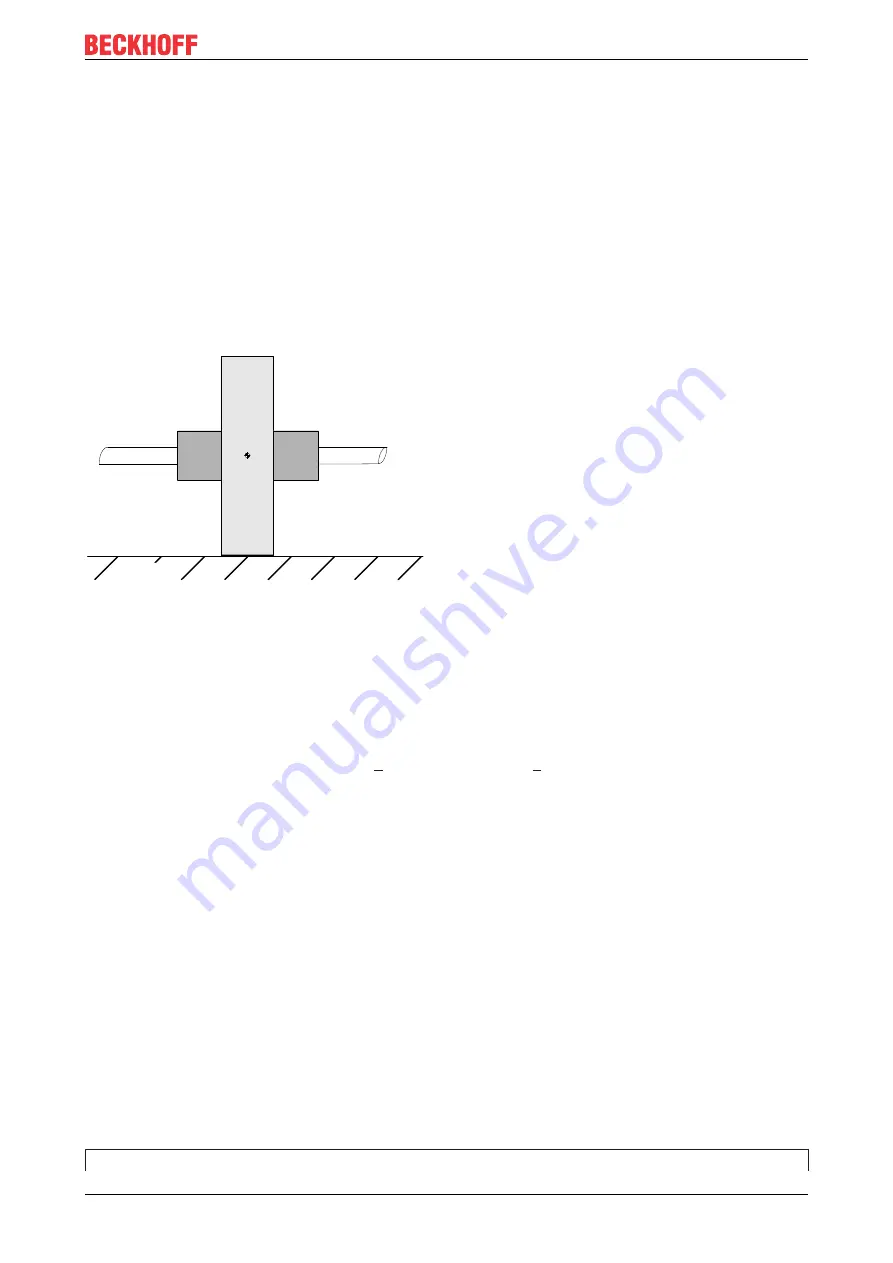
Description
TF5200 | TwinCAT 3 CNC
Online tool compensation
9
Version: 1.02
2
Description
Task
With certain processes such as grinding, the length or the radius of the tool must be continuously corrected
to compensate for wear.
Wear compensation depends on the path covered. In addition, compensation can be influenced by the PLC.
Wear compensation is activated and deactivated from the NC program. The wear constant can be
parameterised both from the NC program and using preset parameters in the tool list P-TOOL-00030.
Rapid traversing blocks have no wear.
It is assumed that the entire width of the lateral surface of the grinding disc is in contact.
Workpiece
Tool
holder
Figure 1: Grinding a contour
Tool type
Wear compensation can only be enabled with tool type 2 (grinding tool). If a different tool type is used, error
message P-ERR-21391 is output.
Processing types
Online wear compensation can be used for 4 processing types and 3 different modes.
1. Radius compensation (only in combination with active TRC) for processing contours in the plane (2.5
D)
2. Length compensation for processing surfaces (surface grinding, 2.5 D)
3. Compensation in tool direction for any orientation (5-axis)
4. Compensation in direction of surface normal (5-axis)
Modes
1. Continuous (dependent on motion path traversed)
2. Discrete (discrete wear compensation via PLC)
3. Automatic, combination of discrete and continuous
Discrete additive wear values which are assigned by the PLC are adjusted over several cycles.
2.1
Programming
The following NC command is provided to program online tool compensation in the NC program.
Parametrisation can be programmed in advance or in combination with #OTC ON:
#OTC ON
|
OFF
[
[
RADIUS
|
LENGTH
|
TOOL_DIR
|
SURF_NORM_DIR
DISC
|
CONT
|
AUTO