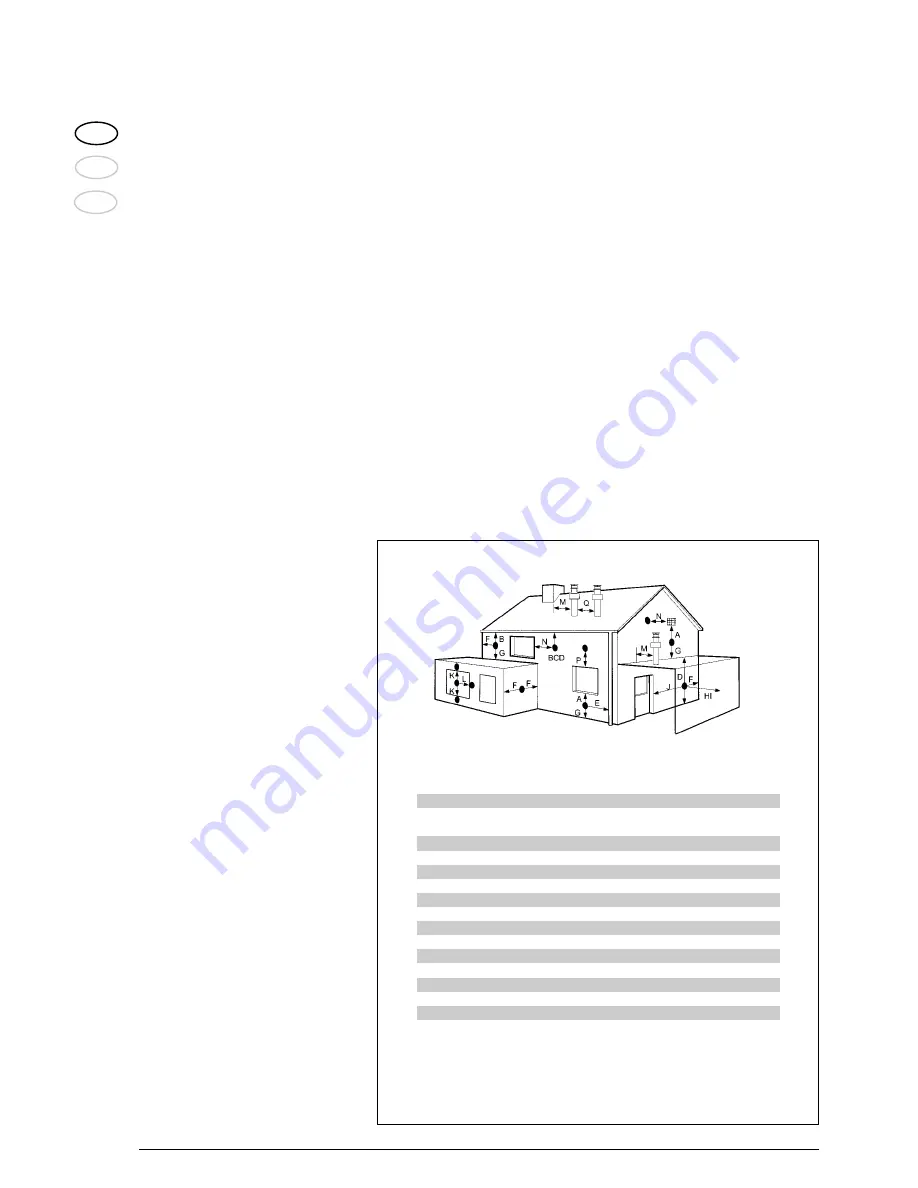
10
ENG
IT
ES
2.1
STATUTORY REQUIREMENTS
GAS SAFETY (INSTALLATION AND USE)
REGULATIONS (as amended). It is the law
that all gas appliances are installed by a
registered person, in accordance with the
above regulations. Failure to install
appliances correctly could lead to
prosecution. It is in your own interest, and
that of safety, to ensure that the law is
complied with.
In addition to the above regulations, this
appliance must be installed in accordance
with the current IEE Wiring Regulations (BS
7671), Local Building Regulations, the
Building Standards (Scotland)
(Consolidation) Regulations, Byelaws of the
local water undertaking, and Health and
Safety Document No 635 “The Electricity at
Work Regulations 1989”. It should also be in
accordance with the relevant
recommendations in the current editions of
the following British Standards and Codes
of Practice: BS5449, BS5546, BS5440:1,
BS5440:2, BS6798, BS6891, and
BG.DM2, BS7074, and BS5482 for
propane installations.
