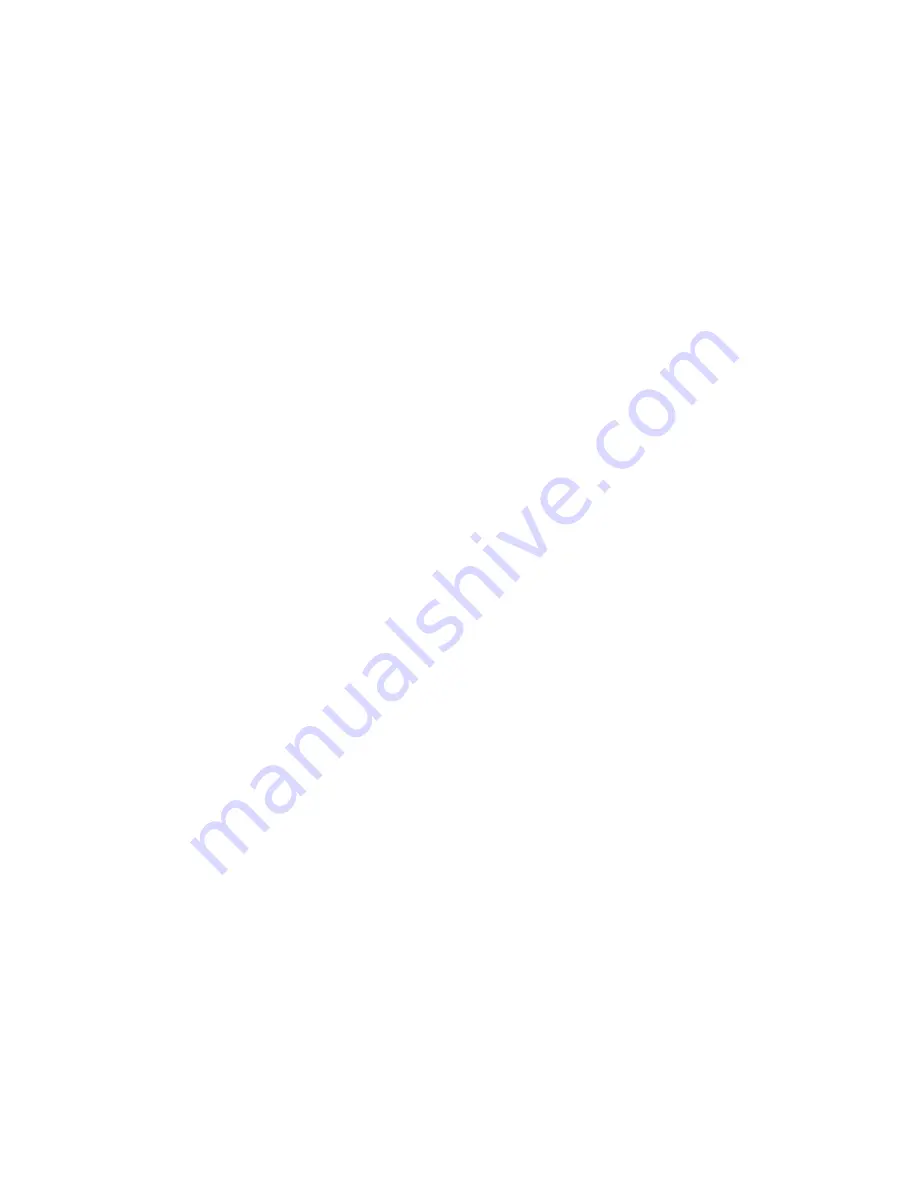
6
If the EC-16
™
controller is programmed for traction control,
it contains the following outputs:
- A connection to the engine's electronic control module
allows the EC-16
™
controller to reduce engine torque under
certain circumstances.
- A traction dash light is connected to and controlled by
the EC-16
™
controller and serves as a means of advising
the driver of the condition of the traction control system.
