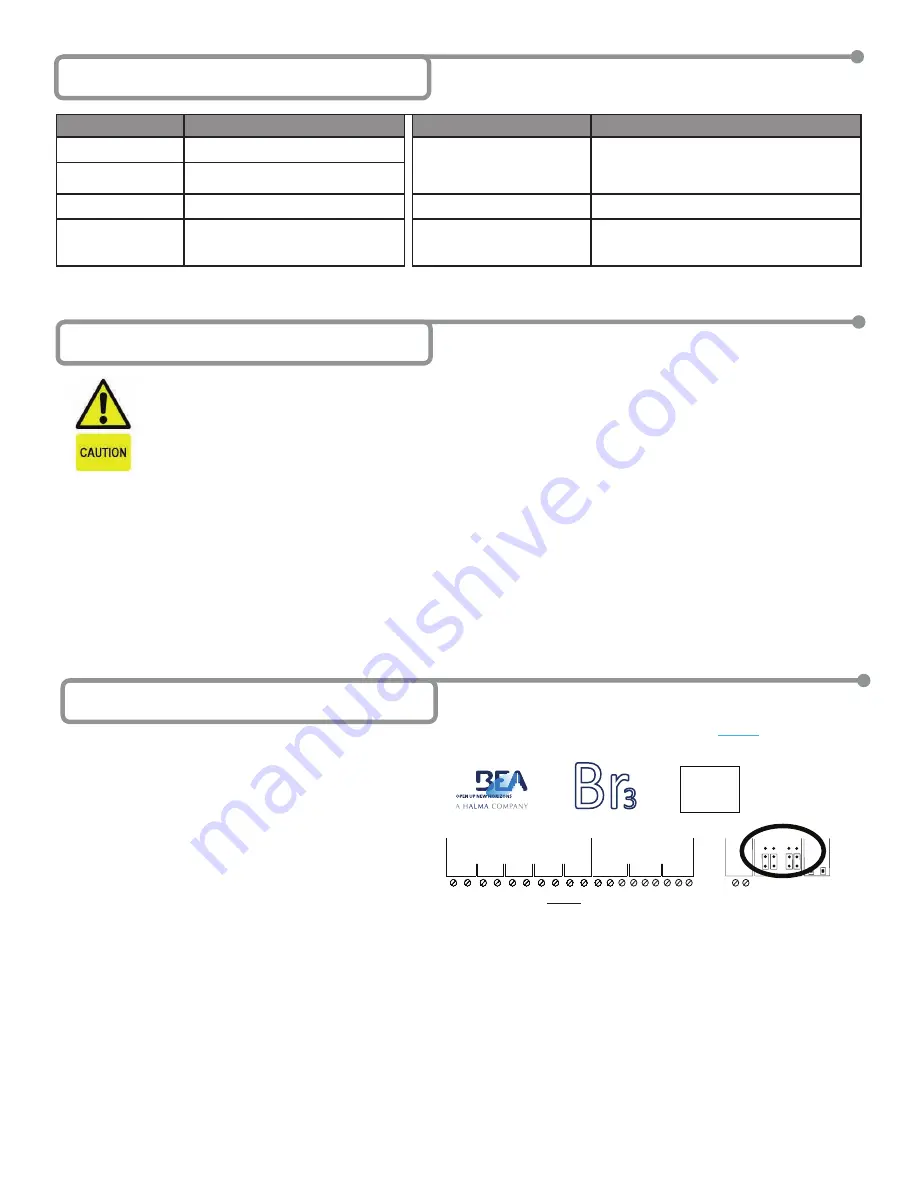
Page 2 of 15
75.5501.02 EN 20091102 (75.5500)
2 Specifications
3 Precautions
Shut off all power before attempting any wiring procedures.
Maintain a clean & safe environment when working in public areas.
Constantly be aware of pedestrian traffic around the door area.
Always stop pedestrian traffic through the doorway when performing tests that may result in unexpected reactions by the door.
ESD: Circuit boards are vulnerable to damage by electrostatic discharge. Before handling ensure you dissipate your body’s
charge.