Manufacturer’s instructions must NOT be
taken in any way as over-riding statutory
obligations.
2.2
BOILER POSITION
In siting the combination boiler, the following
limitations MUST be observed:
– The boiler is not suitable for external
installation. The position selected for
installation should be within the building,
unless otherwise protected by a suitable
enclosure, and MUST allow adequate
space for installation, servicing, and
operation of the appliance, and for air
circulation around it (section 2.4).
– This position MUST allow for a suitable
flue termination to be made. The
combination boiler must be installed on a
flat vertical wall which is capable of
supporting the weight of the appliance,
and any ancillary equipment.
– If the combination boiler is to be fitted in
a timber framed building it should be
fitted in accordance with the Institute of
Gas Engineers document for Gas
Installations In Timber Frame Housing,
Reference 16E/UP/7: 1998. If in doubt,
advice must be sought from the gas
supplier.
– If the appliance is installed in a room
containing a bath or shower, any
electrical switch or control utilising mains
electricity must be so situated that it
cannot be touched by a person using the
bath or shower. Attention is drawn to the
requirements of the current I.E.E. Wiring
Regulations (BS 7671), and in Scotland
the electrical provisions of the Building
Regulations applicable in Scotland.
– A compartment used to enclose the
appliance MUST be designed and
constructed specifically for this purpose.
An existing cupboard, or compartment,
may be used provided it is modified
accordingly.
– Where installation will be in an unusual
location, special procedures may be
necessary. BS6798 gives detailed
guidance on this aspect.
2.3
FLUE TERMINAL POSITION
Detailed recommendations for flue
installation are given in BS5440:1. The
following notes are for general guidance:
– The boiler MUST be installed so that the
terminal is exposed to the external air.
– It is important that the position of the
terminal allows free passage of air
across it at all times.
– It is ESSENTIAL TO ENSURE, in practice
that products of combustion discharging
from the terminal cannot re-enter the
building, or any other adjacent building,
through ventilators, windows, doors,
other sources of natural air infiltration, or
forced ventilation/air conditioning. If this
does occur, the appliance MUST be
turned OFF IMMEDIATELY and the gas
supplier consulted.
–
The minimum acceptable dimensions from
the terminal to obstructions and
ventilation openings are specified in fig. 4.
– If the terminal discharges into a pathway
or passageway check that combustion
products will not cause nuisance and that
the terminal will not obstruct the
passageway.
– Where the lowest part of the terminal is
fitted less than 2 m (78 in) above ground,
above a balcony or above a flat roof to
which people have access, the terminal
MUST be protected by a purpose
designed guard.
– Where the terminal is fitted within 850
mm (34 in) of a plastic or painted gutter,
or 450 mm (18 in) of painted eaves, an
aluminium shield at least 1,500 mm (59
in) long must be fitted to the underside of
the painted surface.
– The air inlet/outlet flue duct MUST NOT
be closer than 25 mm (1 in) to
combustible material.
– In certain weather conditions the
terminal may emit a plume of steam. This
is normal but positions where this would
cause a nuisance should be avoided.
2
INSTALLATION
Fig. 4
TABLE 3
Terminal position
Minimum spacing in mm
A
Directly below an openable window,
300
air vent or any other ventilation opening
B
Below guttering, drain pipes or soil pipes
25 *
C/D
Below eaves, balconies or carport roof
25 *
E
From vertical drain pipes or soil pipes
75
F
From internal or external corners
25
G
Above adjacent ground, roof or balcony level
300
H
From a surface facing the terminal
600
I
From a terminal facing the terminal
1,200
J
From an opening in the carport (e.g. door, window into dwelling) 1,200
K
Vertically from a terminal on the same wall
1,500
L
Horizontally from a terminal on the same wall
300
M
Horizontally from a vertical terminal to a wall
300
N
Horizontally from an openable window or other opening
300
P
Above an openable window or other opening
300
Q
From an adjacent vertical terminal
600
* With “heat shield” installed in accordance to BS 5440 Pt1.
Summary of Contents for Metropolis DGT 25 BF
Page 3: ......
Page 34: ...34 ENG IT ES NOTES...