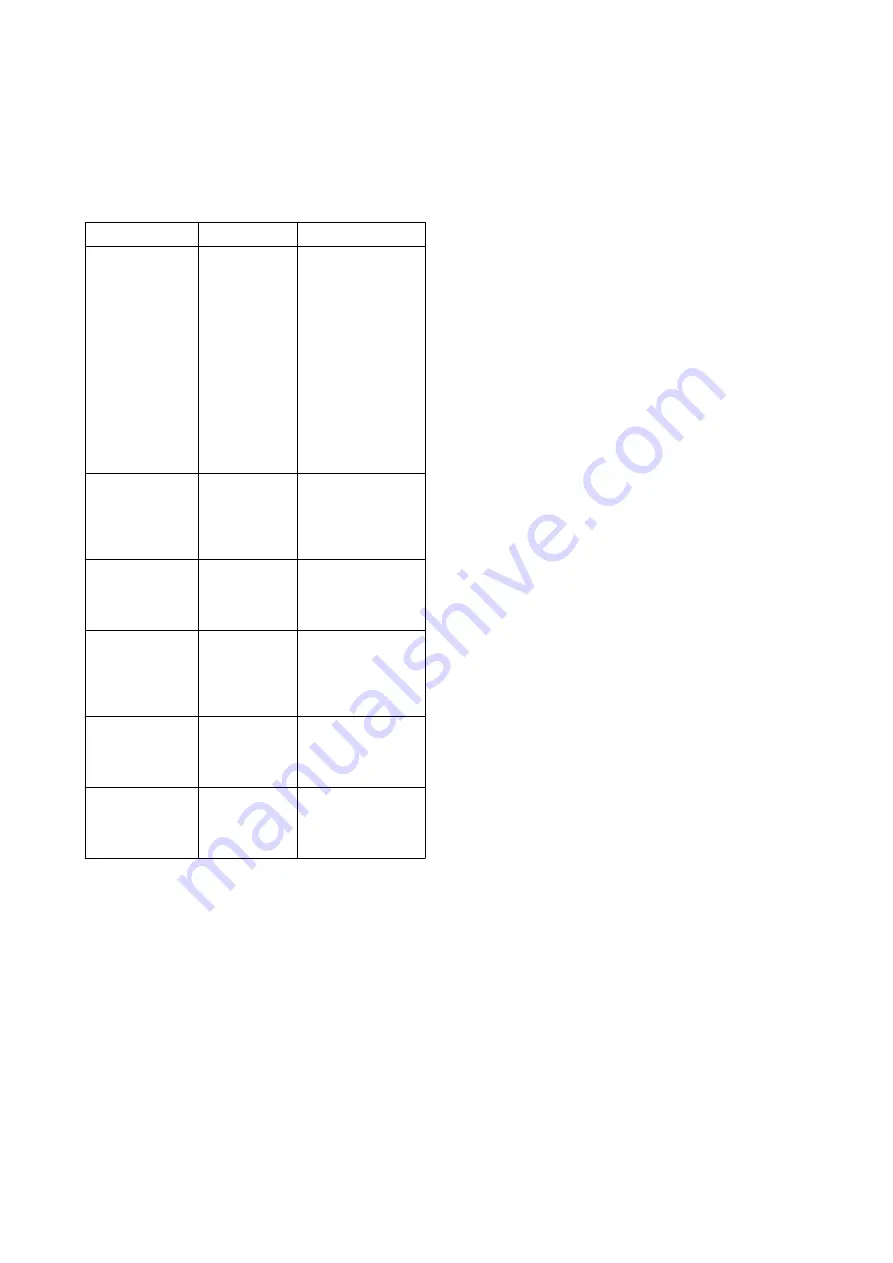
19
8.
MAINTENANCE
8.1
Fault finding during commissioning
If
an
indicator
fails
to
function
during
commissioning the following procedure should be
followed:
Symptom
Cause
Solution
No display
Incorrect
wiring
Check wiring
There should be
2.0 to 5.3V
between terminals
1 & 3 with terminal
1 positive.
With an optional
backlight there
should be 5.8 to
9.1V between
terminals 1 & 3 with
terminal 1 positive.
No display
0V between
terminals 1 & 3.
Incorrect
wiring or no
power supply
Check supply
voltage and voltage
drop caused by all
the instruments in
the loop.
All decimal points
flashing.
Overrange or
underrange if
-ve sign is
displayed.
Recalibrate the
numerical display.
Unstable display 4/20mA input
is noisy.
Eliminate ripple on
4/20mA power
supply and/or
decrease indicator
resolution.
Indicator displays
LpLo
4/20mA input
is too low.
Measure 4/20mA
current and ensure
that it is above
3mA.
Unable to enter
configuration
menu.
Incorrect
security code
entered.
Enter correct
security code, or
contact BEKA if the
code has been lost.
8.2
Fault finding after commissioning
ENSURE PLANT SAFETY BEFORE
STARTING MAINTENANCE
The BA304SG and BA324SG are Ex eb and
Ex tb certified indicators. The instrument
enclosure should only be opened when
the
indicator
is
de-energised,
or
a
gas/dust clearance certificate has been
issued.
If an indicator fails after it has been functioning
correctly, follow the procedure shown in section
8.1. If this does not reveal the cause of the fault, it
is recommended that the instrument is replaced.
8.3
Servicing
BA304SG and BA324SG loop powered indicators
are interchangeable. A single spare instrument
assembly may quickly be recalibrated to replace
any instrument that is damaged or fails.
No
attempt should be made to repair instruments at
component level.
We recommend that faulty instruments are
returned to BEKA associates or to your
local BEKA agent for repair.
8.4
Routine maintenance
The mechanical condition of the instrument and
electrical calibration should be regularly checked.
The interval between inspections depends upon
environmental conditions.
8.5
Guarantee
Indicators which fail within the guarantee period
should be returned to BEKA associates or our local
agent. It is helpful if a brief description of the fault
symptoms is provided.
8.6
Customer comments
BEKA associates is always pleased to receive
comments from customers about our products and
services. All communications are acknowledged
and
whenever
possible,
suggestions
are
implemented.