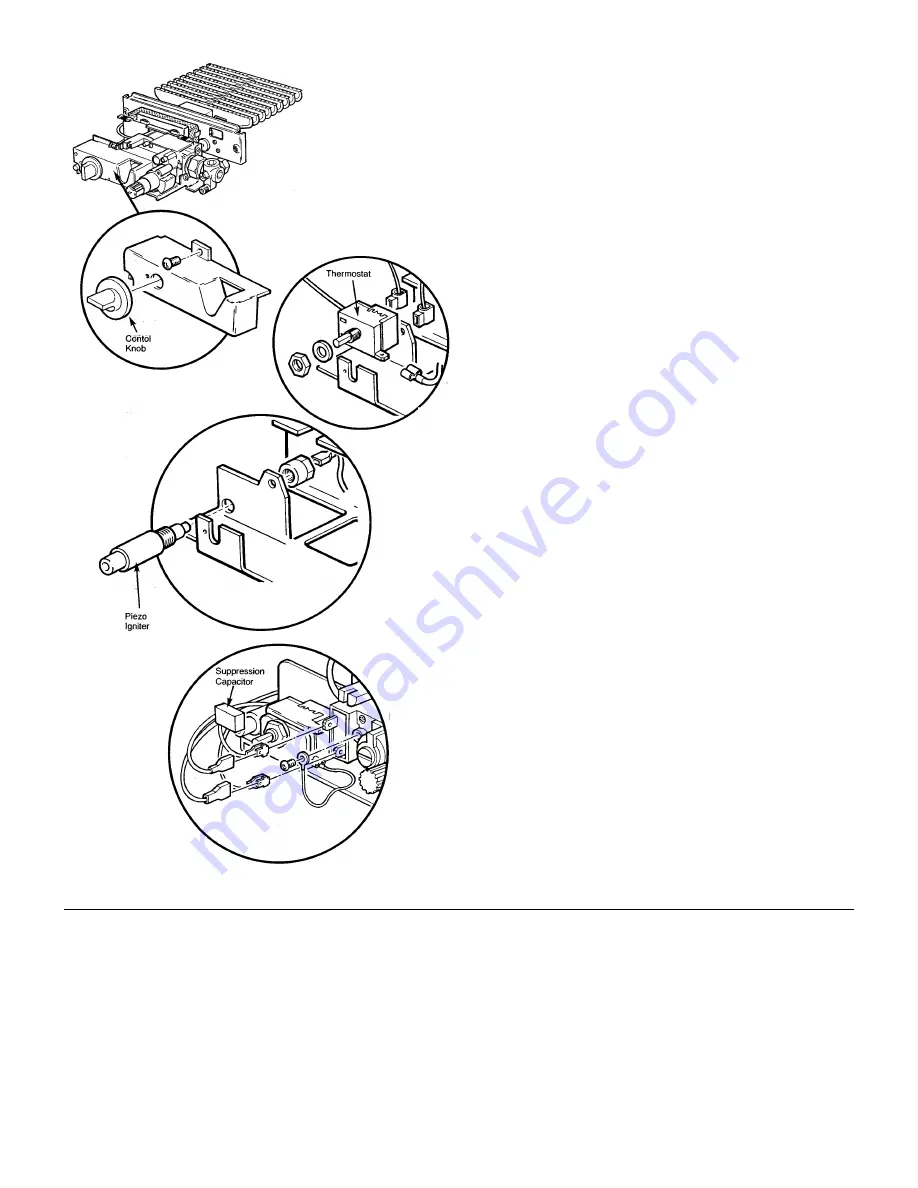
CHANGING COMPONENTS - Page 33
Thermostat
MANUAL CONTROLS ONLY
Remove the control knob. Undo the screw retaining the
valve cover and remove the cover.
Undo the locknut retaining the thermostat to the controls
mounting bracket. Ease the thermostat away from the
bracket and disconnect the electrical connections noting
their positions.
Reassemble in reverse order.
Piezo Igniter Unit
MANUAL CONTROLS ONLY
Remove the controls heat shield from its retaining clips if not
already done so.
Remove the control knob. Undo the screw retaining
the valve cover and remove the cover.
Pull the igniter lead off the piezo and undo the
plastic locknut. Remove the piezo igniter unit.
Reassemble in reverse order.
Suppression Capacitor
MANUAL CONTROLS ONLY
The controls may remain in situ but the controls heat shield
must be removed from its retaining clips.
Remove the control knob. Undo the screw retaining the
valve cover and remove the cover.
Note the positions of the electrical connections on the valve
and remove them.
Remove the capacitor connections from the
valve
Reassemble in reverse order.