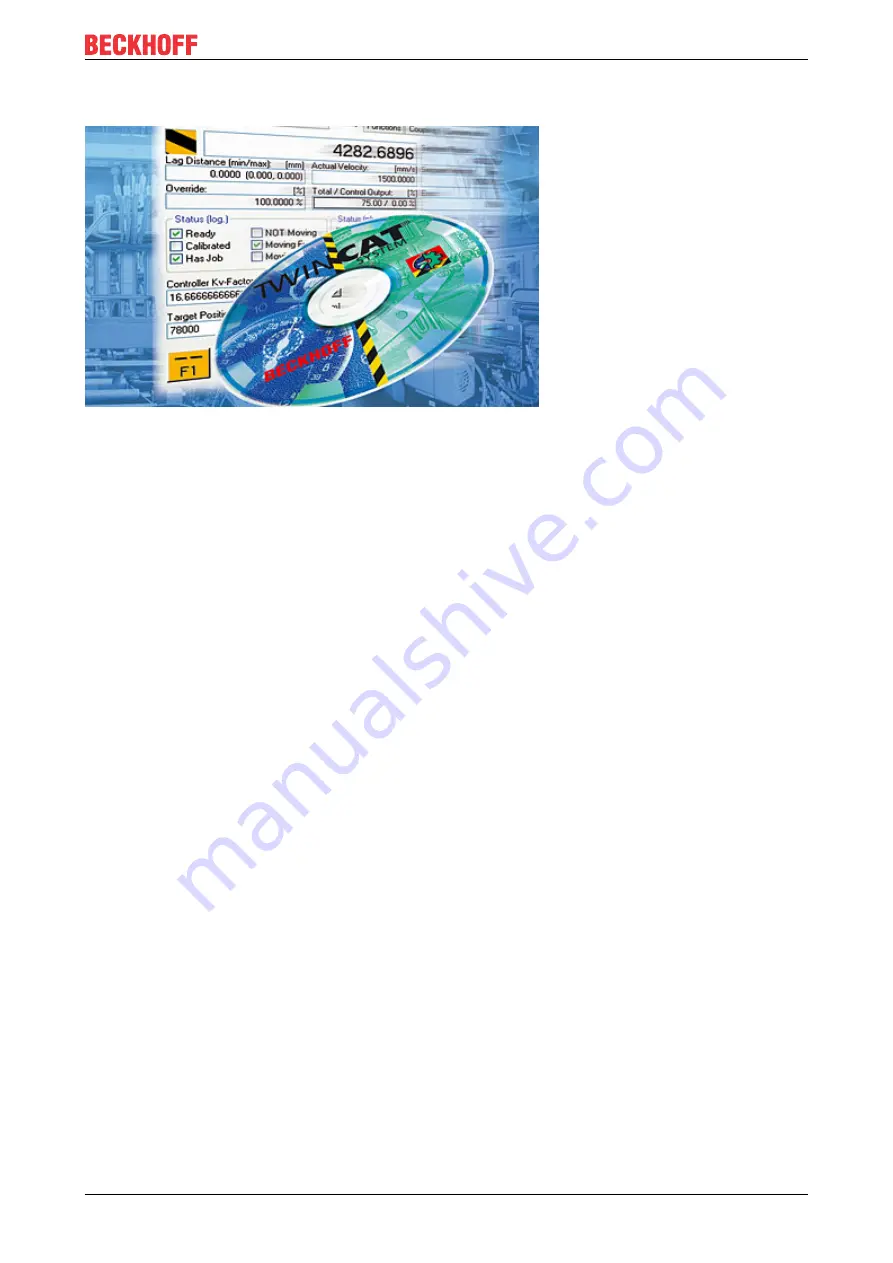
TwinCAT
KL2xxx and KS2xxx
35
Version: 3.0.0
4
TwinCAT
PLC and Motion Control on the PC
TwinCAT -
T
he
Win
dows
C
ontrol and
A
utomation
T
echnology
The TwinCAT automation software converts any compatible PC into a real-time controller with multi-PLC, NC
axis control, programming environment and operating station. TwinCAT replaces conventional PLC and NC
controllers as well as operating devices:
• open, compatible PC hardware
• Embedding of IEC 61131-3 software PLC, software NC and software CNC in Windows NT/2000/XP,
NT/XP Embedded, CE
• Programming and runtime systems optionally together on one PC or separated
• Connection to all common fieldbus systems
• PC interfaces are supported
• Data communication with user interfaces and other programs by means of open Microsoft standards
(OPC, OCX, DLL, etc.)
TwinCAT architecture
TwinCAT consists of runtime systems for real-time execution of control programs and development
environments for programming, diagnosis and configuration. Any Windows programs, for instance
visualization programs or Office programs, can access TwinCAT data via Microsoft interfaces, or can
execute commands.
A practically oriented software solution
TwinCAT offers a precise time-base in which programs are executed with the highest deterministic features,
independently of other processor tasks. The real-time load on a PC is set with TwinCAT: This achieves a
defined operating behavior. TwinCAT displays the system load for running programs. A loading threshold
can be set, in order to assure a defined computing capacity for the operating programs and for Windows
NT/2000/XP. If this threshold is exceeded, a system message is generated.
TwinCAT supports system diagnosis
The general use of hardware and software from the open PC world requires some checking: Unsuitable
components can upset the PC system. Beckhoff integrates a handy display of the real-time jitter in order to
provide administrators with a simple means of evaluating hardware and software. A system message during
operation can draw attention to error states.