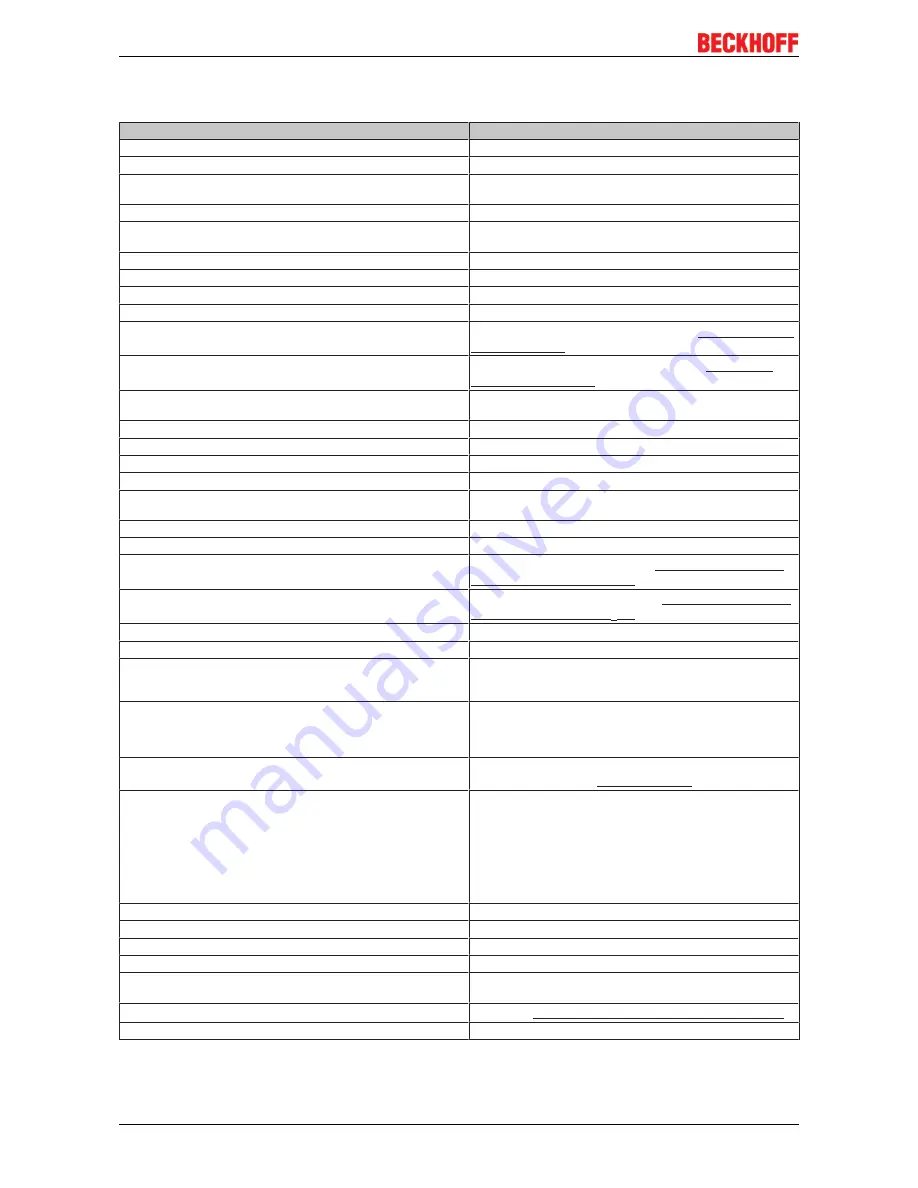
Product description
EL1904
16
Version: 2.1.1
3.3
Technical data
Product designation
EL1904
Number of inputs
4
Status display
4 (one green LED per input)
Reaction time (read input/write to E-bus)
typically: 4 ms,
maximum: see error reaction time
Error reaction time
≤ watchdog time
Cable length between sensor and terminal
unshielded max. 100 m (0.75 or 1 mm²)
shielded max. 100 m (0.75 or 1 mm²)
Output current of the clock outputs
typically 10 mA, max. 15 mA
Input process image
6 bytes
Output process image
6 bytes
EL1904 supply voltage (PELV)
24 V
DC
(–15% / +20%)
Signal voltage "0" inputs
-3 V to 5 V (EN 61131-2, type 3) see chapter
Characteristic curve
of the inputs [
}
17]
Signal voltage "1" inputs
11 V to 30 V (EN 61131-2, type 3) see chapter
Characteristic
curve of the inputs [
}
17]
Current consumption of the modular electronics at 24 V (without cur-
rent consumption of sensors)
4 channels occupied: typically 12 mA
0 channels occupied: typically 1.4 mA
Current consumption via E-bus
4 channels occupied: approx. 200 mA
Power dissipation of the terminal
typically 1 W
Electrical isolation (between the channels)
no
Electrical isolation (between the channels and the E-bus)
yes
Insulation voltage (between the channels and the E-bus, under com-
mon operating conditions)
insulation tested with 500 V
DC
Dimensions (W x H x D)
12mm x 100mm x 68mm
Weight
approx. 50 g
Permissible ambient temperature (operation)
up to SW 05
0 °C to +55 °C (see notes in chapter
Example configuration for
temperature measurement [
}
21]
)
Permissible ambient temperature (operation)
from SW 06 (week 02/2014)
-25°C to +55 °C (see notes in chapter
Example configuration for
temperature measurement [
}
21]
)
Permissible ambient temperature (transport/storage)
-40°C to +70°C
Permissible air humidity
5% to 95%, non-condensing
Permissible air pressure (operation/storage/transport)
750 hPa to 1100 hPa
(this corresponds to a height of approx. -690 m to 2450 m over
sea level assuming an international standard atmosphere)
Climate category according to EN 60721-3-3
3K3
(the deviation from 3K3 is possible only with optimal environmen-
tal conditions and also applies only to the technical data which
are specified differently in this documentation)
Permissible level of contamination
according to EN 60664-1
level of contamination 2
(comply with the chapter
Maintenance [
}
41]
)
Impermissible operating conditions
TwinSAFE terminals must not be used under the following oper-
ating conditions:
• under the influence of ionizing radiation (that exceeds the
level of the natural environmental radiation)
• in corrosive environments
• in an environment that leads to unacceptable soiling of
the Bus Terminal
EMC immunity/emission
conforms to EN 61000-6-2 / EN 61000-6-4
Vibration/shock resistance
conforms to EN 60068-2-6 / EN 60068-2-27
Shocks
15 g with pulse duration 11 ms in all three axes
Protection class
IP20
Permitted operating environment
In the control cabinet or terminal box, with minimum protection
class IP54 according to IEC 60529
Permissible installation position
see chapter
Installation position and minimum distances [
}
20]
Approvals
CE, cULus, ATEX, TÜV SÜD
Summary of Contents for EL1904
Page 2: ......
Page 44: ...Appendix EL1904 44 Version 2 1 1 5 2 Certificates...