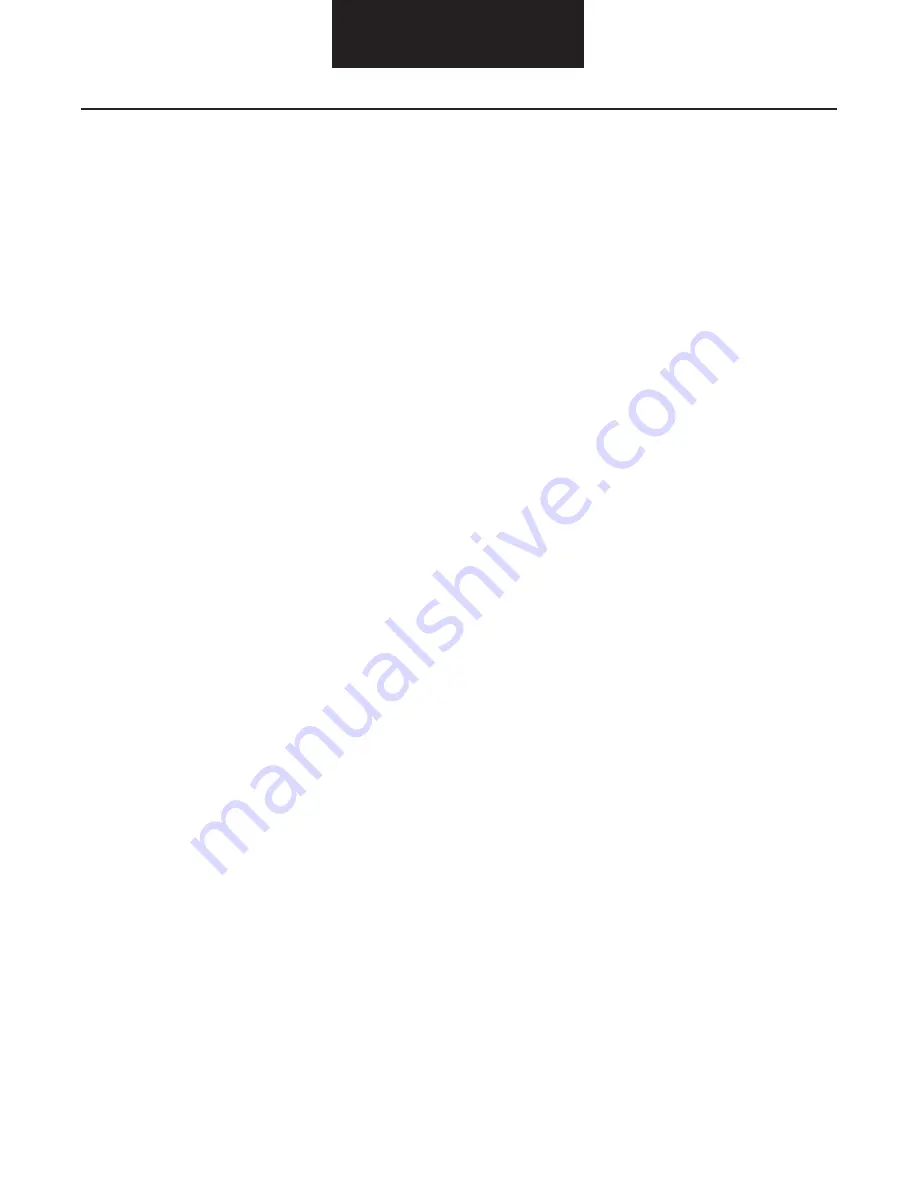
36
Appendix
Retrofi t Information
Retrofi t Recommended Practices
Body builder electrical systems that are to be interconnected with the VS-400 electrical system should adhere to the latest
recommendations of SAE J1292. In addition to SAE J1292, the following recommendations should be followed:
1. All wiring terminals should be properly insulated to prevent "short circuits". All terminals should be of insulation grip design to
provide a reliable connection and to prevent terminal fatigue.
2. Terminals and splices that are connected outside the body should be moisture resistant design. Molded insulator for ring
terminals should be used. Molded connector/insulators are recommended for use with blade or pin type terminals.
3. Wires must be routed to provide at least 3" (75mm) clearance to moving parts, unless positively fastened or protected by conduit.
4. Wire routing should avoid areas where temperatures exceed 80°C [180°F] and a minimum clearance of 6" (150mm) should be
maintained from exhaust system components. Where compliance with this requirement is not possible, heat insulation and heat
shields are required.
5. Wire routing and component mounting (switches, relays, etc.) should be located to be easily removed for service. Do not
surround the components with body structure that will prevent removal for service.
6. Wiring to all circuit components (switches, relays, etc.) in exposed locations shall provide a drip loop to prevent moisture from
being conducted into the device via the wire connection.
7. Routing wiring into wheel splash areas should be avoided. When such routing cannot be avoided, adequate clipping or protective
shielding is required to protect wiring from stone and ice damage.
8. Routing wires under the frame side-members or at points lower than the bottom frame
fl
ange should be avoided to prevent
damage to the wires in off-road operations.
9. The wire retainers and grommets installed by the assembly plant are designed to accommodate only the OEM installed wires.
Additional wiring or tubing must be retained by additional clips. When added wires to tubes are routed through sheet metal
panels, new holes must be used (with adequate wire protection and sealing).
10. All wiring connections to components of the factory-installed system must be accomplished by using the correct mating wire
termination. Connections on studs and ground connections must use ring type terminations.
11. When it is necessary to splice wires, the splice must be adequately crimped to provide a good mechanical and electrical
connection. Double wall heat shrink tubing should be used where the outer wall will provide adequate electrical insulation and the
inner wall melts and seals the splice from the envionrment.
12.
Never add another circuit or splice into the ignition or battery power supplies.
The fuses and curcuit breakers installed
at the assembly plant are designed to protect the wiring and electrical components from overloads. Never remove a factory
installed fuse or circuit breaker and replace with a high value device. If the added electrical device causes "fuse blow", or circuit
breaker cycling, it indicates the total load is too high for the factory-installed circuit protection and requires revisions in the added
circuit; not an increase in fuse or circuit breaker size. In this case, the device cannot be added directly to the circuit, but must be
connected through a separate hang-on switch or relay of the correct capacity, using added wiring of the correct gauge. Failure
to adopt this precaution will lead to switch contacts burning. The following wire table suggests wire gauges for various maximum
current draws and will aid in the selection of the correct wire size. The current capacity of a given wire varies with temperature
and type of insulation, but the following values are generally acceptable. If the total electrical load on the circuit, after the addition
of electrical equipment, is less than the fuse protection in that circuit or less than the capacity of some limiting component
(switch, relay, etc.), the items to be added can be connected directly to that circuit. The connection points and allowable loads
are normally found in the owner's manual. Contact the OEM with any questions.