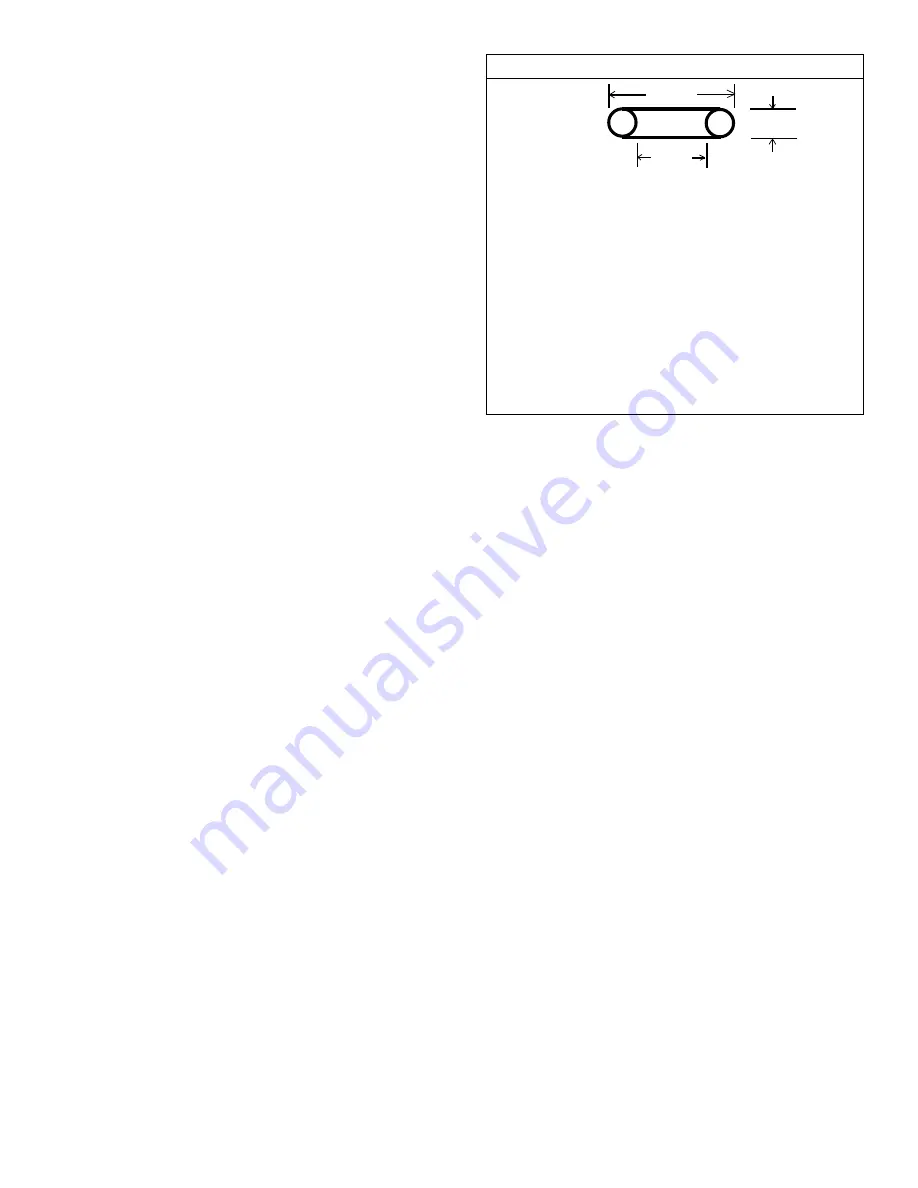
11
3. Install the spring (36) on the inlet seat (37) so that the
small diameter fits over and around the air passage
through the center of the inlet seat.
4. Install o-ring (33) on the check valve seat (32).
5. Using a small amount of grease applied to the check
valve (34) and guide (35) to secure both items to the
check valve seat (32). Gently insert the assembled
items into the valve cover (3). Install the valve guide
(35) so that its flange contains (surrounds) the coils of
the large end of the spring (36), when the valve seat
(32) is installed in the cover (3). Make certain that the
guide (35) is centered over the spring (36), which was
installed in step 3. Note; The check valve must be
installed so that the top hat portion fits into the valve
seat (32).
6. Install the small and large diameter o-rings (27 & 28) on
the check valve seat (23).
7. Install the spring (26) on the inlet seat (29) so that the
small diameter fits over and around the air passage
through the center of the inlet seat.
8. Install the check valve (24) and valve guide (25) in the
check valve seat (23). Note: The check valve must be
installed so that the top hat portion fits into the valve
seat (23). Install the valve guide (25) so that its flange
contains (surrounds) the coils of the large end of the
spring (26), when the valve seat (23) is installed in the
cover (3). Use a small amount grease to hold these
parts in the valve seat (23).
9. Install the assembled valve seat (23) with the check
valve and valve guide (24 & 25) into the cover (3) bore
and while holding it in place install the retaining ring
(22). Make certain the retaining ring is fully seated in
its groove.
10. Install the valve retainer (10) on the inlet and exhaust
valve (11) so that the flange of the retainer (10)
surrounds the rubber portion of the valve. Install the
inlet and exhaust valve in the body (4).
11. Install the inlet and exhaust valve return spring (9) in
the body (4).
12. Install the large and small diameter o-rings (7 & 8) in
the exhaust cover (6), then install the exhaust cover in
the body (4) taking care not to damage the o-rings. Hold
the exhaust cover in place.
13. While depressing the exhaust cover (6), install the
retaining ring (5) in the body (4). Make certain the
retainer (5) is fully seated in its groove in the body.
14. If the valve was equipped with a relay piston return spring
(20), install the spring in the body, large diameter first.
15. Using lubricant to hold them in place, install the large
and small sealing rings (18 & 17) on the cover (3).
16. Install the o-ring (21) on the relay piston (19), then install
the piston in the body (4).
17. Note the relationship marks made prior to disassembly,
then install the cover (3) on the body (4). Secure the
cover on the body using the two, short cap screws (16).
Again, noting the relationship marks, secure the bracket
(15) on the cover (3) and body (4) and using the two
long cap screws (12) and two nuts and washers (13).
Torque the four cap screws to 120 to 150 lb. in.
18. Install the two cap screws (14) that secure the bracket
(15) to the cover (3) and torque to 180 - 220 pound
inches.
19. Noting the relationship marks made during
disassembly, secure the controller (1) or cover plate to
the cover (3) using the four cap screws (2). Torque
the four cap screws to 50-80 pound inches.
20. Install all air line fittings and plugs making certain thread
sealing material does not enter the valve.
Install the rebuilt valve on the vehicle and perform the
OPERATION AND LEAKAGE TESTS before placing the
vehicle in service.
Key Description Qty.
I.D.
O.D.
W
7
O-Ring
1
1.424 1.630 0.103
8
O-Ring
1
0.862 1.068 0.103
18
O-Ring
1
3.487 3.693 0.103
21
O-Ring
1
3.234 3.512 0.139
27
O-Ring
1
1.362 1.568 0.103
28
O-Ring
1
1.114 1.254 0.070
30
O-Ring
1
1.356 1.496 0.070
31
O-Ring
1
1.176 1.316 0.070
33
O-Ring
1
1.176 1.316 0.070
38
O-Ring
1
1.176 1.316 0.070
39
O-Ring
1
0.801 0.941 0.070
40
O-Ring
1
0.739 0.879 0.070
12345
12345
12345
12345
12345
1234
1234
1234
1234
1234
W
O.D.
I.D.
O-RING IDENTIFICATION