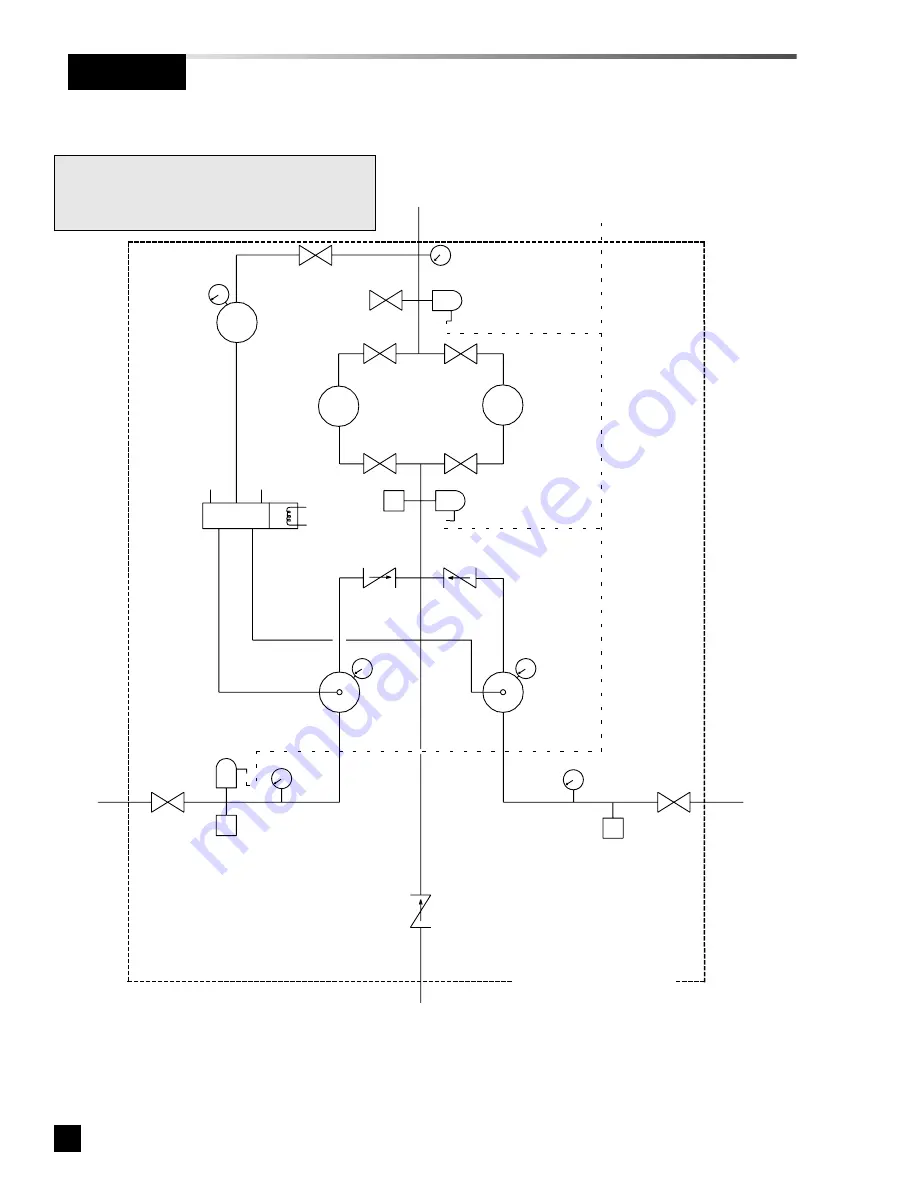
34
Part No. 6-847703-00 Rev. C00
Operation
Figure 22
Manifold
Outlet
Vent Valve
Line Relief Valve
Valve
Line Pressure Gauge
Service Valve
Line
Regulator
Valve
Valve
Valve
Line
Regulator
Intermediate Relief Valve
Solenoid
Valve
Check
Valve
Check
Valve
Bank
Regulator
Bank
Regulator
Inlet
Relief Valve
Bank
Gauge
Bank
Gauge
Check
Valve
*
Dome
Regulator
Relief Valve
Outlet
Right Bank
Inlet
Left Bank
Inlet
From High-Pressure
Reserve Header (Figure 23)
Manifold Control Panel
* NOTE:
Dome regulators not used on oxygen
manifolds design for 55 PSI delivery pressure.
Secondary Supply
Pressure Switch
Secondary Supply
Pressure Switch
Master
Valve
Master
Valve
Reserve In Use
Pressure Switch