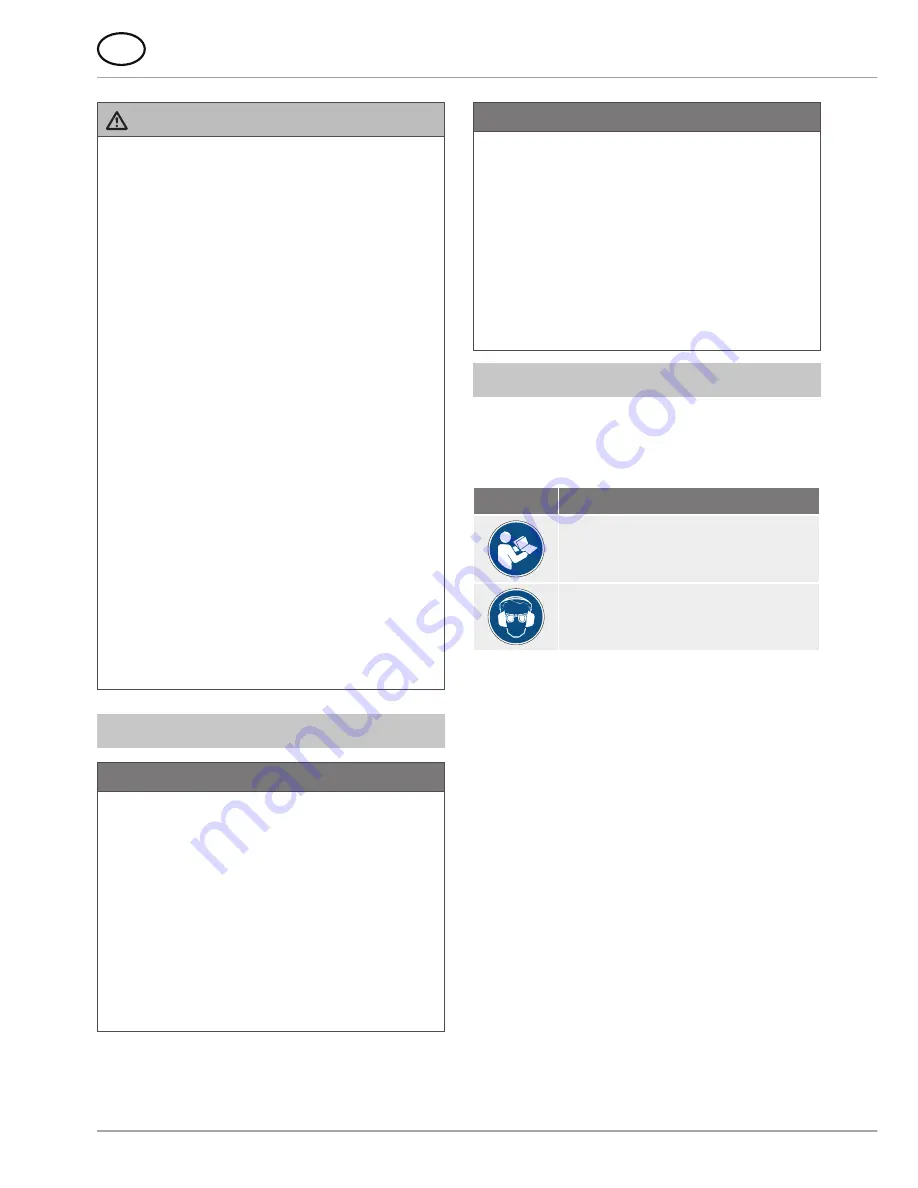
7
Safety
AirMAB 5000
GB
WARNING
Do not put your hand into the ma-
►
chine while it is in operation. Remove
swarf only when the machine is at
a standstill. Wear protective gloves
when removing swarf.
When working on scaffolding, the op-
►
erator must be secured with a safety
belt as the machine can oscillate
dangerously in the event of failure of
the compressed air supply.
Check for secure clamping of the
►
magnets on the substrate before
every use (see
Preparation
section).
Secure the machine with the safety
►
chain (D) supplied when working in
an inclined or vertical position and
during overhead work. The machine
could fall down when the magnet is
released.
Check that the tool is tightened
►
securely before using (see
Inserting
the tool
section).
Do not allow the compressed air line
►
to hang over edges (trip wire effect).
Preventing damage
CAUTION
Potential damage to property if the
machine is improperly used!
Observe the following instructions to
avoid property to damage:
Only use the prescribed air quality, air
►
quantity and operating pressures for
compressed air supply (see section
Preparing).
Always carry the machine by the
►
handle.
CAUTION
Do not crush the compressed air line.
►
Do not expose the compressed air
►
line to heat or chemical liquids.
Do not pull the compressed air line
►
across sharp edges or hot surfaces.
Lay the compressed air line in such
►
a way that it cannot be caught and
wound up in the rotating part of the
machine.
Safety appliances
Symbols on the machine
The symbols on the machine have the fol-
lowing meaning:
Symbol
Meaning
Read the operating instructions
before beginning work!
Wear protective goggles and
ear protection!