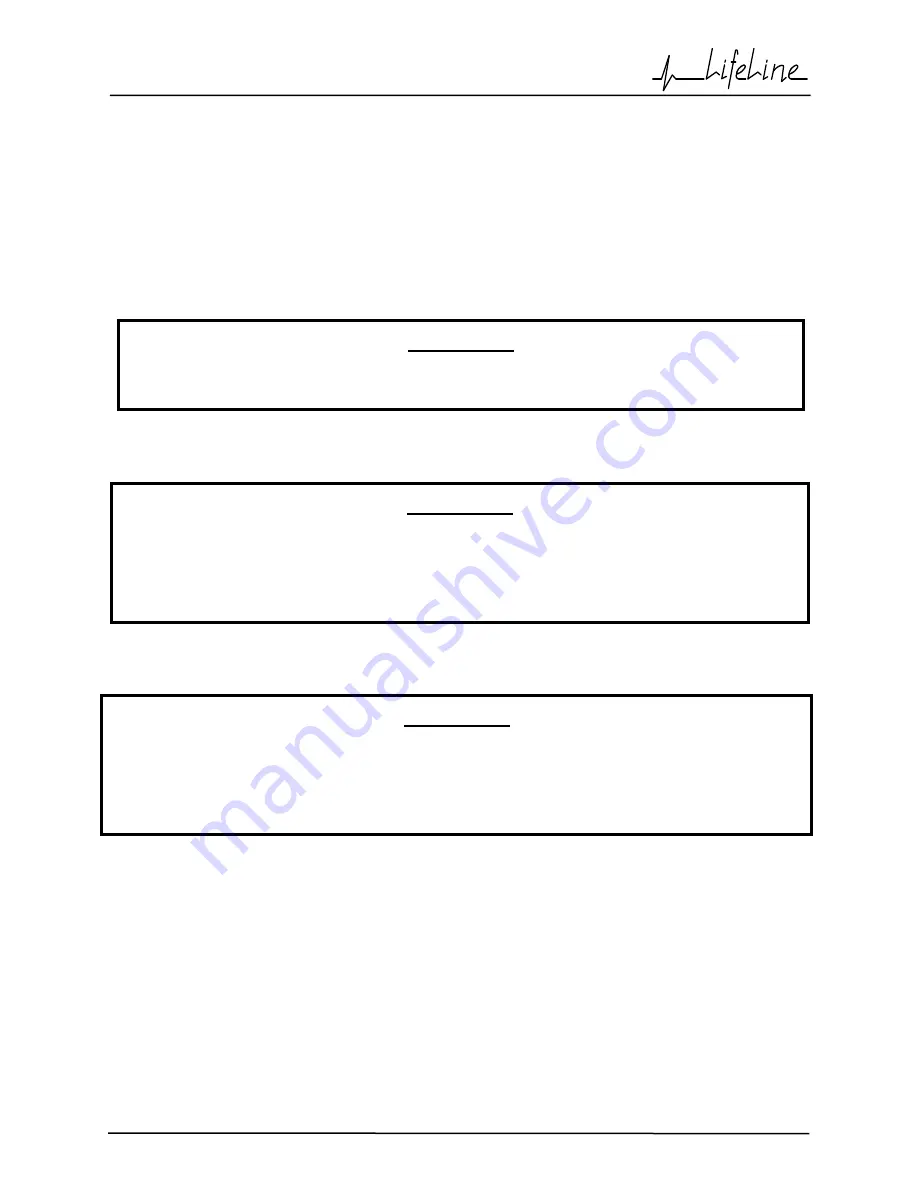
"Camel" Liquid Ring Medical Vacuum
Medical Systems
A-7
8.
Inspect all pump control components (valves, gauges, etc.) to ensure that they have been installed in
accordance with the
BeaconMedæs
installation drawing(s). Make certain that these components are
correctly oriented in the piping scheme in order to achieve the proper direction of flow and functional
operation.
9.
Inspect the pump inlet to ensure that the inlet screen and clean out connections have been properly
made and are free of tools, equipment, and debris.
10.
Make certain that the liquid discharge connection is free of obstructions.
11.
Remove the motor fan guard and rotate the motor fan in the specified direction of rotation as marked
on the pump body. Because of the direct-drive configuration, the pump shaft will also turn.
THE
PUMP SHAFT MUST ROTATE FREELY
. If the pump shaft is bound and can not be freed by
rotating it manually, contact your
BeaconMedæs
representative for assistance.
12.
With the main supply valves open and the pump primed, bump the drive motor in order to check for
proper direction of shaft rotation.
A.5.5 Starting and Stopping the Pump
A.5.5.1 Starting
Once the preliminary inspection and pre-operational check procedures have been completed, start the pump and
check pump operation as follows:
1.
Check the pump and system for adequate prime and then turn on all main water supply sources to the pump
and heat exchanger (if used).
2.
Open the inlet valve to the pump.
3.
Start the pump motor.
4.
Open and adjust the service liquid shut off valve. Determine the correct liquid flow rate by means of a flow
gauge or by measuring the overflow at the separator tank.
5.
Lock the adjusting valve. If a solenoid valve is used instead of a normal valve, the motor starting up should
control this. The use of a solenoid valve eliminates the possibility of starting the pump flooded. Therefore,
it should open when the motor is energized.
6.
Check that the motor power consumption is in accordance with the nameplate data by means of an
ammeter
7.
Check that the pump operation is free from any excessive vibration and noise.
WARNING
Do not attempt to free a pump shaft from a binding or bound condition
by applying power to the drive motor. Severe damage may result.
WARNING
Never operate the pump without adequate prime and service liquid flow.
High service liquid supply pressures do not necessarily indicate that the
flow is adequate. Check for flow from vacuum pump discharge or water
trap silencer.
WARNING
If the pump is to be checked in a system, notify the appropriate hospital
personnel before placing a pump on line, particularly when placing the
pump online for the first time. Starting up a system unexpectedly may cause
personnel injury.