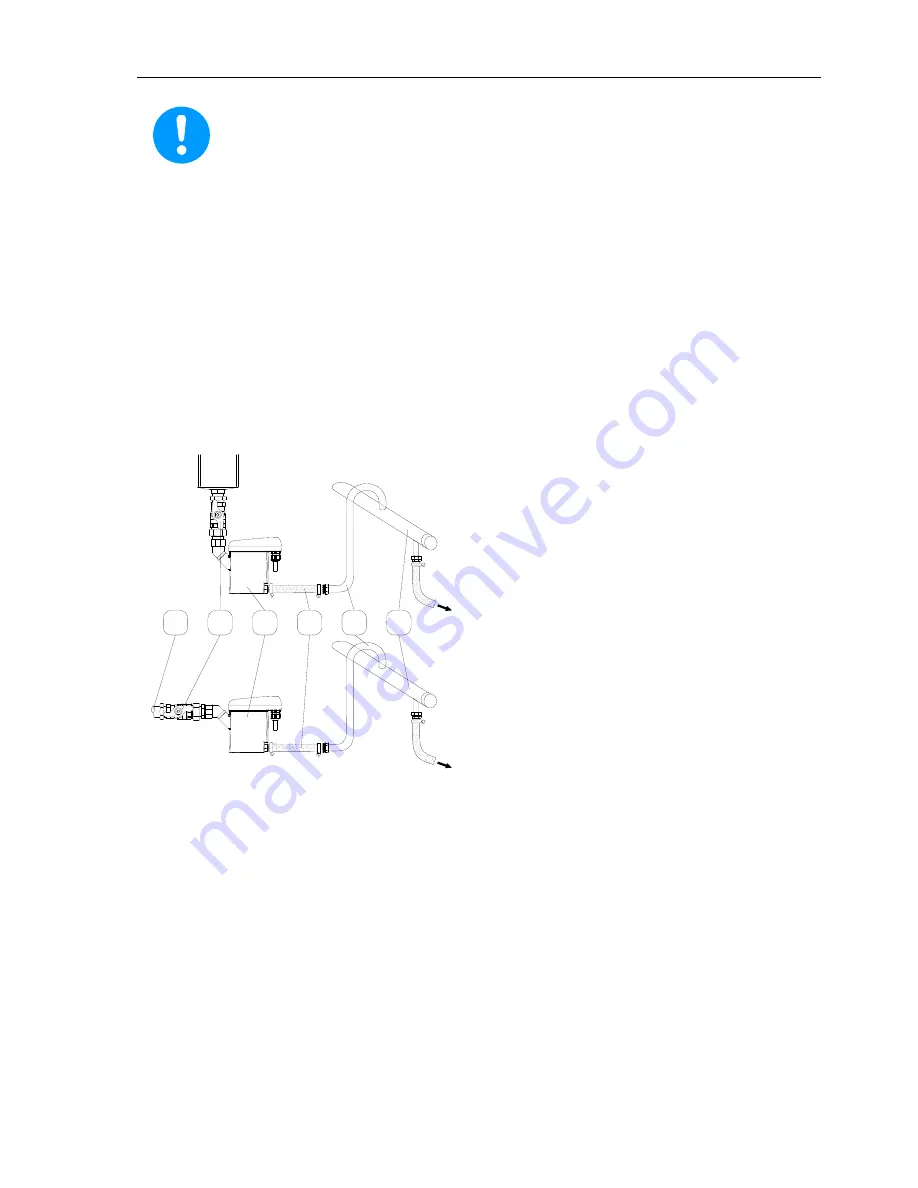
Installation
BEKOMAT® 32U
15
Note:
It is imperative to observe all hazard statements and warnings listed here.
Please also observe all regulations and notes regarding industrial safety and fire prevention at the place
of installation.
As a matter of principle, only use suitable and appropriate tools and materials in a proper condition.
Do not use aggressive cleaners and improper devices such as high-pressure cleaners.
Please note that condensates may contain aggressive or harmful components. Therefore, skin contact
should be avoided.
Condensate is subject to mandatory waste disposal. As such, it must be collected in suitable containers,
and disposed of or processed properly.
Installation instructions:
• Only the displayed installation position of the
BEKOMAT
®
(3) is permissible. Never install in a
horizontal or any other tilted position.
• Feed pipe (1) and ball valve (2) at least G½.
• No filter or screen in the inlet line.
• Slope in the inlet line >1%.
• Use ball valves (2) only.
• Operating pressure: min. 0,8 bar (12 psig),
max. 16 bar (230 psig).
• Short pressure hose
(4)
fixed on a
pressure-resistant pipe.
• The required minimum pressure increases by
0,1 bar (1,4 psi) per metre gradient in the
discharge pipe (5).
• Discharge pipe (5) rising by max. 5 m (16,4ft).
• Install manifold (6) ½" with a slope of 1%.
• Introduce the discharge pipe (5) from the top
into the manifold (6).
• Prior to the start-up, always carry out a leak test
and verify the correct engagement of the control
unit.
1
2
3
4
5
6