to use the lift.
TRAINING SHOULD INCLUDE, BUT NOT LIMITED TO:
Proper positioning of the vehicle on the runway. (See manufacturers minimize wheel base loading requirements.)
Use of the operating controls.
Understanding the lift capacity.
Proper use of jack stands or other load supporting devices.
Proper use, understanding and visual identification of safety lock devices and their operation.
Reviewing the safety rules.
Proper housekeeping procedures (lift area should be free of grease, oil, tools, equipment, trash, and other debris)
A daily inspection of the lift should be completed prior to its use. Safety devices, operating controls, lift arms
and other critical parts should be inspected prior to using the lift.
All maintenance and repairs of the lift should be completed by following the manufacturer’s requirements. Lift repair
parts should meet or exceed OEM specifications. Repairs should only be completed by a qualified lift technician.
The vehicle manufacturer’s recommendations should be used for spotting and lifting the vehicle.
LIFT OPERATION SAFETY
It is important that you know the load limit. Be careful that you do not overload the lift . If you are unsure what the
load limit is, check the data plate found on one of the lift columns or contact the manufacturer.
The center of gravity should be followed closely to what the manufacturer recommends.
Always make sure you have proper overhead clearance. Additionally, check that attachments, ( vehicle signs,
campers antennas, etc.) are not in the way.
Be sure that prior to the vehicle being raised, the doors, trunk, and hood are closed securely
Prior to being raised, make sure there is no one standing closer than six feet from the lift
After positioning the vehicle on the lift runways, set the emergency brake, make sure the ignition is off, the doors are
closed, overhead obstructions are cleared, and the transmission is in neutral.
Double check that the automatic chock devices are in position and then when the lift is raised, observe the chocks
Put pads or adapters in the right position under the contact points that have been recommended
The lift should be raised just until the vehicle’s wheels are about one foot off the ground. If contact with the vehicle is
uneven or it appears that the vehicle is not sitting secure, carefully lower the lift and readjust.
Always consider potential problems that might cause a vehicle to slip, i.e., heavy cargo, undercoating, etc.
Pay attention when walking under a vehicle that is up on the hydraulic lift.