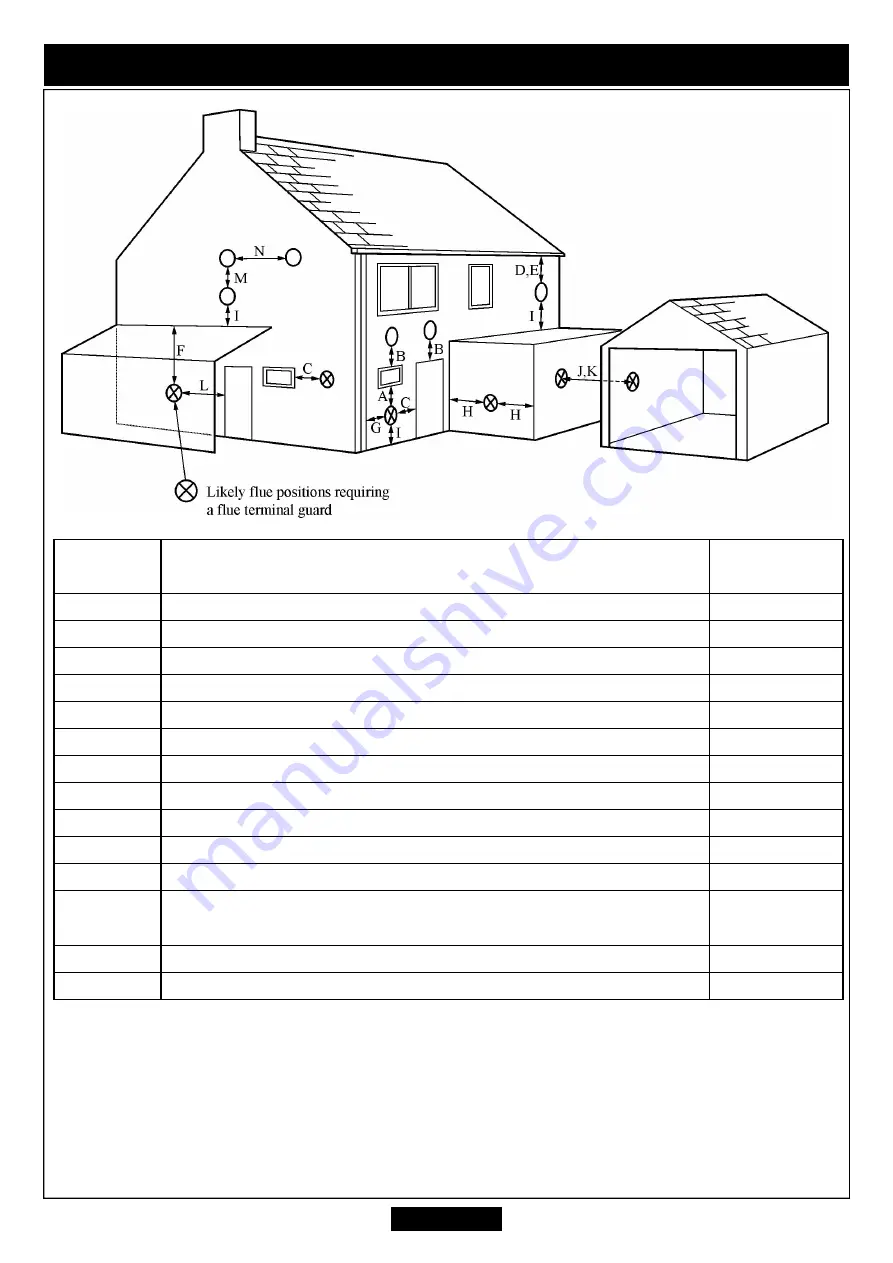
Page 10
INSTALLER GUIDE
Figure 3
Dimension
Terminal Position
Minimum
Distance
A*
Directly below an opening, air brick, opening window etc.
300mm
B*
Above an opening, air brick, opening window etc.
300mm
C*
Horizontally to an opening, air brick, opening window etc.
300mm
D
Below gutters, soil pipes or drain pipes
75mm
E
Below eaves
200mm
F
Below balconies or car port roof
200mm
G
From a vertical drain pipe or soil pipe
150mm
H**
From an internal or external corner
200mm
I
Above ground, roof or balcony level
300mm
J
From a surface facing the terminal
600mm
K
From a terminal facing the terminal
1200mm
L
From an opening in a car port (e.g. door, window) into
dwelling
1200mm
M
Vertically from a terminal on the same wall
1500mm
N
Horizontally from a terminal on the same wall
300mm
*In addition, the terminal should not be nearer than 150mm to an opening in the building
fabric formed for the purpose of accommodating a built-in element such as a window frame
or door frame (See figure 3b).
** The reference to external corners does not apply to building protrusions not exceeding
450mm, such as disused chimneys on external walls.