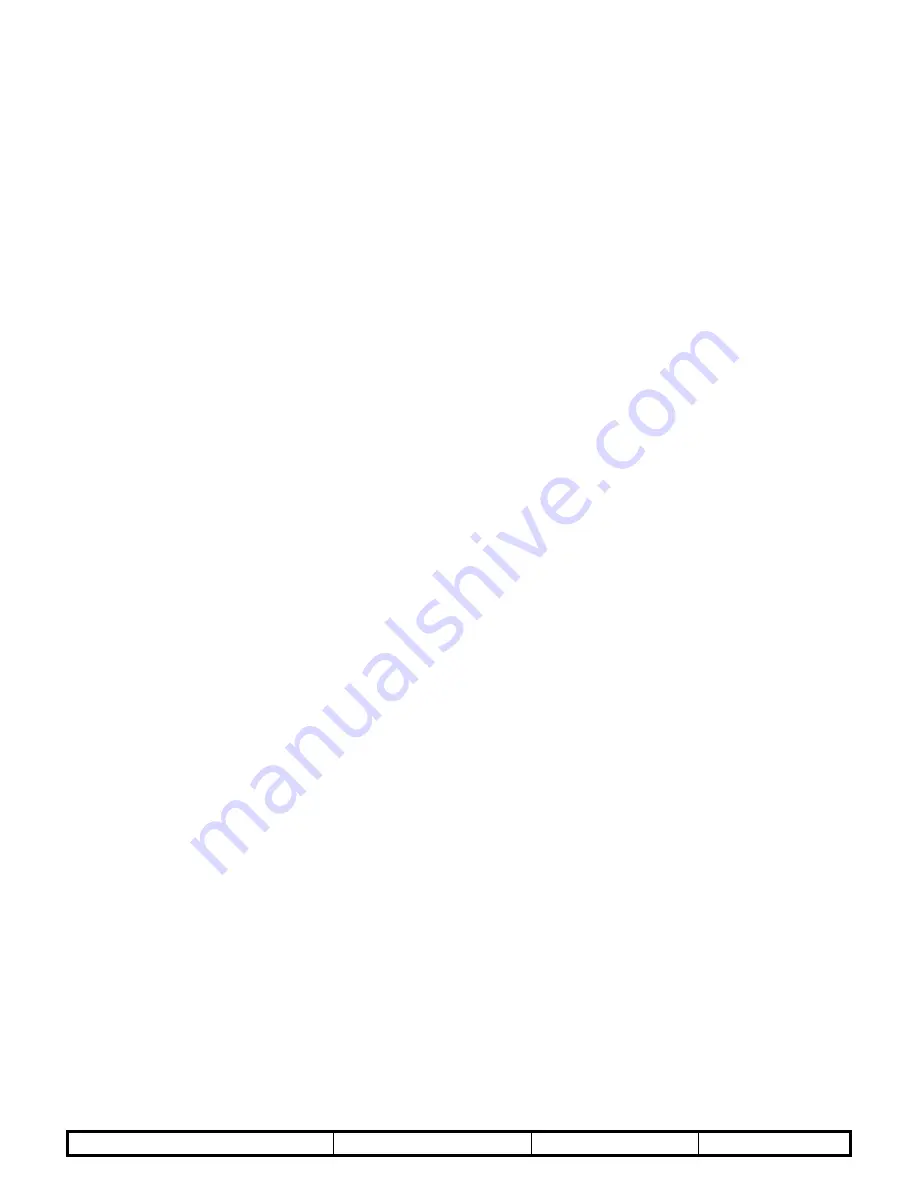
Document Number:
1999-0212
Issue Date:
06/06/07
Revision No:
005
Page:
3 of 38
SPECIFICATIONS ( WI-0087-B )
Bayne
THINLINE
®
Premium Lift Systems
A.
Rotary Actuator - rack and pinion style design.
•
Rack, pinion, and shaft bearings are constantly lubricated by the hydraulic oil for
extended life.
•
Body and caps are made of high quality ductile iron.
•
Pinion output shaft and racks are made of high tensile alloy steel.
•
The rotary actuator provides smooth motion throughout the lift cycle, which results in
longer cart life with virtually no cart damage or abuse.
B.
The BTL 208-12 lift unit measures as little as 5 3/4” thick from the back of the mainframe
to the front of the lift saddle in the down position. The unit also rotates underneath the
hopper to allow for easy dumping of large commercial containers without interference.
C.
The BTL 208-12 faceplate is normally at 45 degrees in the dump position in order to
completely eject all materials into the hopper.
D.
The BTL 208-12 lift unit operates at a cycle time of
8 to 10 seconds
for safe, fast,
efficient service.
Note : Cycle time is controlled by flowrate, as flowrate increases, cycle time decreases. In
order to avoid injury and maintain manufacturer’s warranty never operate outside
the cycle time listed above
E.
Recommended flow rate is
1 1/2 to 2 GPM
.
F.
Hydraulic pressure requirements are as follows:
•
2000 to 2500 PSI
normal working pressure
•
3000 PSI
maximum pressure
G.
BTL 208-12 lift units can be a bolt on type installation for easy, quick maintenance and
less downtime.
H.
All parts are manufactured and kept in stock at Bayne Machine Works, Inc. for fast
response to customer requests.
I.
Two ( 2 ) year limited warranty from date of delivery on all units and models when
properly maintained and operated within the recommended cycle time.
All lift units and parts are inspected by our Quality Control Department before shipment to
insure that you always receive the highest quality available in the lift business.
For more information, please contact us at 1/800/535-2671 or by fax at 1/864/458-7519.
Summary of Contents for Thinline BTL 208-12
Page 28: ...Document Number 1999 0212 Issue Date 06 06 07 Revision No 005 Page 28 of 38...
Page 29: ...Document Number 1999 0212 Issue Date 06 06 07 Revision No 005 Page 29 of 38...
Page 30: ...Document Number 1999 0212 Issue Date 06 06 07 Revision No 005 Page 30 of 38...
Page 31: ...Document Number 1999 0212 Issue Date 06 06 07 Revision No 005 Page 31 of 38...
Page 32: ...Document Number 1999 0212 Issue Date 06 06 07 Revision No 005 Page 32 of 38...
Page 33: ...Document Number 1999 0212 Issue Date 06 06 07 Revision No 005 Page 33 of 38...
Page 34: ...Document Number 1999 0212 Issue Date 06 06 07 Revision No 005 Page 34 of 38...
Page 35: ...Document Number 1999 0212 Issue Date 06 06 07 Revision No 005 Page 35 of 38...
Page 36: ...Document Number 1999 0212 Issue Date 06 06 07 Revision No 005 Page 36 of 38...
Page 37: ...Document Number 1999 0212 Issue Date 06 06 07 Revision No 005 Page 37 of 38...
Page 38: ...Document Number 1999 0212 Issue Date 06 06 07 Revision No 005 Page 38 of 38...