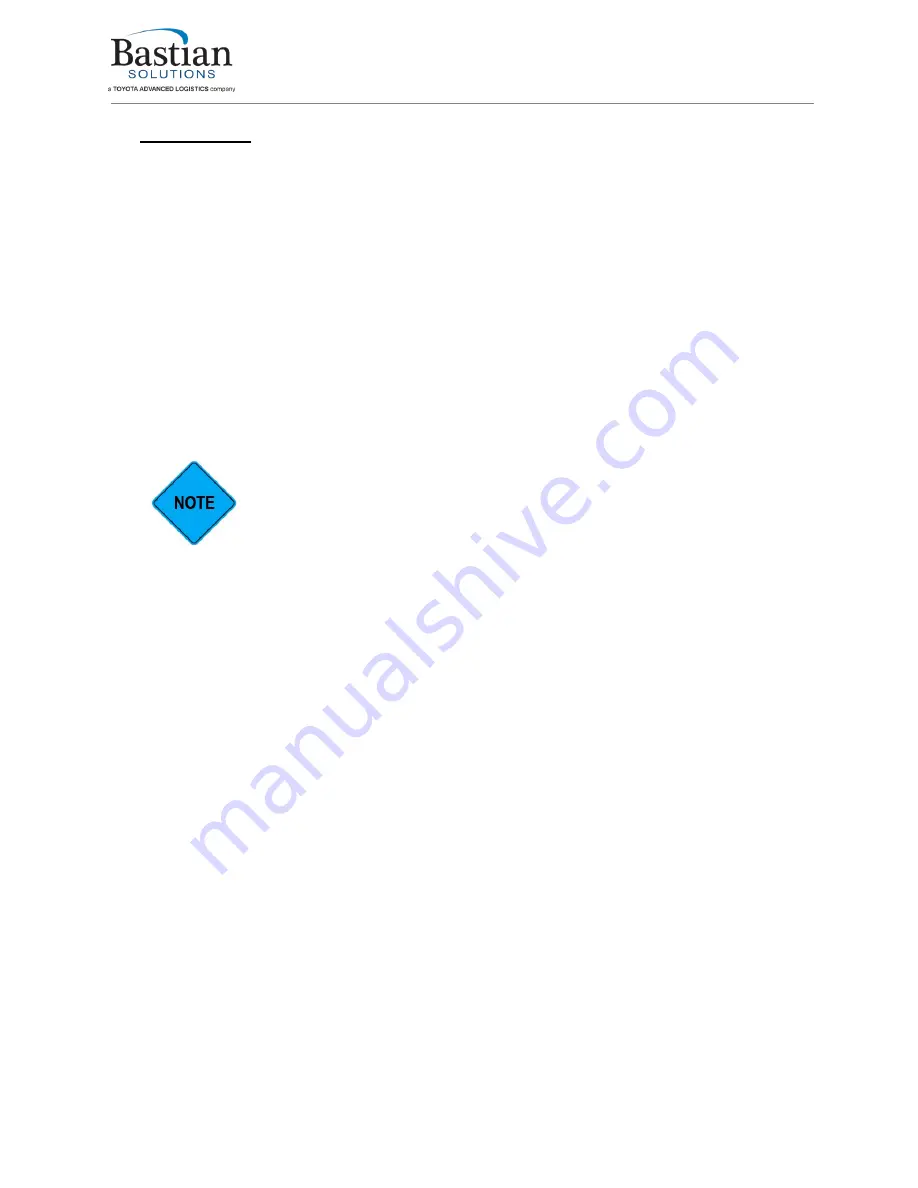
Installation and Maintenance Manual: RLCDC
Published January 2022
Rev. B Rev. B
10
5 Installation
The installation supervisor should have elevation and layout prints with detailed information regarding the
placement of conveyor sections and support structures. This information is not the responsibility of
Bastian Solutions to provide unless otherwise specified.
1. Clear the workspace around the portion of the layout selected for installation.
2. Measure out from a constrained origin to start placement of supports.
3. Use elevation layouts to determine the conveyor’s top of conveying surface.
4. Place the support type that the layout designates. Each support type has a corresponding mark
sticker.
5. Check the flow direction on the mark stickers to ensure that conveyors are mounted properly.
6. Place the conveyor onto the support structure and fasten it securely using the 3/8”-16 carriage
bolts and wiz nuts provided. The recommended torque specification is 26ft-lbs.
7. Attach any guiderail or miscellaneous accessories. For information on guiderail installation,
please reference the “Bastian Solutions Conveyor Side Cover and Guiderail Installation Manual”
8. Check that the height of the infeed and discharge ends are correct per the system layout. If
installed properly, the curve should be level.
9. Lag the supports to the floor (or other permanent fixture).
Refer to the “Bastian Solutions Conveyor Support Installation Manual” for
more information on installing conveyor.