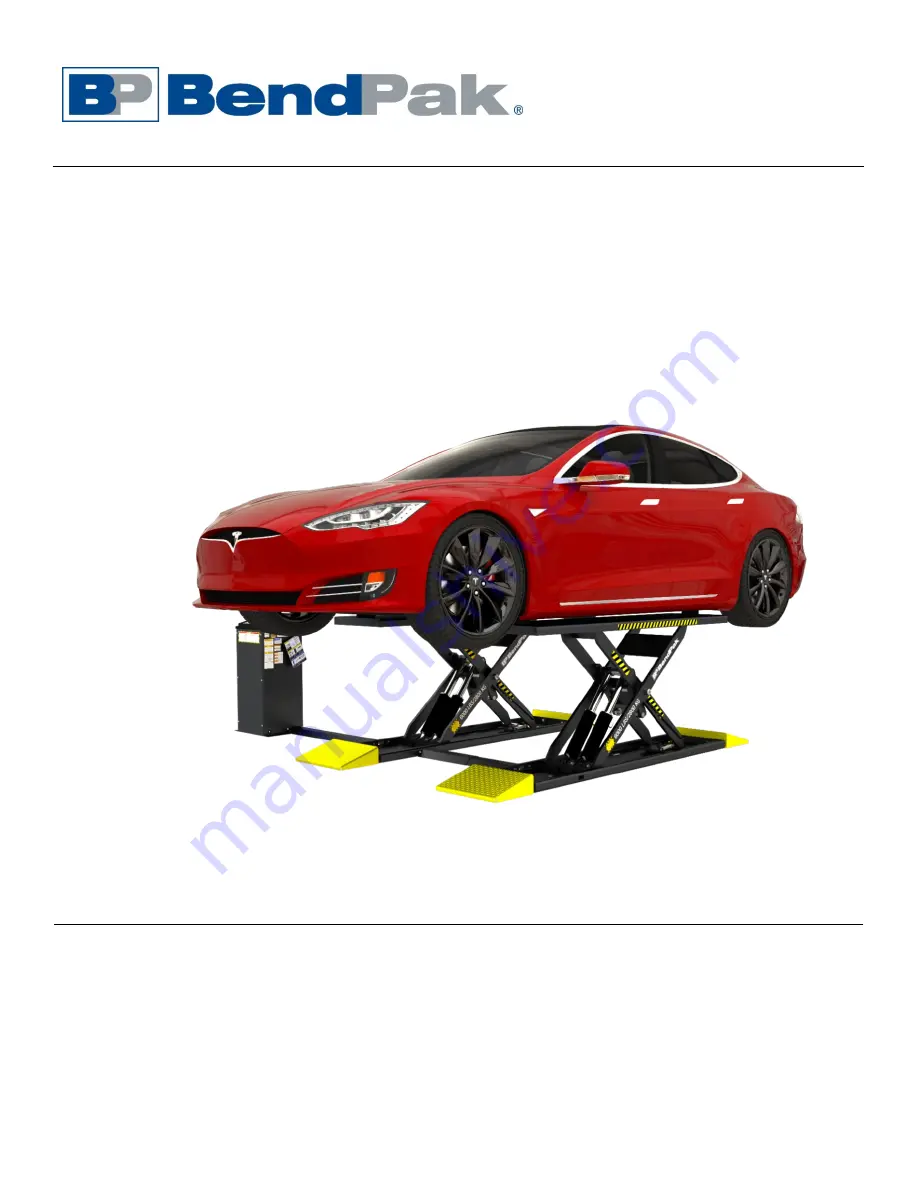
1645 Lemonwood Dr.
Santa Paula, CA, 93060 USA
Toll Free: (800) 253-2363
Tel: (805) 933-9970
Mid-Rise Scissor Lift
Installation and Operation Manual
Manual P/N 5900030 — Manual Revision D — April 2021
Models
: • MDS-6EXT • MDS-6EXTF • MDS-6LP • MDS-6LPF
Model MDS-6EXT shown.
Designed and engineered by BendPak Inc. in Southern California, USA. Made in China.
⚠
DANGER
Read the
entire contents
of this manual
before
using this
product. Failure to follow the instructions and safety precautions in
this manual can result in serious injury or death. Make sure all other
operators also read this manual. Keep the manual near the product
for future reference.
By proceeding with setup and operation,
you agree that you fully understand the contents of this
manual and assume full responsibility of product use
.
Summary of Contents for MDS-6EXT
Page 58: ...MDS 6 Mid Rise Scissor Lifts 58 P N 5900030 Rev D April 2021 ...
Page 73: ...MDS 6 Mid Rise Scissor Lifts 73 P N 5900030 Rev D April 2021 Labels ...
Page 74: ...MDS 6 Mid Rise Scissor Lifts 74 P N 5900030 Rev D April 2021 ...
Page 75: ...MDS 6 Mid Rise Scissor Lifts 75 P N 5900030 Rev D April 2021 ...
Page 76: ...MDS 6 Mid Rise Scissor Lifts 76 P N 5900030 Rev D April 2021 Parts Diagrams ...
Page 77: ...MDS 6 Mid Rise Scissor Lifts 77 P N 5900030 Rev D April 2021 ...
Page 78: ...MDS 6 Mid Rise Scissor Lifts 78 P N 5900030 Rev D April 2021 ...
Page 79: ...MDS 6 Mid Rise Scissor Lifts 79 P N 5900030 Rev D April 2021 ...
Page 80: ...MDS 6 Mid Rise Scissor Lifts 80 P N 5900030 Rev D April 2021 ...
Page 81: ...MDS 6 Mid Rise Scissor Lifts 81 P N 5900030 Rev D April 2021 ...
Page 82: ...MDS 6 Mid Rise Scissor Lifts 82 P N 5900030 Rev D April 2021 ...
Page 83: ...MDS 6 Mid Rise Scissor Lifts 83 P N 5900030 Rev D April 2021 ...
Page 84: ...MDS 6 Mid Rise Scissor Lifts 84 P N 5900030 Rev D April 2021 ...
Page 85: ...MDS 6 Mid Rise Scissor Lifts 85 P N 5900030 Rev D April 2021 ...
Page 86: ...MDS 6 Mid Rise Scissor Lifts 86 P N 5900030 Rev D April 2021 ...
Page 87: ...MDS 6 Mid Rise Scissor Lifts 87 P N 5900030 Rev D April 2021 ...
Page 89: ...MDS 6 Mid Rise Scissor Lifts 89 P N 5900030 Rev D April 2021 Maintenance Log ...
Page 90: ...MDS 6 Mid Rise Scissor Lifts 90 P N 5900030 Rev D April 2021 Maintenance Log ...
Page 91: ...MDS 6 Mid Rise Scissor Lifts 91 P N 5900030 Rev D April 2021 Maintenance Log ...