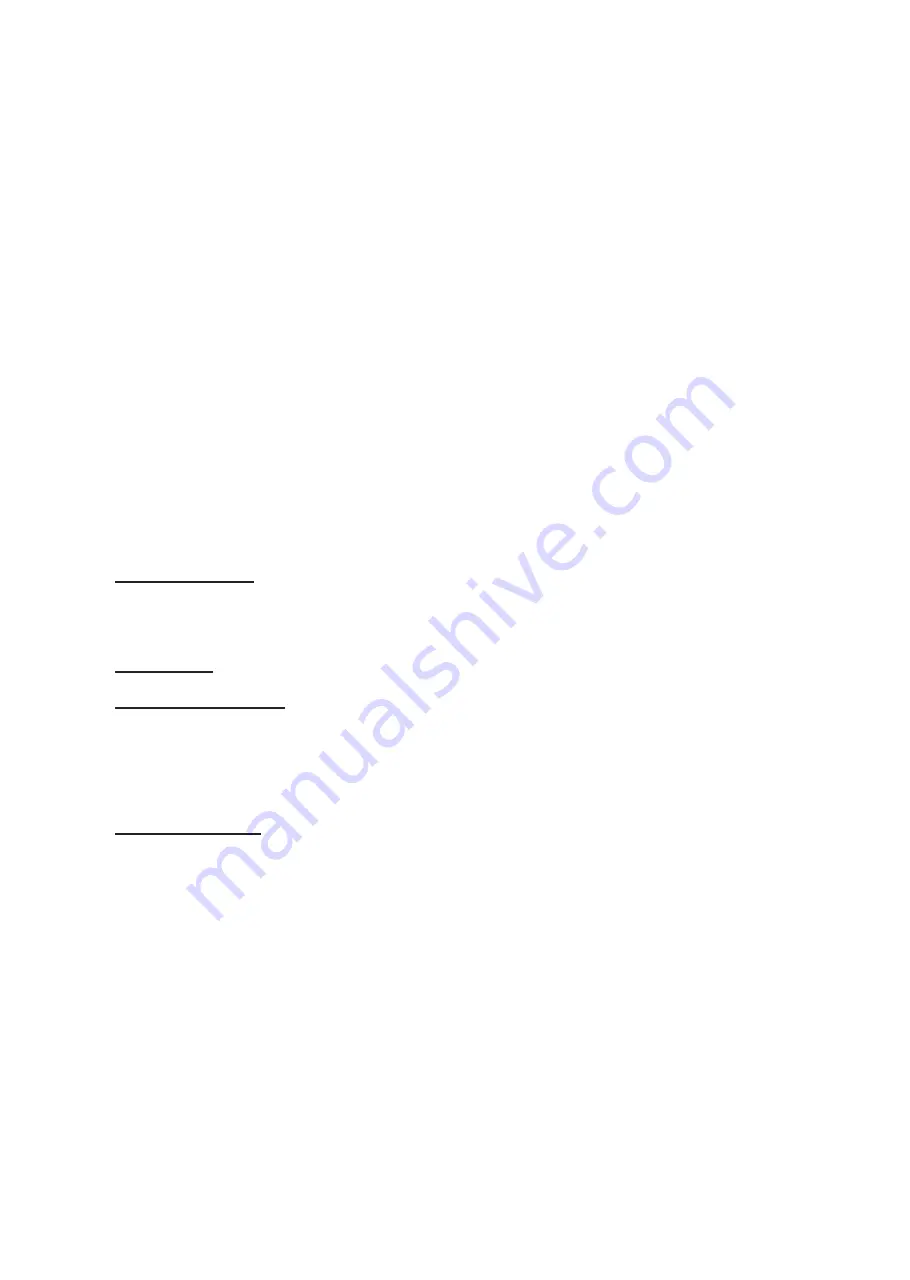
28100031
100 08/2017
Page: 8
Driving motor:
Directly behind the flanged connection to the pump housing, the motor housing has openings for checking
the direction of rotation of the motor. The latter has to correspond to the direction of the arrow affixed to the
outside of the motor cabinet.
Should this not be the case, the direction of rotation can only be changed by exchanging two phases at the
outlet of the frequency inverter. The clamps are marked as follows:
U 96, V 97 W 98
Starting up and shutting down the unit
Initial Operation of the unit
To supply the complete unit with power, the following necessary steps have to be taken; before the main
switch can be turned on
I.
Turn on all automatic motor protection switches
II.
If not already done, turn
main switch
as far as it will go to the left, then to the right.
Starting up the vacuum pump or the compressor
After the complete installation has been connected as described in point 3 of the instructions for starting up the
unit, the control or regulating program will be started.
•
Initialising the unit:
After two or three seconds, the message
“Initialising…”
appears in the first line of
the display. At this point, you will have the opportunity to check, adjust or correct the edge conditions of
the intended use of the unit. The adjustable edge conditions as well as their values and meaning are listed
the table
“Adjustable parameters”
in
section 2.6 (Parameter overview)
. If the entire unit was disconnected,
the point Initialisation will come up every time the unit is switched on.
•
Confirmation:
If all pre-settings have been made in accordance with the table,
press the [START] key
once
to confirm your settings. The message
“Restart Y/N”
appears in the first line of the display.
•
Start/Stop without SPS:
If parameter 19-43 was set to “Without SPS”, pressing the
[START]
key once
more will start the unit with the set speed of rotation along the pre-set slope. First, the oil pump will start
and the highlighted text
“Starting screw pump…”
will be displayed. As soon as the minimal oil pressure
is reached, the fans will turn on as well and the pressure/vacuum generator will start up. The unit can be
stopped pressing the
[STOP]
key. In this case, the message
“Manual stop wait…”
appears in the display.
The unit can be restarted as soon as the message
“Restart Y/N”
is displayed. If there is no restart of the
unit the fans will switch off after another follow-up running time of 5 minutes.
•
Start/Stop with SPS:
The start cannot be commenced with set PLC until a release signal that is sent by
the PLC is available at the terminal strip X6.3 and X6.4 at the frequency converter. Respectively, discontinuing the signal
will cause the unit to stop, displaying the message
“SPS Stop wait…”
. In this case also, the SPS can only restart after the oil
pump has been shut down and the message
“Restart Y/N”
appears in the display.
Note: A unit which has started automatically can be shut down during operation by pressing the
[STOP]
key. In this case also, the message
“Manual stop wait…”
will be displayed. However, switching back the
unit to automatic mode now requires pressing the
[START]
key. If the SPS release signal is received at^
that time, the unit will restart.