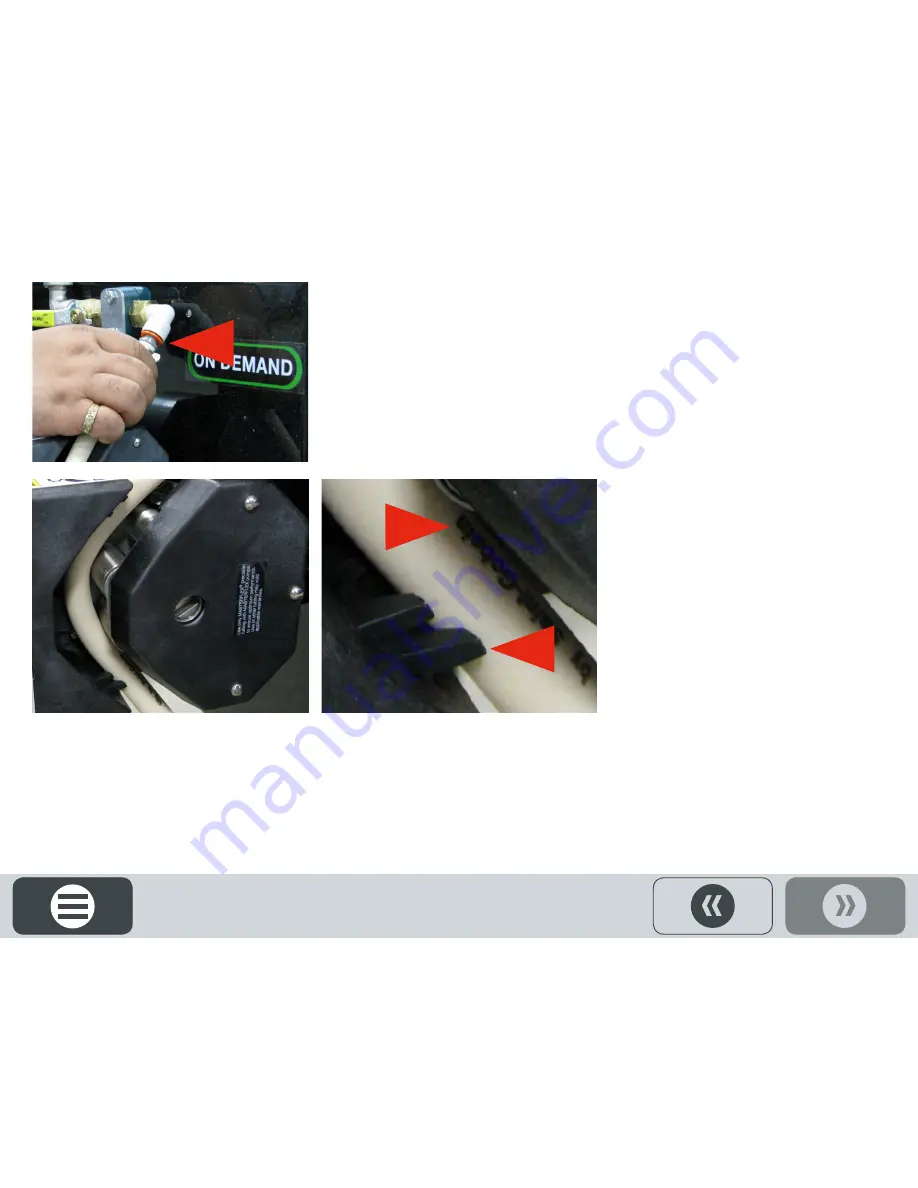
Step 2:
Use the correct element with the right Pump.
• LS uses 15 (small), IP uses 73 (large).
• Insert one end of the factory supplied Pump Element into the orange Fitting Receptacle on the Pump Treatment Valve
Vibration Mount, as shown.
Step 3:
Insert the Pump Element onto the Pump Head
Rollers, as shown.
• Ensure Pump Element fits behind Pump Head Clips
15