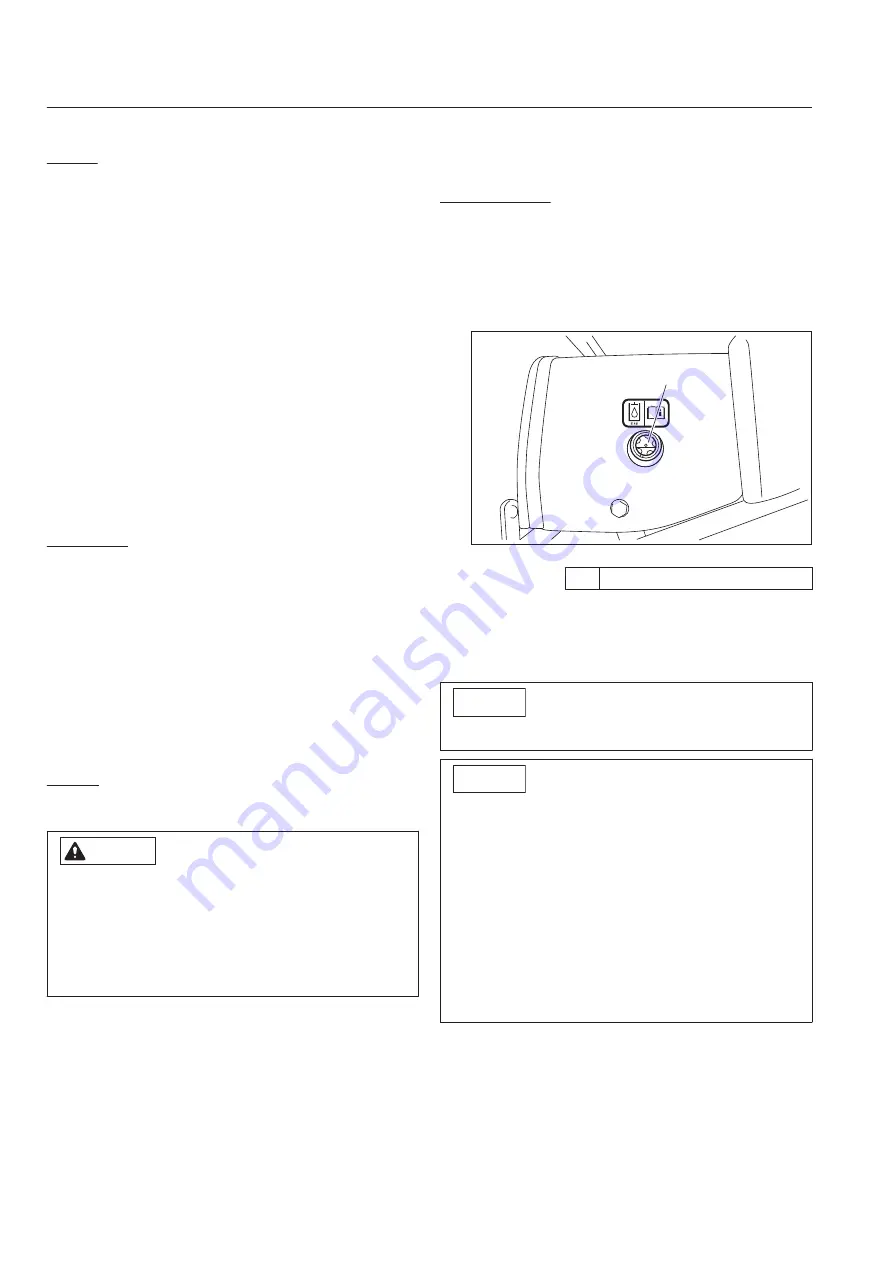
Roller
Inspection of Rollers
Bearing wear due to frequent use or bearing
damage caused by water infiltration may
prevent the roller from rotating smoothly.
Inspect the roller and, if necessary, replace
parts such as oil seals and bearings.
Make sure that there is no abrasion nor
adhesion of the roller.
Make sure that there is no wear of the roller
shaft.
Make sure that there is no wear nor
damage of the oil seal.
Make sure that there is no wear nor rust of
the bearing.
Make sure that there is no play in the roller
shaft.
Outrigger
Inspection of Outrigger
The outriggers may happen to be damaged
during traveling, etc.
Inspect and, if necessary, repair or replace.
Make sure that there is no bend or
deformation.
Make sure that there is not damage or
deterioration.
Make sure that the pin is not missing.
Cover
Inspection of Covers
Caution
If you have removed a protective cover during
inspection, be sure to securely install it in its
original position.
If a protective cover remains removed, foreign
objects may fly off, possibly resulting in
injuries.
Make sure that there is no wear or
deterioration of protective covers.
Make sure that there is no damage to
protective covers.
Make sure that there is no interference with
moving parts due to deformation of
protective covers.
1.
2.
3.
4.
5.
1.
2.
3.
1.
2.
3.
Make sure that protective covers are
installed in their appropriate positions.
Hydraulic Oil
Inspection of Hydraulic Oil
On a level surface, lower the brush frame
and the bucket and maintain that position.
Make sure that the oil level is at the middle
of the oil gauge.
1
olekci-001
Inspection of Hydraulic Oil_001
1
Oil gauge
Check underneath the machine for oil
leakage.
Hydraulic Oil Supply
Important
Do not mix different types of oil.
Important
Use Shell Tellus S2M46 (or equivalent) as
hydraulic oil.
In case of an equivalent, consult
Characteristics of Hydraulic Oil and use
hydraulic oil whose characteristics are
superior to those of the specific hydraulic oil.
Especially regarding kinematic viscosity and
viscosity index, use of hydraulic oil whose
figures are less than those of the specified
hydraulic oil will cause a malfunction in the
hydraulic circuit.
Note:
Characteristics of Hydraulic Oil
4.
1.
2.
3.
FS900
Handling Instructions
Page 5-6
Inspection and Cleaning