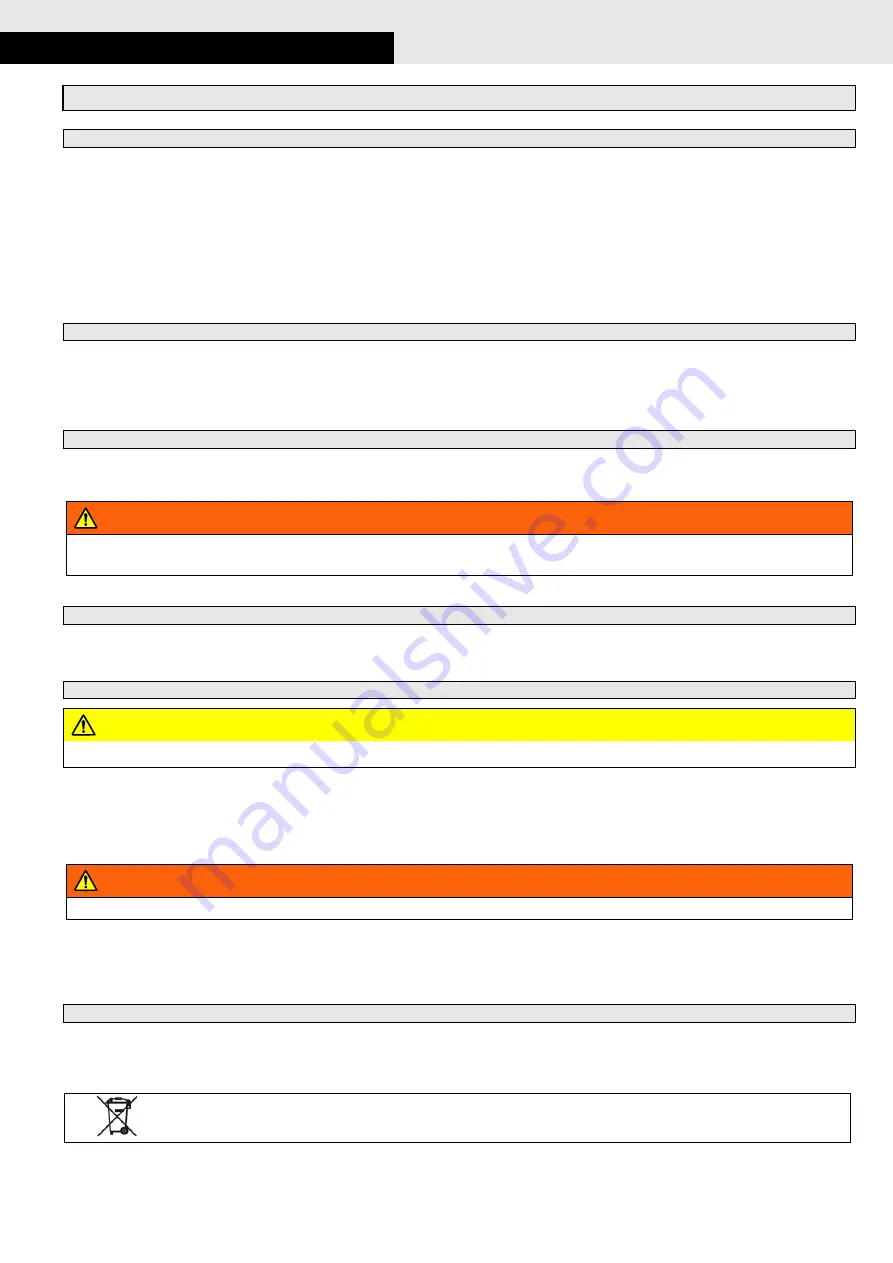
Design Guide for Hazardous / Industrial
Self-regulating trace heating systems
21-5400-7D0001/-
05/2023-EHT-466854
Notice Technical data subject to change without notice.
No claims for damage arising from alternations, errors or misprints shall be allowed.
Page 36 / 40
Maintenance
Visual and functional inspection
Regularly check the thermal insulation for possible damage, missing seals, cracks, damage to the outer jacket, missing thermal insulation bushings
for trace heaters and cables, penetrated water or chemicals. If the thermal insulation is damaged the trace heater should be checked for possible
damage.
Damaged trace heaters must be replaced.
Parts subject to wear must be replaced (e.g. seals, locking plates etc).
Check junction boxes, splices, end terminations etc. for corrosion and possible mechanical damage. Make sure that all enclosure covers are
properly in place.
If present, check the temperature controller connecting cables and sensors for damage and that their installation is protected against mechani-
cal damage.
Electrical inspection
Measurement of the insulation resistance should be seen as a permanent part of regular maintenance. For instructions on how to perform the
test refer to section Measurement of the insulation resistance on prior pages.
Upon completion of maintenance/repair/modification, the insulation resistance of the trace heater shall be measured and recorded after instal-
lation and shall not be less than 20 MOhm.
Inspection intervals
For frost protection installations inspections should be carried out annually before the heating period begins.
For systems designed to maintain process temperatures, inspections should be carried out at regular intervals, but at least twice a year.
WARNING
Risk of serious injury due to electrostatic charging.
For plastic type label electrostatic charging hazard exist. Only wet cleaning is allowed.
Personnel training courses
Regular maintenance should be carried out by trained, experienced maintenance personnel.
It is recommended that maintenance personnel is updated on new developments in application technology and maintenance.
Repairwork on piping or thermal insulation
CAUTION
Consult the trace heating system documentation prior to maintenance/repair/modification.
Ensure that all safety procedures and precautions in the area for repairs are followed.
Take care that the heat tracing system is not damaged during repairwork on the pipes or insulation.
After completion of the repairwork:
Make sure that any repaired heating circuits are properly installed and tested according to the project planning documentation.
WARNING
Risk of fire or electrical shock due to damaged components. Remember that self-regulating trace heaters are designed to be installed only once.
Carry out a visual, functional and electrical test (refer to section Tests and commissioning on page 34).
Test the operation of the earth-fault device of each affected circuit” or equivalent.
In the event of an earth fault or over current interruption, the device shall not be reset until the cause of the trip has been investigated by
qualified personnel” or equivalent.
Disposal and Recycling
Each product of the heating system must be disposed of properly in accordance with legal regulations. The main components are glass-fibre
reinforced plastic, metal and electrical components. Each product must be disassembled into its components and fed into the recycling system in
accordance with its components.
Disposal
The appliance must be disposed of in accordance with local laws and regulations according to its components.