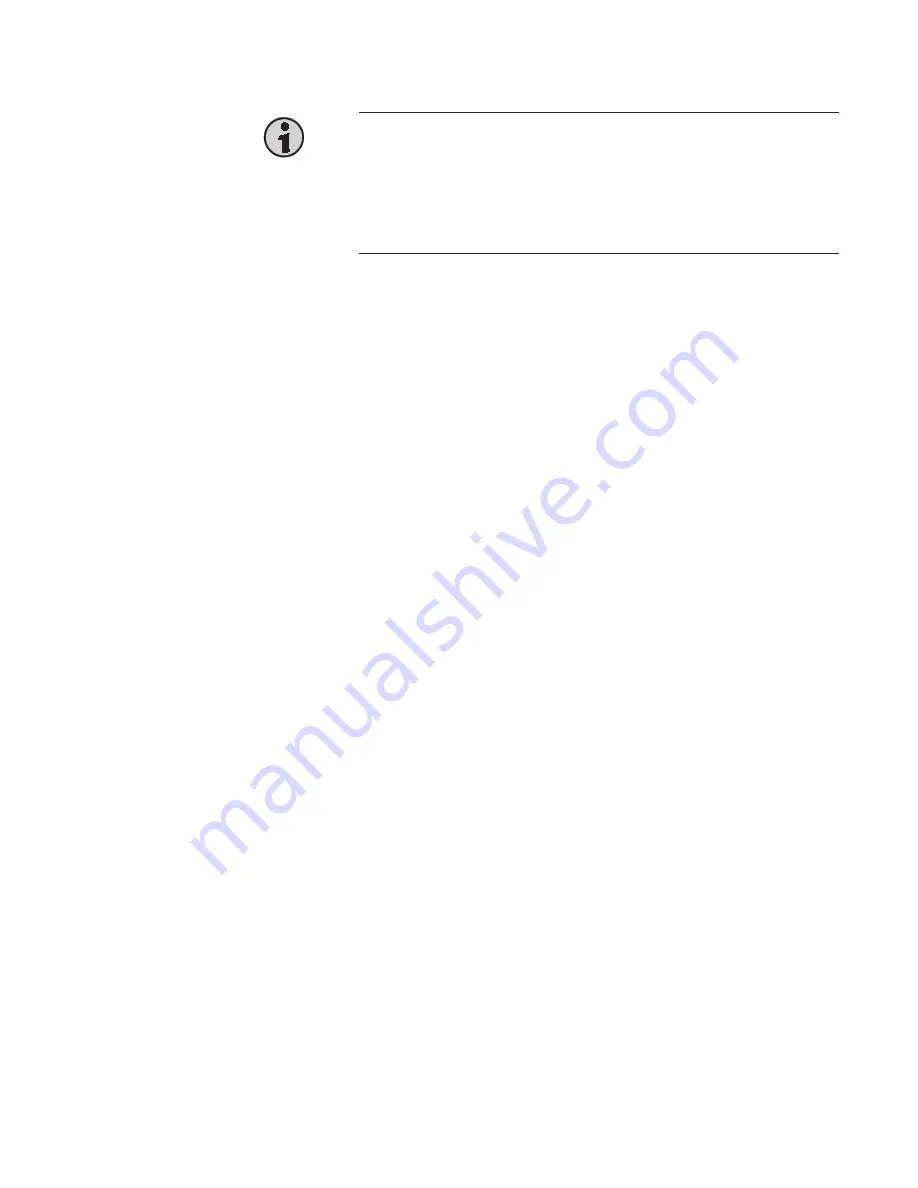
2-1
Part 2
Mechanics manual
Hint
This part of the operating instructions contains all information required to put
the machine into operation and to do programming, troubleshooting and
maintenance. It adresses to trained technical personnel, which is able to
overview their tasks and recognize possible danger at an early moment. The
operating instructions given in part 1 of this manual are to be considered as
part of this mechanics manual.
Contents
Page
Part 2
Mechanics manual ............................................................................................. 2-1
1
Delivery, transportation, storage ...................................................................... 2-2
1.1
Delivery ................................................................................................................ 2-2
1.2
Transportation ...................................................................................................... 2-2
1.3
Storage ................................................................................................................ 2-2
2
Installation .......................................................................................................... 2-3
2.1
Technical data ...................................................................................................... 2-3
2.2
Mechanical installation ......................................................................................... 2-3
2.2.1
Unpack and put up ............................................................................................... 2-3
2.2.2
Connection of air supply ....................................................................................... 2-4
2.3
Elektrical installation ............................................................................................ 2-4
2.4
First putting into operation .................................................................................... 2-5
3
Programming instructions and machine setup ............................................... 2-6
3.1
General hints ....................................................................................................... 2-6
3.2
Selection of the setup pages ................................................................................ 2-6
3.3
Setup page -01 .................................................................................................... 2-7
3.4
Setup page -02 .................................................................................................... 2-7
3.4.1
Position actor, turn direction, needle position ....................................................... 2-7
3.4.2
Revs (min. and max.) ........................................................................................... 2-8
3.4.3
Foot pedal ............................................................................................................ 2-9
3.4.4
Cover Page .......................................................................................................... 2-9
3.4.5
Store error messages .......................................................................................... 2-9
3.4.6
Enable access code ........................................................................................... 2-10
3.5
Setup page -03 .................................................................................................. 2-10
3.5.1
Thread cutter ..................................................................................................... 2-10
3.5.2
After thread cutting, time until sewing foot up ...................................................... 2-11
3.5.3
Presser foot ........................................................................................................ 2-11
3.5.4
Needle cooling ................................................................................................... 2-12
3.5.5
Step motors: pinking mechanism and metering ................................................. 2-12
3.5.6
Tape transportation ............................................................................................ 2-13
3.6
Setup page -10 .................................................................................................. 2-13
3.7
Program inputs and outputs ............................................................................... 2-14
3.7.1
Setup page of inputs and outputs ....................................................................... 2-14
3.7.2
Settings for this machine .................................................................................... 2-15
3.8
Meanings of the used symbols ........................................................................... 2-16
4
Use of the storage module .............................................................................. 2-18
4.1
Load data from the storage module ................................................................... 2-18
4.2
Write data on the storage module ...................................................................... 2-19
4.3
Write single programs on the storage module .................................................... 2-19
4.4
Read a single sewing program into the machine control .................................... 2-20
5
Troubleshooting hints ..................................................................................... 2-21
5.1
Error – possible solution ..................................................................................... 2-21
5.2
Error messages in the display – possible solution .............................................. 2-21
5.3
Hints for several repair duties ............................................................................ 2-22
Summary of Contents for 1500/70 Series
Page 24: ...1 22 ...