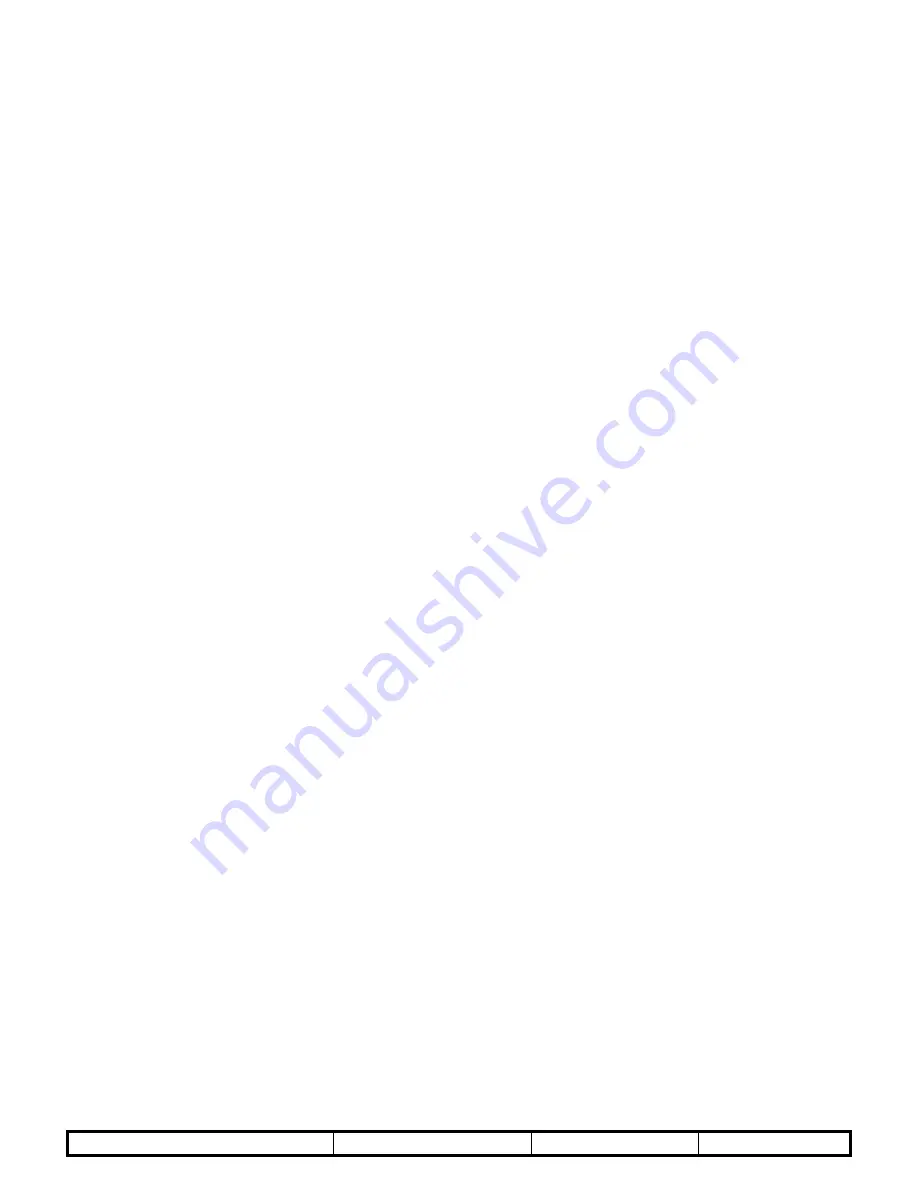
Document Number:
1900-0098
Issue Date:
01/15/08
Revision No:
003
Page:
14 of 44
POSSIBLE PROBLEMS
1.
The most common cause of valve failure is dirty oil. If debris becomes lodged in the
cartridge valves they will malfunction. Recommended filtration level is between 15 and
25 microns. Many systems filter the oil on the return side. This does not guarantee clean
oil going into the system. It is important to ensure that the tank vent filtration element is
properly maintained as well. Very small contaminants may not cause the valve to stop
functioning, but can cause “stiction” in the cartridges between the body and the moving
spool. This can cause improper operation. A slow moving tipper is most likely the result
of contamination in the flow regulator cartridge. A pulsating noise may be the result of
contamination in the differential pressure sensing valve causing it to stick. If any valve
malfunctions, remove and thoroughly clean the valve, being extremely careful not to score
or abrade the “o” ring seals or moving parts of the valve. Be sure that the spool moves
freely in the valve body.
