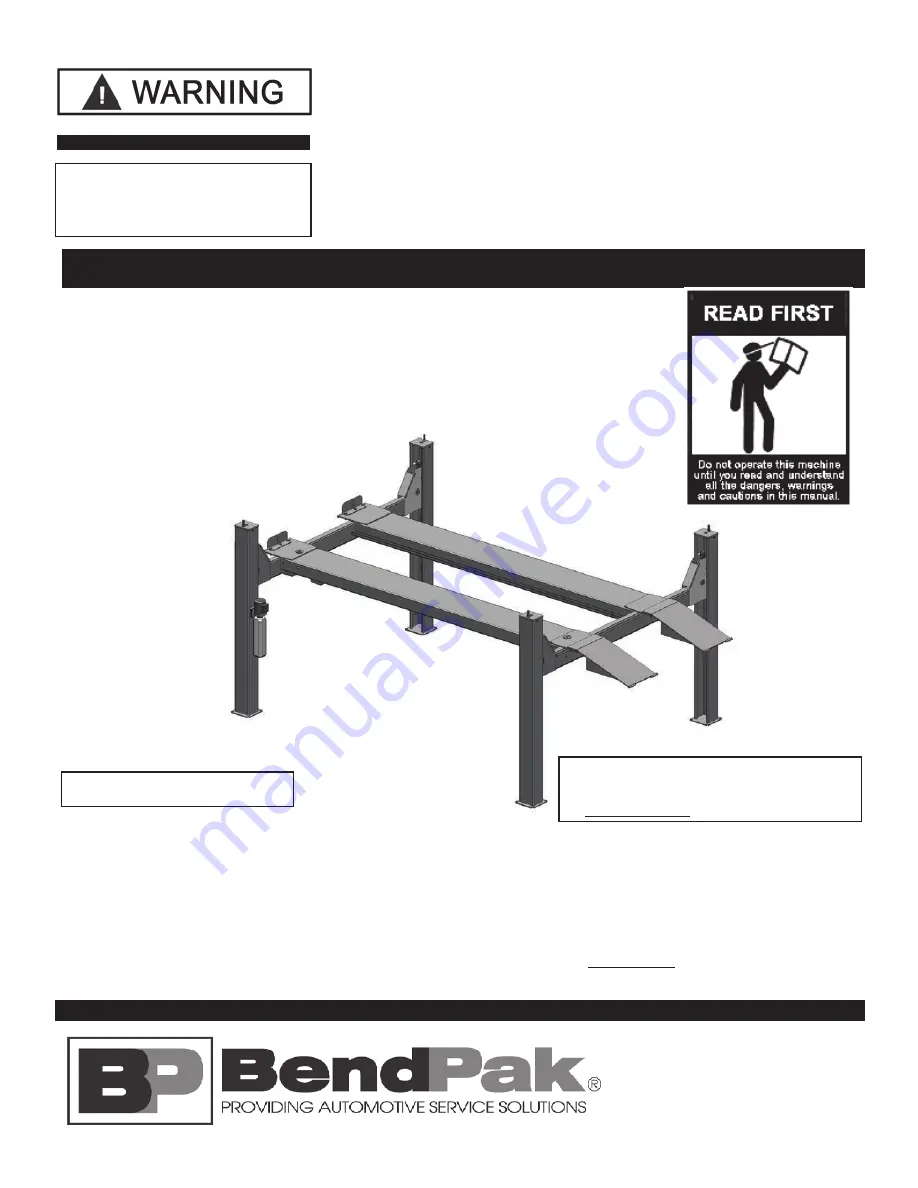
INSTALLATION AND OPERATION MANUAL
SUPER-DUTY
FOUR-POST LIFTS
Models:
HDS-18 / HDS-18X
VER B
HDS-27 / HDS-27X
VER B
HDS-35 / HDS-35X
VER B
HDS-40 / HDS-40X
VER B
IMPORTANT SAFETY INSTRUCTIONS
SAVE THESE INSTRUCTIONS
PLEASE READ THE ENTIRE CONTENTS OF THIS MANUAL PRIOR TO INSTALLATION
AND OPERATION. BY PROCEEDING WITH LIFT INSTALLATION AND OPERATION YOU
AGREE THAT YOU FULLY UNDERSTAND AND COMPREHEND THE FULL CONTENTS
OF THIS MANUAL. FORWARD THIS MANUAL TO ALL OPERATORS. FAILURE TO
OPERATE THIS EQUIPMENT AS DIRECTED MAY CAUSE INJURY OR DEATH.
Manual REV G 05-14-15
pn# 5900160
1645 Lemonwood Dr.
Santa Paula, CA. 93060, USA
Toll Free 1-800-
25
3-
2363
Tel: 1-805-
93
3-
9970
Fax: 1-805-933-9160
www.bendpak.com
RECEIVING
The shipment should be thoroughly inspected as soon as it
is received. The signed Bill of Lading is acknowledgement
by the shipping carrier as receipt of this product as listed
in your invoice as being in a good condition of shipment. If
any of these goods listed on this Bill of Lading are missing
or damaged, do not accept goods until the shipping carrier
makes a notation on the freight bill of the missing or dam-
aged goods. Do this for your own protection.
BE SAFE
Your new lift was designed and built with safety in mind.
However, your overall safety can be increased with proper
training and thoughtful operation on the part of the operator.
DO NOT operate or repair this equipment without reading
this manual and the important safety instructions shown
inside. Keep this operation manual near the lift at all times.
Make sure that ALL USERS read and understand this
manual.
400V 50Hz SUPPLY DETAILS ARE IN-
CLUDED WITH ELECTRICAL CONTROL
BOX. DISREGARD SUPPLY WIRING
DETAILS IN THIS MANUAL
EUROPEAN USERS
ORIGINAL INSTRUCTIONS IN
ENGLISH LANGUAGE
Keep this operation manual near the
machine at all times. Make sure that
ALL USERS read this manual.