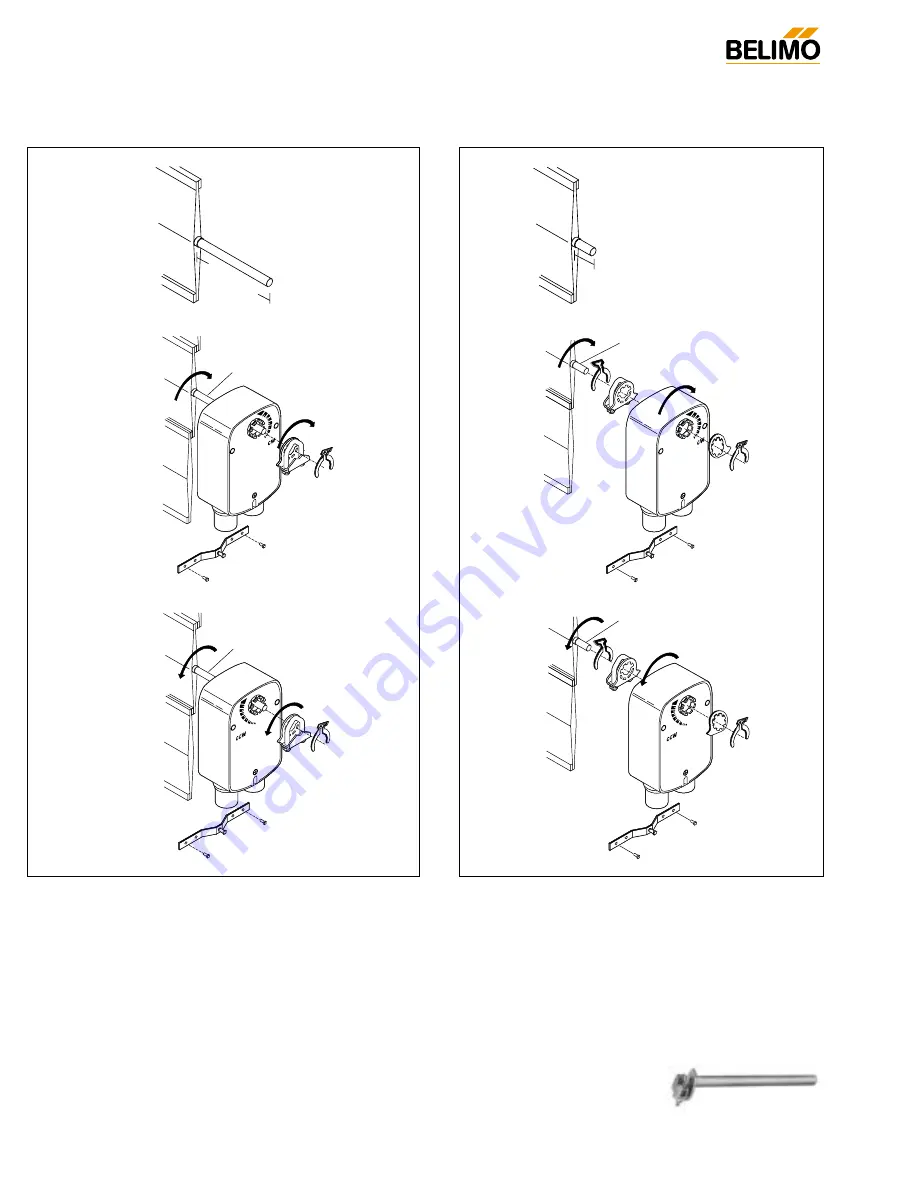
88
J20741 - Subject to change. © Belimo Aircontrols (USA), Inc.
Preliminary steps
1. Belimo actuators should be mounted indoors in dry, rela-
tively clean environment free from corrosive fumes. If the
actuator is to be mounted outdoors, a protective enclosure
must be used to shield the actuator. (See Belimo
Mechanical Accessories )
2. For new construction work, order dampers with extended
shafts. Instruct the installing contractor to allow space for
mounting and service of the Belimo actuator on the shaft.
3. For standard mounting, the damper shaft must extend at least
3 1/2" from the duct. If the shaft extends less than 3 1/2", the
actuator may be mounted in its
short shaft configuration. If an
obstruction blocks access, the
shaft can be extended with the
AV 10-18 shaft extension. (K6-1 is required)
Installation Instructions
Quick-Mount Visual Instructions
min 3 1/2”
[90]
min 3 1/2”
[90]
min 3/4”
[20]
IND-LF Position Indicator
(optional)
min 3/4”
[20]
IND-LF Position Indicator
(optional)
1. Rotate the damper to its failsafe position. If the shaft rotates
counterclockwise, mount the “CCW” side of the actuator out. If it
rotates clockwise, mount the actuator with the “CW” side out.
2. If the universal clamp is not on the correct side of the actua-
tor, move it to the correct side.
3. Slide the actuator onto the shaft and tighten the nuts on the
V-bolt with a 10mm wrench to 6-8 ft-lb of torque.
4. Slide the anti-rotation strap under the actuator so that it
engages the slot at the base of the actuator. Secure the
strap to the duct work with #8 self-tapping screws.
NOTE: Read the “Standard Mounting” instructions, on the next
page, for more detailed information.
min 3 1/2
”
[90]
min 3/4
”
[20]
®
Standard
Mounting
Short Shaft
Mounting
Dimensions
[All numbers in brackets are in millimeters.]