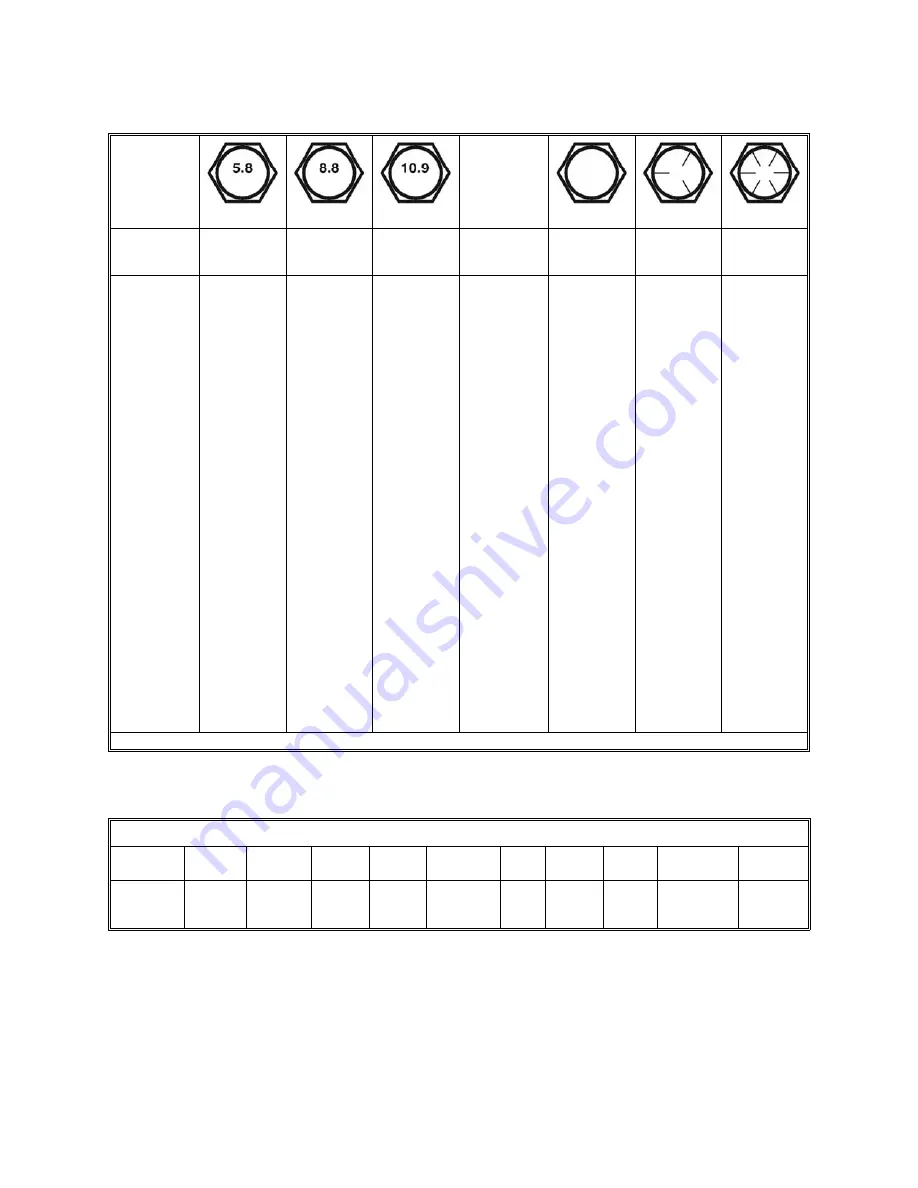
TABLE 1 - TORQUE SPECIFICATIONS
When using lock washers with nuts, increase torque values by 5%.
