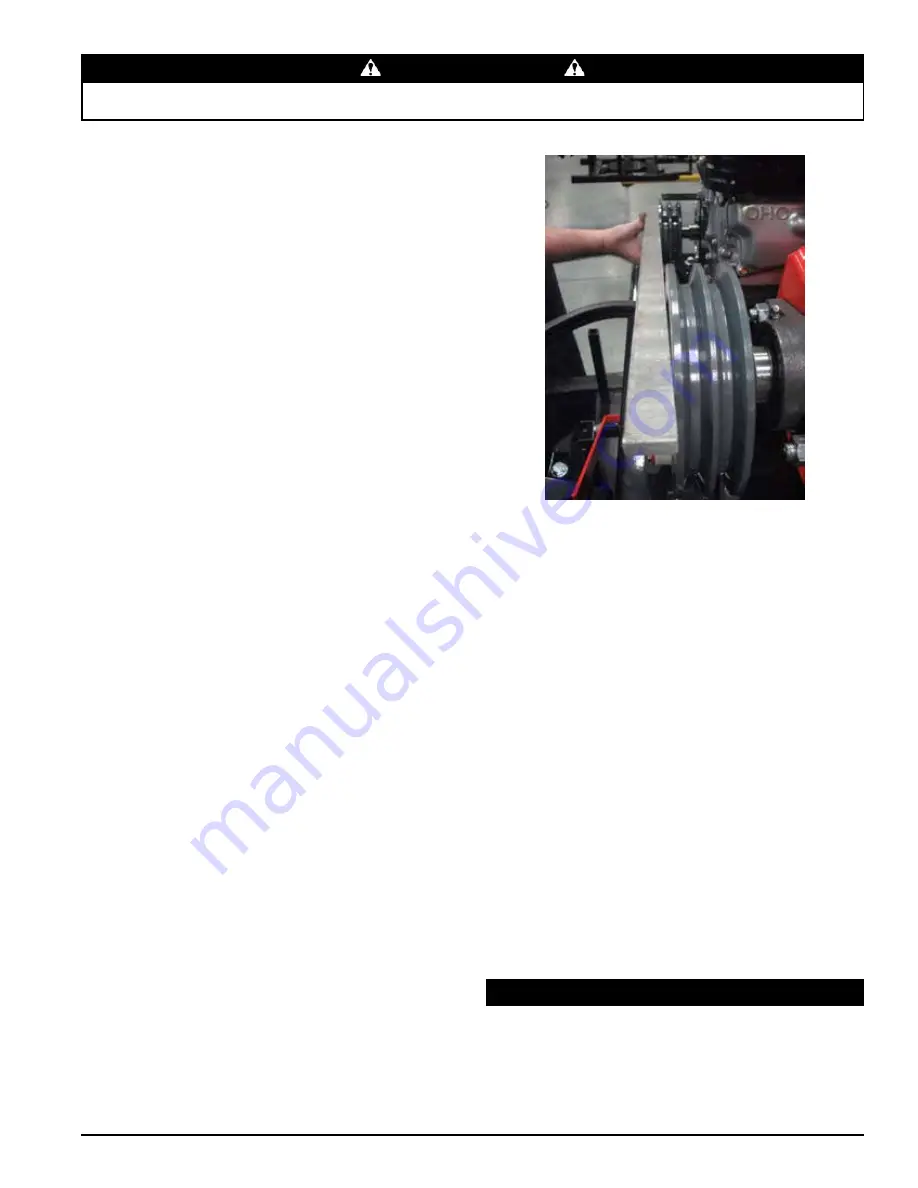
21
4 INCH CHIPPER
ENGLISH
SERVICE & MAINTENANCE
WARNING
BEFORE INSPECTING OR SERVICING ANY PART OF THIS MACHINE, SHUT OFF POWER SOURCE, DISCONNECT SPARK PLUG
WIRE FROM SPARK PLUG AND MAKE SURE ALL MOVING PARTS HAVE COME TO A COMPLETE STOP.
5.11.2 INSTALLING
1. Replace bearing and center in the bearing opening.
2. Tighten the two 1/2 x 1-1/2" carriage bolts and 1/2"
centerlock nuts securing the rear bearing to the
chipper housing. Torque to 75 ft-lb.
3. Slide the rotor back into the chipper housing.
4. Slide a snap ring onto the rotor shaft, making sure
that it is seated properly on the rotor.
5. Slide the bearing shim, front bearing and second
snap ring on the rotor, making sure that the second
snap ring is seated properly on the rotor.
6. Reinstall the rotor cover using seven 5/16" nuts and
washers.
7. Next, the rotor must be centered vertically and
horizontally inside the chipper housing. To do this,
measure the distance from the rotor to the inside
edge of the chipper housing at four points around the
rotor. Adjust the rotor until all four points are an equal
distance from the edge of the chipper housing or use
Alignment Tool. Finish tightening the 1/2 x 3/4" bolts
and nuts securing the front bearing to the chipper
housing to a torque of 75 ft-lbs.
8. Tighten the two set screws located on both the front
and rear bearings, securing the bearings to the rotor
shaft. Torque set screws to 160 in-lbs.
9. Slide the bushing and sheave onto the shaft.
10. Tighten the two 1/2 x 3/4" bolts and nuts securing the
front bearing to the chipper housing. Torque to 75 ft-
lbs.
11. Using a straight edge, align the sheave with the other
pulley to ±1/16". Keep in mind that the sheave will
shift approximately 1/16 to 1/8" away from you once it
is tightened (see Figure 5.11).
12. Insure the pulley drive key is completely seated under
the pulley and tighten the set screw.
13. Remove the three screws in the sheave and put them
in the other three threaded holes on the sheave.
Tighten the screws equally until the bushing tightens.
Torque to 108 inch-lbs.
14. Recheck pulley alignment. Pulley faces should line
up. If not, readjust and repeat alignment check (see
Figure 5.11).
15. Replace the belt.
16.
Adjust the drive belt so that the belt deflection is 7/16"
when a 20 lb. load is placed against the belt (see
Figure 5.9). To do this, adjust both 5/16" adjustment
bolts equally.
17. If the bolts and nuts between the engine plate and the
trailer cannot be adjusted any further, and the tension
needs further adjustment, tighten the eyebolt until the
appropriate deflection is achieved.
18.
Once correct belt deflection has been achieved,
tighten both 5/16" flange nuts to maintain it.
19. Tighten the four carriage bolts attaching the engine
plate to the trailer.
20. Reinstall the belt guide.
21. The chipper engagement lever should be in the
START position (up).
22. Reinstall the idler assembly.
23. Attach the chipper chute to the rotor cover.
24. Attach the discharge cap.
25. Replace the belt guards.
Figure 5.11, Checking Pulley Alignment
5.12 CHANGE OIL
Check the oil level before each use. Change oil as directed
in the engine owner's manual.