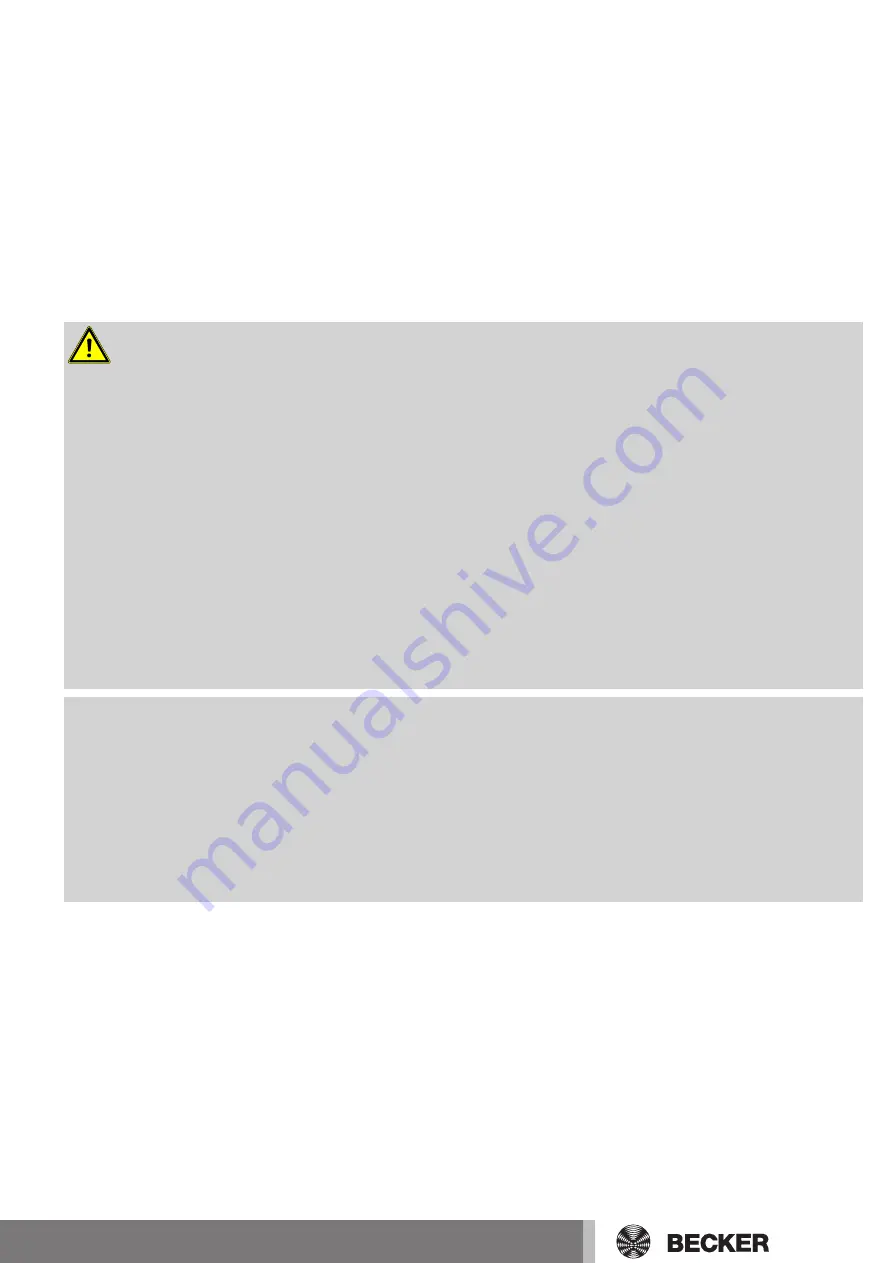
•
Hazardous moving parts of the drive must be installed at a height of over 2.5 m above floor level or any
other surface from which the drive can be accessed.
•
To ensure safe operation of the system after commissioning, the limit positions must be correctly set/
programmed in.
•
Drives with a H05VV-F connecting cable may only be used indoors.
•
Drives with a H05RR-F, S05RN-F or 05RN-F connecting cable may be used both indoors and outdoors.
•
To connect the drive to the driven part, solely mechanical accessory components made by the drive
manufacturer from the current product catalogue may be used. The components must be installed in
accordance with the manufacturer's instructions.
•
If the drive is used for shading solutions in a specially marked area (e.g., escape routes, hazard zones,
safety areas), compliance with all applicable regulations and standards must be ensured.
Caution
Safety instructions for avoiding serious injuries.
•
When electrical or electronic equipment and units are operated, certain components,
e.g., the power supply unit, are live. Physical injuries or damage to property can result in
the event of unauthorised interventions or failure to heed warnings.
•
Be careful when touching the tubular drive, as it heats up during operation for technical
reasons.
•
Before installation, shut down all lines and control devices that are not essential for op-
eration.
•
Crushing or shearing points must be avoided or protected.
•
When installing the drive, all-pole disconnection from the mains with a contact gap of at
least 3 mm per pole must be provided (EN 60335).
•
If the mains connecting cable is damaged, it may only be replaced by the manufacturer.
If the drive has a plug-in connecting cable, it must be replaced with the same type of
mains connecting cable, which is available from the drive manufacturer.
Attention
Safety instructions for avoiding property damage.
•
Ensure that there is adequate clearance between moving parts and adjacent objects.
•
The drive must not be carried by the mains connecting cable.
•
All latching connections and fastening screws on the brackets must be checked to en-
sure that they are secure.
•
Ensure that nothing rubs against the tubular drive, such as shading solution attach-
ments, screws, etc.
5