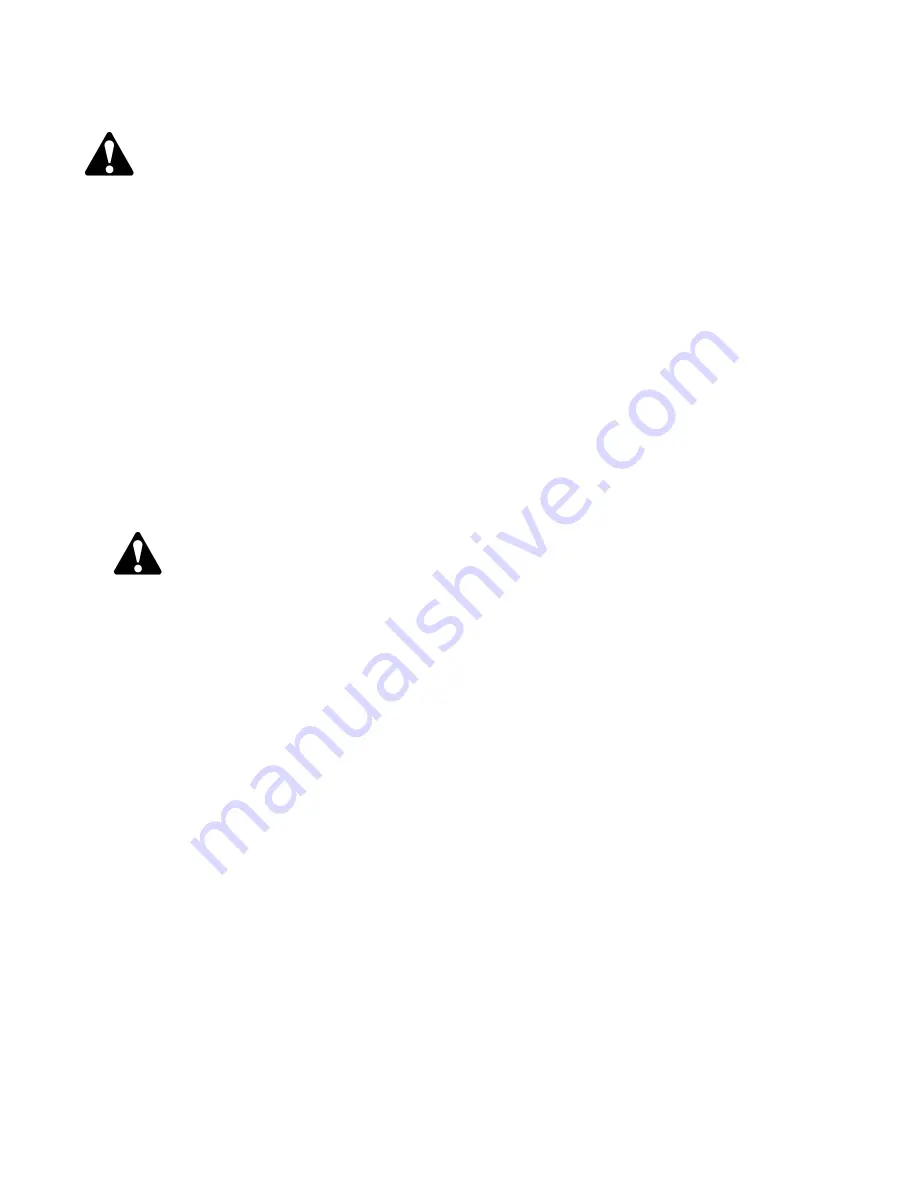
Feeding
The BWC may be available in either gravity or hydraulically feed.
Danger: If gravity feed be careful not to reach into the feed hopper further than the curtain.
To r each
further, use a stick or branch to push any material into the disc that does not go in on its own.
To begin operations, slowly slide the material to be chipped into the hopper. Allow it to feed on its own without excret-
ing much pressure.
Plugging
If plugging occurs, following these procedures:
Stop the engine, remove the ignition key and place it in your pocket and wait for all moving parts to stop before unplugging.
Pull the material out of the
feed hopper
. Be sure all the material is out and nothing is jammed or wedged between the input
opening and the rotor.
Pull the material out of the discharge hood. Use a stick to poke loose any material jammed into the
discharge hood
. Do not
allow anything to remain in this area.
If severe plugging occurs
:
Danger: Ensure the engine is off and you have pocked the key to prevent unintentional startup.
Loosen the feed hopper anchor nuts and raise the feed hopper. Remove material from inside the rotor compartment.
Clean out the discharge area/rotor.
Open the
rotor cover
and clean out the housing. Be sure to turn the rotor by hand to be sure there is nothing jammed be-
tween the rotor and stationary blades.
Close, install and fold down all components opened to unplug. Tighten fasteners to their specified torque.
Check that everyone is clear of machine before restarting engine.
Start the engine, engage the PTO and resume working.
Sharpening Blades:
The rotor blades and anvil need to be sharp for the chipper to perform as expected. It is recommended that the rotor blades
be removed from the rotor when sharpening. Always sharpen the blades at a 45° angle to provide the best cutting effect as
it meets the anvil. Be sure to tighten the blade mounting bolts to their specified torque when re-installing the blades to the
rotor.
The stationary blade is designed with 4 sharp corners that can be utilized. When the corner facing the rotor blade rounds
over, remove the blade and re-install with a different corner facing the rotor blade. Use the anvil to set the clearance to the
rotor blade when re-installing. Be sure to tighten mounting bolts to their specified torque.
The drive system is designed to function well without failing the shear pin. If it does fail, generally it is being fed too fast
or something very hard has been jammed into the rotor or between the blades. Always unplug the sys- tem and determine
the cause of the problem and correct it before resuming work
11