- A connection to the traction solenoid (located in the
upper portion of the antilock traction relay valve—see Figure
3) is provided via a 2 pin Deutsch connector.
OPERATION - ANTILOCK
PHILOSOPHY
The Bendix
®
EC-16
™
controller antilock system uses
individual sensors, modulators and an electronic controller
to control the four vehicle wheel ends. By monitoring the
deceleration rate during braking, and subsequently adjusting
the brake application pressure at each wheel, the EC-16
™
controller is able to improve braking between the vehicle tire
and the road surface it is on, while maintaining vehicle
stability.
The rear axle brakes are controlled independently; therefore
brake application pressure at an individual wheel is adjusted
solely on the basis of its behavior on the road surface on
which it is traveling.
While each steering axle brake is under the control of an
individual modulator, the EC-16
™
controller does not treat
these brakes totally independently. The EC-16
™
controller
uses a modified individual control philosophy for the steering
axle brakes. This is done in order to minimize "steering
wheel pull" in the event each wheel is traveling on a different
road surface (for example, ice close to the curb and a dry
crown). Essentially the EC-16
™
controller controls the braking
force differences between the two brakes.
The wheel on dry pavement is initially given less braking
force and is brought up to optimum during the stop, while
the wheel on ice attempts to maintain optimum braking during
the entire stop.
In the case of vehicles equipped with tandem rear axles
(6x2, 6x4), the wheel speed sensors are installed at the
wheels on the axle that is most likely to lock first. A single
modulator controls both curb side brakes on the tandem,
and another modulator controls both brakes on the driver's
side of the tandem. With this arrangement of speed sensors
and modulators, both brakes on one side of the tandem are
treated as one since they will most likely be on the same
type of road surface.
NON ANTILOCK BRAKE APPLICATION
During normal braking, air pressure from the brake valve
enters the control port of the service relay valve. The service
relay delivers air to, and through, the antilock modulator
located near the braked wheel, and into the brake actuator.
The service brakes are thus applied. If the wheel sensors do
not detect an impending wheel lock up, the EC-16
™
controller
does not initiate any corrective action and the vehicle comes
to a stop in a normal fashion.
ANTILOCK BRAKE APPLICATION
If a service brake application is made and the wheel speed
sensors detect an impending wheel lockup, the EC-16
™
controller will immediately begin modification of the brake
application using the antilock modulator(s) at the affected
wheel(s). Solenoid valves contained in the modulator are
energized and de energized by the EC-16
™
controller in order
to modify the brake application. When a solenoid coil is
energized, its shuttle moves. Depending upon the function
of the specific solenoid, it either opens or closes, thereby
causing the exhaust or re application of air pressure to the
brake actuator. The solenoids in each modulator are
controlled independently by the EC-16
™
controller. By
opening and closing the solenoid valves in the appropriate
modulator, the EC-16
™
controller is actually simulating what
drivers do when they "pump the brakes". It must be
remembered however that unlike the driver, the EC-16
™
controller is able to "pump" each brake on the vehicle
independently and with far greater speed and accuracy.
OPERATION - TRACTION CONTROL
PHILOSOPHY
Traction control is a natural extension of antilock. Just as
antilock helps vehicle control and stability during braking,
traction control helps during vehicle acceleration. The wheel
speed sensors not only detect rapid decreases in wheel
speed for antilock but also detect unreasonably high
increases for traction control. With traction control, a spinning
wheel is instantly detected and compared with the other
wheels on the vehicle, both front and rear. Two different
methods are used to control wheel spin; torque limiting and
differential braking. Depending upon vehicle type, speed and
road (surface) condition, each method provides a unique
and desirable type of wheel spin control. Ideally both methods
are used to control vehicle traction. While all new version
EC-16
™
controllers are capable of providing wheel control
antilock and traction control (utilizing both methods of
control), not all systems will be configured for both methods.
Depending upon the vehicle, either or both traction control
methods will be activated during the self configuration
procedure.
Summary of Contents for EC-16 ANTILOCK CONTROLLER
Page 31: ...31...