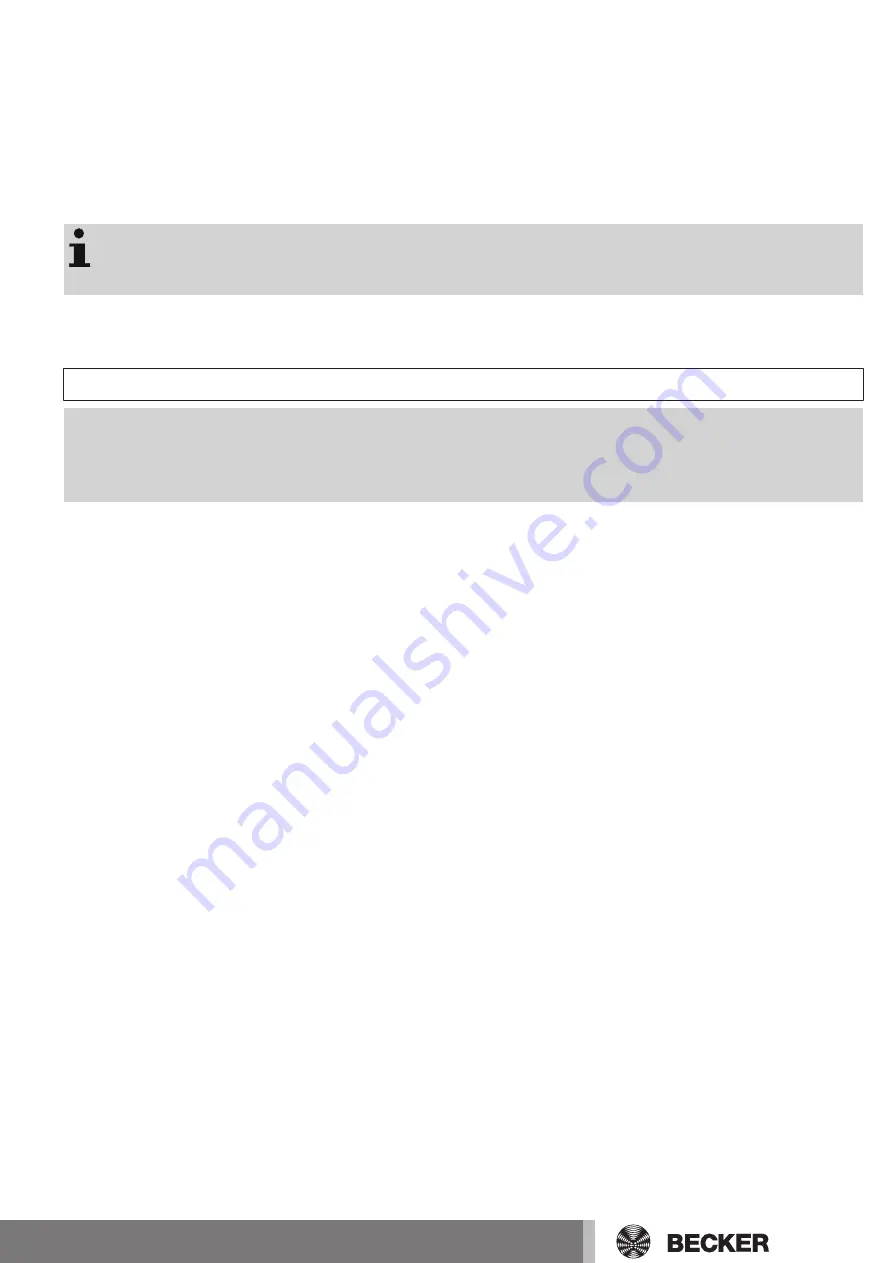
3.
Rotate the black cam S6 "CLOSE" on its shaft until the precision set screw is within easy reach. Now use the precision set
screw (slotted) to manually set the cam in such a way that it activates the switch. Move the door slightly up and down again un-
til the end switch stops the door. Fine tune the setting as necessary.
4.
Now move the door to just before the upper limit position.
5.
Now set the grey cam S5 "OPEN" in the same way as described in point 3.
6.
Now set the yellow safety cams S1F "UP" and S2F "DOWN" to lag both operational limit switches S5 "OPEN" and S6 "CLOSE".
7.
The two functional cams S7 (orange) and S8 (green) can be set accordingly if required.
8.
The limit switches are now set. Carry out a test run to check the set limit positions.
If the orange functional cam S7 is used as a pre-limit switch for functional switch-off of the
safety edge of the door, then it must switch a maximum of 5 cm above the floor; EN12453
and EN12445.
Replace the housing cover on the limit switching system. Make sure that the seal and the lining groove are clean and that the cover
is properly positioned. Tighten the screws carefully.
Maintenance
Attention
The door system must be regularly checked by an expert to ensure that it is in safe working
order. The door manufacturer stipulates the frequency of maintenance and checks ac-
cording to national regulations and the frequency of use.
Counterweight (applies to sectional doors with spring compensation or a counterweight):
The counterweight/spring tension must be checked. The sectional door should be counterweighted in every position. Note the
door's operating instructions.
The following checks must be performed on the drive:
1. Fastenings:
All fastening screws, including the screws to secure the torque bracket, must be checked to ensure they are in good condition and
fastened securely.
2nd Safety limit switches:
The functionality and switch-off point of the safety limit switches S1F, S2F and S3F must be checked. Follow the relevant assembly
and operating instructions for the door control unit. The safety limit switches must be checked for continuity as per the connection
diagram.
Re S1F / OPEN (applies to cam-operated limit switching)
Open to the upper limit position. Using the emergency manual operation function, keep opening up to the point where no damage
occurs. The safety switch S1F must be checked as per the connection diagram. There must be no continuity.
Re S2F / CLOSE (applies to cam-operated limit switching)
Close to the lower limit position. Using the emergency manual operation function continue closing until the load-bearing medium
(e. g., cables or chains) for suspending takes the complete weight of the door sections. It must be ensured that the cables do not
fall from the cable drum. The safety switch S2F must be checked as per the connection diagram. There must be no continuity.
Re S3F (applies to HK and LK drives)
Before inspecting the safety switch S3F, the door system must be disconnected from the mains.
Insert the crank handle (HK) in the motor shaft and turn through at least one revolution and hold the position or pull the light chain
(LK) and keep it taut.
The safety switch S3F must be checked as per the connection diagram. There must be no continuity.
3. Gears:
The gears are lubricated for life and maintenance-free.
4. Toothed belt
1.
Check that the toothed belt (1) has sufficient preliminary tension.
2.
Carry out a visual check of the toothed belt (1) along the complete travel distance of the door. The toothed belt (1) must show
no signs of wear.
13
Summary of Contents for a100/25
Page 15: ...Declaration of incorporation 15 ...
Page 16: ......