3557
4823
2194
2974
978
1326
12
1-1/2”
2607
3535
1830
2482
1131
1534
4
M36
3161
4286
1949
2643
869
1179
6
1-1/2”
1659
2250
1180
1600
738
1000
2
M30
2712
3677
1673
2268
746
1011
12
1-3/8”
1499
2033
1047
1420
668
906
3.5
M30
2382
3230
1469
1992
655
888
6
1-3/8”
1176
1594
825
1119
530
719
2
M27
2012
2728
1241
1682
553
750
12
1-1/4”
1103
1496
774
1050
484
656
3
M27
1817
2463
1120
1519
500
677
7
1-1/4”
808
1095
567
769
360
488
2
M24
1445
1958
891
1208
397
539
12
1-1/8”
750
1017
526
714
327
444
3
M24
1288
1746
794
1077
354
480
7
1-1/8”
644
873
452
613
281
381
1.5
M22
995
1348
704
955
273
371
12
1”
595
807
418
567
254
344
2.5
M22
909
1232
644
873
250
339
8
1”
476
646
335
454
212
288
1.5
M20
668
906
473
642
184
249
14
7/8”
437
592
306
415
189
256
2.5
M20
606
822
430
582
167
226
9
7/8”
343
465
241
327
150
203
1.5
M18
420
569
297
403
192
261
16
3/4”
327
443
229
311
145
196
2
M18
376
509
266
361
172
233
10
3/4”
310
421
218
295
133
181
2.5
M18
240
325
170
230
110
149
18
5/8”
236
320
161
218
104
141
1.5
M16
212
287
150
203
97
132
11
5/8”
223
302
152
206
97
131
2
M16
171
232
121
164
79
106
18
9/16”
154
209
105
142
69
94
1.5
M14
154
208
109
147
70
95
12
9/16”
144
195
98
133
62
84
2
M14
120
163
85
115
55
75
20
1/2”
98
133
66
90
44
59
1.25
M12
106
144
75
102
48
66
13
1/2”
94
128
64
87
41
56
1.5
M12
78
106
55
75
36
48
20
7/16”
91
123
62
84
40
54
1.75
M12
70
95
49
67
32
43
14
7/16”
58
78
39
53
26
35
1
M10
49
67
35
47
23
31
24
3/8”
55
75
38
51
24
33
1.25
M10
44
59
31
42
20
27
16
3/8”
52
71
35
48
23
31
1.5
M10
27
37
19
26
13
17
24
5/16”
28
38
19
26
13
17
1
M8
25
33
17
24
11
15
18
5/16”
27
36
18
25
12
16
1.25
M8
14
19
10
13
6
8
28
1/4”
11
15
7
10
4
6
1
M6
12
16
8
11
5
7
20
1/4”
7
9
4
6
3
4
0.8
M5
ft-lb
N.m
ft-lb
N.m
ft-lb
N.m
Thread
inch
tpi
Bolt
size
inch
ft-lb
N.m
ft-lb
N.m
ft-lb
N.m
Thread
mm
Bolt
size
mm
Grade 8
Grade 5
Grade 2
Inch (SAE)
treaded
bolts head
marking
Class 10.9
Class 8.8
Class 5.8
Metric (ISO)
treaded
bolts head
marking
TABLE 2 - C30 ENGINE MOWER - TECHNICAL FEATURES
Briggs &
Stratton
11.5 HP
4 - 8.4”x3.2”
2 BX
1” - 4”
3
14173
2673
460
65”
60”
C30-CE5H
Engine
# Wheels &
size
# Belts
& type
Cutting
height
#
Blades
Blades tip
speed ft/min
Rotor
rpm/min
Weight
lb.
Overall
width
Working
width
Model
Series C30, rear discharge, cat. 1 ball
M
AINTENANCE
29
BEFCO
C
YCLONE
O
PERATOR
’
S
M
ANUAL
Summary of Contents for C30-CE5H
Page 30: ...TABLE 3 OVERALL DIMENSIONS MAINTENANCE 30 BEFCO CYCLONE OPERATOR S MANUAL 91 24 60 65...
Page 40: ...CYCLONE BELTS SPINDLES OPERATOR S MANUAL C30 CE5H PARTS MANUAL 40 BEFCO 0121...
Page 42: ...CYCLONE MOTOR THROTTLE SWITCH OPERATOR S MANUAL C30 CE5H PARTS MANUAL 42 BEFCO 0121...
Page 44: ...CYCLONE BELT SHIELDS WHEEL ARMS OPERATOR S MANUAL C30 CE5H PARTS MANUAL 44 BEFCO 0121...
Page 46: ...CYCLONE DRAWBAR OPERATOR S MANUAL C30 CE5H PARTS MANUAL 46 BEFCO 0121...
Page 48: ...CYCLONE DECALS OPERATOR S MANUAL C30 CE5H PARTS MANUAL 48 BEFCO 0121...