2.
The flow regulator cartridges (FR1 and FR2) are designed to operate at a designated
pressure of 80 psi. This means that in order for the valve to function properly, a minimum
of 80 psi is required from the supply line through the “IN” port of the valve. This can
present a problem on trucks with a dry valve pump system. Normally in the dry (off)
mode of the pump, a flow of approximately 2 gpm at 20 psi is required to circulate
through the open center system of the truck. This is for pump lubrication in the off mode.
When the diverter valve is placed in the main pressure line of the truck, a blockage occurs
because of the differential pressure sensing valve needing 80 psi to initially open and
allow the flow regulators function. The path of the lubrication oil is therefore stopped
because the valve does not open. When the oil is blocked, the pump will rotate and
cavitate in the lubricating oil, causing heat to build up over an extended period of time,
possibly leading to premature pump failure. To prevent this problem from occurring, a
“bleed line” circuit needs be installed on the truck to allow passage of the lubricating oil
back to tank.
3.
On front load residential truck applications, several considerations need to be noted. The
Bayne hand valve is an open center valve that allows for the lifter circuit to maintain flow
through the hand valve and back to the diverter valve when the lifter is not being operated.
If flow is not maintained through the hand valve, the oil will constantly be relieving over
the lifter circuit relief valve (RV) in the diverter valve, which can cause an increase in
operating temperature. Certain front load box designs allow for the hand valve to be
located on the arms of the truck which keeps the hand valve in the lifter circuit at all times
to maintain flow. Most problems occur with applications where the hand valve is located
on the box itself. In this situation, when the operator disconnects the hydraulic lines to the
box, a blocked condition occurs in the lifter circuit. To prevent this problem, the pump
must be turned off prior to disconnecting the box hydraulic lines. Once the lines have
been disconnected from the box, it is necessary to connect the two lines for the hand valve
to each other to functionally complete the lifter circuit. It is recommended that male and
female quick disconnects be used opposite each other on the truck to provide an
uninterrupted circuit. Once the lines have been connected and the circuit continued, the
pump could then be turned on to continue operations.
Summary of Contents for Thinline DTL 1116
Page 29: ...Document Number 1900 0098 Issue Date 01 15 08 Revision No 003 Page 29 of 44...
Page 30: ...Document Number 1900 0098 Issue Date 01 15 08 Revision No 003 Page 30 of 44...
Page 31: ...Document Number 1900 0098 Issue Date 01 15 08 Revision No 003 Page 31 of 44...
Page 32: ...Document Number 1900 0098 Issue Date 01 15 08 Revision No 003 Page 32 of 44...
Page 33: ...Document Number 1900 0098 Issue Date 01 15 08 Revision No 003 Page 33 of 44...
Page 34: ...Document Number 1900 0098 Issue Date 01 15 08 Revision No 003 Page 34 of 44...
Page 35: ...Document Number 1900 0098 Issue Date 01 15 08 Revision No 003 Page 35 of 44...
Page 36: ...Document Number 1900 0098 Issue Date 01 15 08 Revision No 003 Page 36 of 44...
Page 37: ...Document Number 1900 0098 Issue Date 01 15 08 Revision No 003 Page 37 of 44...
Page 38: ...Document Number 1900 0098 Issue Date 01 15 08 Revision No 003 Page 38 of 44...
Page 39: ...Document Number 1900 0098 Issue Date 01 15 08 Revision No 003 Page 39 of 44...
Page 40: ...Document Number 1900 0098 Issue Date 01 15 08 Revision No 003 Page 40 of 44...
Page 41: ...Document Number 1900 0098 Issue Date 01 15 08 Revision No 003 Page 41 of 44...
Page 42: ...Document Number 1900 0098 Issue Date 01 15 08 Revision No 003 Page 42 of 44...
Page 43: ...Document Number 1900 0098 Issue Date 01 15 08 Revision No 003 Page 43 of 44...
Page 44: ...Document Number 1900 0098 Issue Date 01 15 08 Revision No 003 Page 44 of 44...