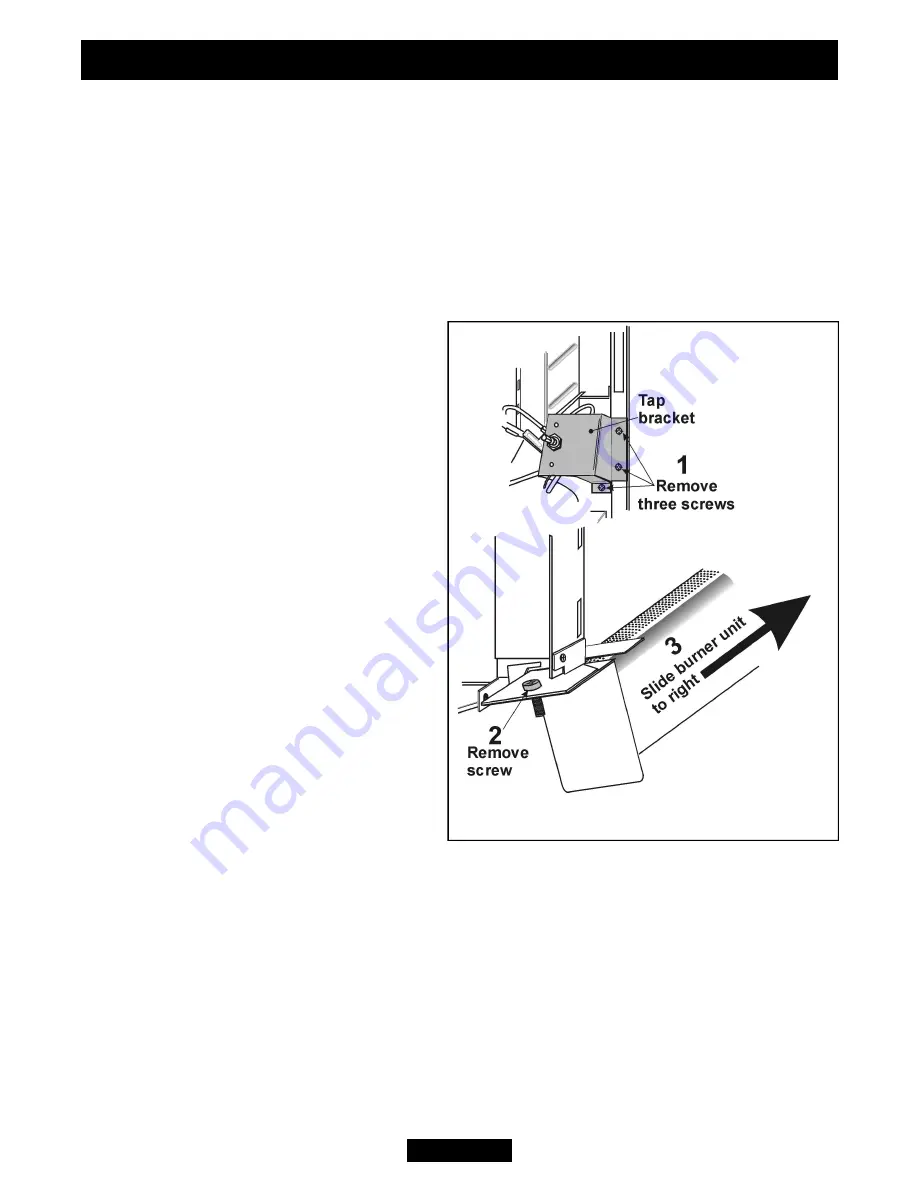
9.5 To remove the piezo generator.
9.5.1
Remove the gas tap as section 9.4.
9.5.2
Make sure that the tap is in the off position.
9.5.3
Remove the circlip holding the piezo unit to the tap. Remove the piezo unit.
9.5.4
Replace in the reverse order.
9.6 To grease the control tap.
9.6.1
Detach the tap and remove the piezo generator as section 9.5 making sure that the
tap is in the ‘off’ position.
9.6.2
Remove the two screws from the
head of the tap. Remove the niting head
and spindle complete with collar and
spring.
9.6.3
Note the position of the slot in the
plug - mark its position on the tap body.
9.6.4
Remove the plug rotating slightly
while pulling.
9.6.5
Clean and grease the plug lightly
with suitable grease. Do not apply
excessive grease. Particularly, make sure
that the gas ports in the tap are not
restricted by grease.
9.6.6
Push the plug into the tap body and
position the slot in line with the mark
previously made on the tap body.
9.6.7
Reassemble the niting head and
spindle complete with collar and spring
making sure that the components are
correctly engaged. Check the operation of
the tap.
9.6.8
Refit the piezo generator.
9.7 To remove an injector.
9.7.1
Remove the fascia as section 9.2.
9.7.2
Release the pipe compression fitting to the upper or lower injector as required.
Lock the injector with a second spanner to ensure that it does not move.
9.7.3
Loosen the pipe compression fitting at the tap end and move the pipe clear.
9.7.4
Remove the injector from the burner.
9.7.5
Replace in the reverse order.
Page 25
INSTALLER GUIDE
©
Baxi Heating U.K. Limited 2007.
Figure 15. Burner module removal