Always check placement of components before powering up so that moving parts will not catch any wires or cause damage to
equipment.
Ensure compliance with all applicable safety standards (i.e. ANSI A156.10 / 19) upon completion of installation.
When preparing to wire multiple devices together for a ‘system’ configuration, it is best to ensure the correct operation of each
device independently before starting to help reduce troubleshooting time later, in the event of a discrepancy.
When applying equipment on a new installation, utilizing new electrical supply circuits, always ensure that correct line voltage
exists and is stable. Remember to shut the power back off once this is checked, before performing any wiring to the system.
DO NOT attempt any internal repair of the sensor. All repairs and/or component replacements must be performed by BEA, Inc.
Unauthorized disassembly or repair:
1. May jeopardize personal safety and may expose one to the risk of electrical shock.
2. May adversely affect the safe and reliable performance of the product resulting in a voided warranty.
*
NOTE: If the Br3 is powered with AC voltage and is using the ‘WET” output to convert to DC, and the current draw of the device is greater
than .9 amps the upper temperature range is +130°F (54°C).
DESCRIPTION
SPECIFICATION
DESCRIPTION
SPECIFICATION
Supply Voltage
12 to 24 VAC/VDC: +/- 10%
Contact Rating ‘DRY’ - Relay 1
- Relay 2
- Relay 3
Contact Rating ‘WET’ - Relay 1
3 A at 24 VAC; 3 A at 30 VDC
3 A at 24 VAC; 3 A at 30 VDC
1 A at 24 VAC; 1 A at 30 VDC
1 A
Current Consumption 30 to 130 mA (‘DRY’ Output)
Temperature Range
-15°F (-26°C) to +150°F (65°C)
*
Dimensions
5.2” (133mm) W x 2.2” (55mm) D x 1” (25mm) H
Input Specification
Inputs 1 to 4: ‘DRY’ Contact
‘WET’ Input:
5 VAC/VDC to 24 VAC/VDC: +/- 10%
Housing Material
ABS – Grey Translucent
4 Jumper Settings
1.
The Br3 contains two (2) sets of jumpers. Both sets deal
with configuring Relay 1 options:
Jumper set 1 configures whether or not to output AC or
DC voltage if the ‘WET’ output is selected. Jumper set 2
configures whether or not the Relay 1 output is ‘WET’ or
‘DRY’. The ‘WET’ voltage output means that the module
will supply a voltage output of up to 1 Amp on Relay
1 to power electric strikes and magnetic locks without
the need for an external power supply. This feature can
greatly simplify the installation (as long as the power
supply powering the Br3 is rated for 1 Amp).
The ‘WET’ output can also be set using jumpers to output
DC if the Br3 is supplied with AC, otherwise it will just
pass the AC voltage that is supplied. Similarly if powered
by DC, the ‘WET’ output will only output DC.
• To set Relay 1 to output DC (if ‘WET’) move
both
shunts (2) on Jumper Set 1, to the two (2) lower pins.
• To set Relay 1 to output AC (if ‘WET’ and powered with AC) move
both
shunts (2) on Jumper Set 1, to the two (2) upper pins.
• To set Relay 1 to output ‘DRY’ (Jumper Set 1 becomes unused), move
both
shunts (2) on Jumper Set 2, to the two (2) lower pins.
• To set Relay 1 to output ‘WET’, move
both
shunts (2) on Jumper Set 2, to the two (2) upper pins.
G
N
D
IN
-1
G
N
D
IN
-2
G
N
D
IN
-3
G
N
D
IN
-4
1
2
3
4
WET
WET
WET
N
C
N
O
C
O
M
N
C
N
O
C
O
M
12
-2
4V
AC
/D
C
RELAYS
1
2
POWER
RELAY 1
IN
C
R
.
PARAM
SETUP
D
C
AC
D
R
Y
W
ET
INPUTS
00
N
C
N
O
C
O
M
3
Br
3
CAUTION: RELAY 1 WET
OUTPUT OPTION
IS ACTIVE FOR
ALL FUNCTIONS.
NOTE: Default jumper settings make Relay 1 output
‘DRY’ only. All four jumpers set to lower pins.